Separator film for li-ion batteries; adhering to quality and production methods
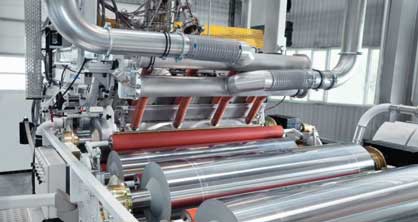
With the expansion of electromobility, the market for lithium-ion batteries is gaining rapidly in importance – and with it the demand for separator film. This is one of the most critical and expensive part in a lithium-ion battery, accounting for 15-20 % of the overall costs.
Over the last ten years, Austrian extrusion machinery maker SML has delivered more than 90 cast film lines for the production of premium separator film.
“It uses the efficient and environmentally friendly dry process. With this vast experience gained, we know in the meantime what really matters in this business,” Alexander Bruckmüller, Product Manager at SML explains.
But which functions does a separator basically have in a lithium-ion battery? Its main purpose is to keep the two electrodes apart to prevent electrical short circuits. Simultaneously, the separator allows the transport of ionic charge carriers that are needed to close the circuit during the passage of current in an electrochemical cell.
To fulfill these functions, separator film in lithium-ion batteries must meet a number of requirements:
- Free from gels, as any surface defect, unmolten or burnt particle in the film can cause holes after stretching. And this in turn causes short circuits.
- Thin-gauges and uniform thickness: Battery separator film (BSF) must be thin to facilitate the battery's energy and power densities. To support many charging cycles, its thickness must be uniform.
- Optimum porosity enables the electrolyte to be thoroughly moistened and ensures facile ionic conduction. Generally, commercial separators with pores of 1 micron or less have a porosity of 40-50 %.
- Adequate mechanical properties: to withstand physical stress caused by external compression and electrode expansion.
- Chemical stability: the separator must be an electronic insulator; additionally it must be electrochemically stable in the face of redox reaction potentials.
- Ability for a thermal shutdown at temperatures which are slightly lower than that, at which thermal runaways occur. During a shutdown, mechanical properties must be retained.
- Dimensional stability: the ability to keep shape over a wide temperature range without curling or warping, lying completely flat. Minimum thermal shrinkage in all directions.
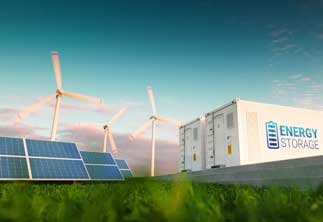
Cost-efficient manufacturing using the dry process
SML’s cast film lines for separator film fulfill these requirements “100%”, says the firm.
“Separator film can be made of different materials and can be produced in different processes. The most common processes are the dry and the wet process, and the most common raw materials are polypropylene (PP) and polyethylene (PE),” continues Bruckmüller.
On SML’s cast film lines, separator film is manufactured using the dry process. Compared to the wet production method, the dry process has significant advantages:
- Lower material costs: in the dry process, rather standard PP or HDPE resins are used. While in the wet process, relatively expensive, ultra-high molecular weight polyethylene (UMWPE) is applied.
- Fewer production steps: the dry process is more straightforward compared to wet process.
- More environmentally friendly: no solvents are required to create the pores, as it is necessary in the wet process.
- Much lower energy consumption: it is not necessary to evaporate the solvent and dry the film afterwards.
Next to the electromobility market, dry process separator film is in high demand for large-scale electricity storage at wind and solar power plants.
(PRA)
Subscribe to Get the Latest Updates from PRA Please click here
©2023 Plastics and Rubber Asia. All rights reserved.
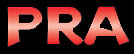
©2023 Plastics and Rubber Asia. All rights reserved.
Home Terms & Conditions Privacy Policy Webmail Site Map About Us