Old is gold: product makeovers with recycled plastics
Post-consumer plastics offer value to various industries, such as the packaging, automotive and furniture sectors, as they unravel their sustainability agendas, aided by new technologies, says Angelica Buan in this article.
The market for post-consumer recycled materials (PCR) continues to grow as adoption increases, thanks to policies that promote the use of PCR and increase its use across industries. Based on a study by Towards Packaging released this year, the global PCR plastic packaging market size is expected to reach US$64 billion by 2030, climbing to nearly US$73 billion by 2032—a 60% increase from the projected US$44.6 billion in 2024.
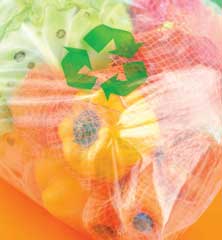
In line with the United Nations (UN) 2023 global commitment report, there is a call to action to raise the target percentage of PCR material across all plastic packaging used, with a goal of 26% by 2025. Sourcing may, however, become difficult when considering that these targets will probably increase even further in the upcoming years.
Furthermore, according to a World Economic Forum (WEF) article on responsible sourcing of PCR, the lack of data and transparency surrounding PCR plastic and other materials leads to irresponsible sourcing. Notably, sourcing is impacted by inadequate collection, transparency of sources, limited waste management infrastructure, and the labour conditions of informal waste pickers.
Technologies for improving recycled output
New technologies are being developed to help industries meet global PCR content targets. These innovations focus on improving the efficiency and quality of recycling processes and recycled materials, enabling the use of more recycled materials in manufacturing.
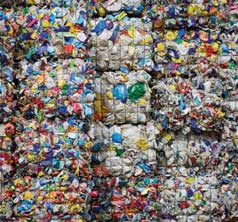
Austrian chemical company OMV and polyolefins provider Borealis have entered into long-term feedstock supply agreement for their recycling facilities with Tomra Feedstock, a subsidiary of sorting technology producer Tomra.
Tomra has pioneered a process that transforms presorted mixed plastic waste into clean, specific polymer types, which can then be further processed in mechanical/ chemical recycling plants.
OMV will process feedstock supplied from Tomra plants in its ReOil facility in Schwechat, Austria, while Borealis will process feedstock produced by Tomra at its mechanical recycling operation in Europe. The feedstock will be produced from mixed PCR material at a first-of-itskind sorting facility currently being developed by Tomra in Germany.
OMV is also constructing a new ReOil plant at the same site with a capacity of 16,000 tonnes/year, while Tomra is building a sorting plant in Germany with a capacity of 80,000 tonnes/year, expected to be operational by the end of 2025.
Packaging redefined with biobased materials
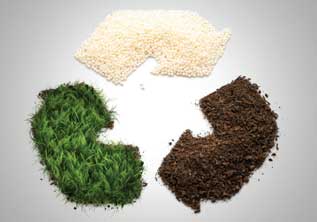
Packaging design is changing as a result of the use of waste and renewable-based materials, especially when considering sustainability. A noticeable trend in the packaging industry is the use of renewable resources like organic waste and biomass in the development of packaging solutions, as environmental responsibility becomes more and more important. Players in the materials business are driving this shift by making investments in cutting-edge technology to produce packaging that not only satisfies functional needs but also has a minimal environmental impact.
German chemical firm BASF is offering the packaging industry a pathway to increase the use of renewable feedstocks, by having expanded its portfolio of certified compostable biopolymers to include a biomass-balanced (BMB) ecoflex, a polybutylene adipate terephthalate (PBAT) commonly used in biopolymer compounding. For the new ecoflex F Blend C1200 BMB, fossil raw materials typically used in production are replaced with renewable feedstock at the beginning of the value chain.
The biomass-balanced ecoflex not only reduces reliance on fossil resources but also achieves a 60% lower Product Carbon Footprint (PCF) compared to standard ecoflex F Blend C1200, adds BASF.
(PRA)SUBSCRIBE to Get the Latest Updates from PRA Click Here»