Additives: Next generation additives redefining sustainability
Evolving standards for plastic products, focusing on performance, application, quality, and material guideline compliance, are driving advancements in additives, highlighting their critical role in modern manufacturing, adds Angelica Buan in this report.
Sustainable additives in a growth mode
Innovative additive technologies are fast emerging, with the potential to disrupt the polymer sector. Meanwhile, sustainable additives are gaining a significant market share.
According to a Lucintel report, the global green polymer additive market is set to grow along with the rising demand in packaging, injection moulding, automotive, and biopolymers. Growth is projected at a CAGR of 6-8% from 2022-2027, fuelled by a preference for biobased plastics, stringent environmental regulations, and cost-effective green polymers.
The packaging segment is expected to lead the market, with Asia Pacific experiencing the highest growth due to demand for sustainable packaging films and an expanding plastics industry in countries like China, Japan, India, South Korea, and Malaysia.
Stabilisers and coatings for recycled materials
South Korean additives manufacturer Songwon Industrial Co has developed a re-stabilisation technology, Songnox binary antioxidant blends, for materials containing mechanically recycled PCR content. These innovations allow recyclers to offer materials with improved melt flow, durable mechanical properties, and enhanced cost-efficiency.
Meanwhile, Songwon has also formulated a coating stabilisers range, which enhances durability and protect surfaces, adhesives, and sealants from the detrimental effects of light and heat. The latter includes a liquid hydroxyphenyl triazine (HPT) UV absorber, which is tailored to maximise performance, efficiency, and sustainability across various substrates.
Sustainable portfolio for the PU industry
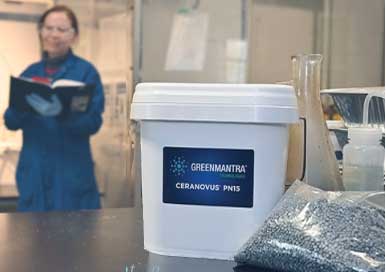
Elsewhere, Greenmantra Technologies, a Canadian molecular recycling company, offers its solutions for transforming hardto-recycle plastics into specialty polymer additives through a high-yield process that uses low heat and pressure.
Its Ceranovus specialty PP and PE additives act as melt flow modifiers in plastic applications, enhancing operational efficiency and productivity while using less energy. They also enable the incorporation of higher recycled content in plastic parts. Target applications include agricultural drainage pipes, conduits, plastic lumber and decking, as well as crates and pallets.
Greenmantra employs various molecular recycling methods, such as depolymerisation, methanolysis, hydrolysis, and pyrolysis, to create sustainable products. This approach involves a patented process focused on mid-size polymer molecules, like synthetic waxes, used as polymer additives. This strategy has successfully enabled Greenmantra to scale up production to commercial levels. Its target markets are for asphalt, plastic pipes, construction, and automotive parts sectors.
Along the same vein, German speciality chemicals firm Lanxess’s Adiprene Green line features polyether-based PU systems with renewable raw materials, expanding into adhesives, sealants, and one-component foam applications. These prepolymers are designed for safe handling with low free monomeric MDI content and comply with EU regulations, reducing environmental impact.
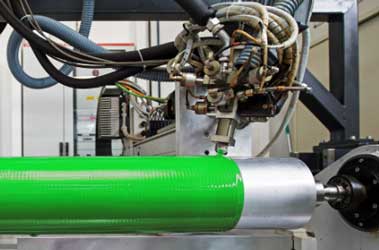
In adhesive, sealant, and OCF applications, Lanxess develops prepolymer grades with high NCO levels and low viscosity, underlining safety and compliance. Its Stabaxol stabilisers provide crucial hydrolysis protection in footwear and polyester-based cellular PU elastomers, enhancing product longevity under wet conditions.
Meanwhile, the firm’s Modulast range optimises physical properties and reduces material costs in TPU and CASE (Coatings, Adhesives, Sealants, Elastomer) applications, with products like Modulast PU meeting industry standards for colouration, odour, and elasticity.
Green opportunity with colourants
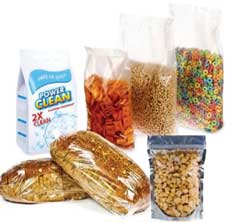
The plastic colourant market, encompassing compounds such as masterbatches, pigments, dyes, and additives, was valued at US$42 million in 2023 and is projected to reach nearly US$ 87 million by 2030. This represents a growth rate of 10% CAGR from 2024-2030, according to Verified Market Reports. Industry leaders like Milliken & Company, D&L Industries, and others are driving colourant innovations in the current year.
US-based Milliken is focused on enhancing PP and PE formulations to optimise the reusability, recyclability, and efficiency of plastics without compromising performance. Thus, it has introduced two new solutions: UltraGuard 2.0 and Hyperform HPN 58ei.
UltraGuard 2.0 builds on the established line of tailored PE masterbatches, significantly boosting barrier performance in HDPE and LLDPE by up to 70%. This advancement supports expanded options for mono-material packaging and facilitates material downgauging. Hyperform HPN 58ei enhances performance for PP sheets and thermoformed parts, delivering improved optical properties, isotropic shrinkage, and regrind quality, and is FDA-approved for food packaging.
Additionally, Milliken’s Millad NX 8000 platform, a PP clarifying agent, reduces energy consumption and cycle times during injection moulding with UL-certified energy savings of up to 10%. Meanwhile, its viscosity modifiers enhance the performance of recycled polypropylene (rPP) by improving melt flow rates, thereby broadening application possibilities for both pre- and post-consumer rPP materials.
In the Philippines, D&L Industries is advancing the circular economy through its subsidiaries First in Colours Incorporated (FIC) and D&L Polymer & Colours (DLPC). With over six decades of experience in the plastics industry, D&L specialises in manufacturing colourants and additives that enhance the physical and chemical properties of plastics across diverse sectors such as food and healthcare. The firm is responsible for pioneering technologies like Plastibond, Polyguard, and Deomate that enable plastic upcycling and customisation for specific applications.
President Lester Lao of FIC and DLPC conveyed the company's commitment to sustainable innovation, green chemistry promotion and assisting businesses in achieving sustainability objectives, including compliance with the country’s Extended Producer Responsibility (EPR) law.
Likewise, Swiss chemical firm Clariant has launched its AddWorks PPA product range for the polyolefin film extrusion market, aiming to enhance processability and optimise optical film qualities by addressing issues like sharkskin and dye build-up.
These additives, which maintain film tensile, mechanical, and sealing properties, while offering high thermal stability, low or no migration and low let down ratios, are free from inorganic content and silicone components, ensuring consistent high performance and compliance with PFAS regulations according to Miao Zhigang, Head of Clariant’s Polymer Solutions business.
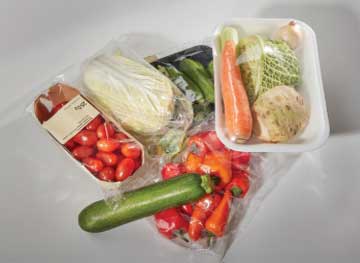
Additionally, Clariant’s AddWorks PKG 158 serve as an efficient antioxidant that protects colour and reduces thermal oxidative degradation during polymer conversion processes.
Eliandro Felipe, Head of Sales Americas for Additives Polymer Solutions, highlighted the benefits in enhancing processability and preparing resins for recycling, providing stability at high temperatures and minimising discolouration and plate-out.
Hot trend for flame retardants
Lucintel's flame retardants (FRs) additives market report indicates bright prospects for FRs within the global plastic additive market, fuelled by rising demand from the electrical & electronics industry, increased adoption of thermoplastics to curb carbon emissions, and stringent government regulations aimed at improving fire safety standards.
Strategic opportunities are anticipated across several industries including aerospace & defence, electrical & electronics, wires & cables, pipes & tanks, transportation, building & construction, and marine sectors. By 2028, the market for FRs in plastics is projected to reach about US$11 billion, growing at a CAGR of 5.7% from 2023-2028.
A prominent player in this segment, US specialty material solutions provider Trinseo, unveiled new FR grades of PC and PC/ABS resins at the recent Chinaplas 2024 show. These resins are manufactured without PFAS (per and polyfluoroalkyl substances) or halogenated additives and offer options with recycled content. They address the rising demand and regulatory pressures to reduce PFAS use, particularly in consumer electronics & electrical industries.
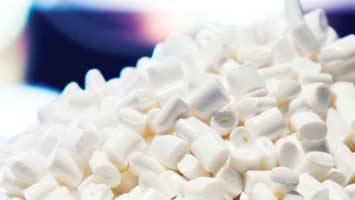
Trinseo’s line-up includes Emerge PC 8600PV and 8600PR resins, along with Emerge PC/ABS 7360E65 resins. These products maintain critical performance attributes such as heat, oil, stain, grease, and water resistance while meeting sustainability demands. Initially launched in the AsiaPacific market, they cater to applications in IT equipment, electronics, battery chargers, and voltage stabilisers.
Trinseo's Senior Vice President and Chief Technology Officer, Han Hendriks, affirmed the company’s direction to developing sustainable solutions by eliminating PFAS and halogenated additives from their products. Both Emerge 8600PR and Emerge 7360E65 utilise PCR substrates, maintaining performance comparable to virgin materials. This approach not only reduces waste but also lowers carbon footprint and promotes recycling in the consumer electronics sector.
According to Trinseo, it prioritises non-halogenated additives in manufacturing, ensuring UL94 V0 rating (1.5 mm) across all colours with high-temperature resistance and options for glossy or matte finishes. Emerge 8600PR, which includes recycled content, is said to offer excellent dimensional stability, impact resistance, a wide processing window, and UV resistance.
Meanwhile, Trinseo's Emerge PC/ABS 7360E65 FR products achieve UL94 V2 rating (0.5 mm) across all colours, boasting high flow properties ideal for thinwall applications. These products also deliver thermal stability, incorporate 65% recycled content, and ensure dimensional stability along with a wide processing window and UV resistance.
Similarly, Lanxess offers phosphorus-based Levagard and Disflamoll FR brands, as well as the reactive brominecontaining PHT4 diol. Levagard products are ideal for both rigid and flexible PU foams, offering solutions that enhance performance in rigid foam applications. Disflamoll phosphates provide effective flame retardancy and plasticising properties across various PU applications, according to Lanxess.
(PRA)SUBSCRIBE to Get the Latest Updates from PRA Click Here»