Additives: Circular developments in recycling additives
A new range of additives are helping recycled plastics producers meet the enhanced requirements for high quality recycled materials, says Angelica Buan in this report on additives.
Additives pump up polymers effectiveness
Additives are required to increase both the utility and quality of polymers; improving plastics' flexibility and workability with plasticisers, strengthening with reinforcements and fillers; improving their flowability with lubricants, and incorporating antistatic and conductive properties.
While additives can provide a variety of benefits to plastics, certain additives can be hazardous to the environment as well as posing risk to human health and ecosystems when these additives are exposed to heat or weathering, or that some may release heavy metals into the environment during the production, use, or disposal of plastics.
Even more, some additives used in plastics, such as fillers, pigments, flame retardants, and plasticisers, can contaminate the recycling process. During recycling, plastics are typically sorted and processed based on their resin type. If additives are present, they can interfere with the sorting process, making it difficult to separate and process different types of plastics effectively
The disruption in the recycling process can hinder efforts to reduce plastic waste and promote a circular economy.
Every year, around 400 million tonnes of plastics are produced, with packaging accounting for approximately 40% of the total. Only a small portion of this is recycled, with the vast majority ending up in landfills and incinerators after only one use, or being dumped into the environment.
Thus, the development of new recycling additives is vital for increasing not only recycling rates but also the quality of recycled plastics.
From waste to high value plastics
Demand for recycled polymers is increasing, owing mostly to rising consumer awareness and effective regulations. According to McKinsey's Advanced Recycling: Opportunity of Growth report, more than 80 global consumer packaged goods (CPG), packaging, and retail companies have made public commitments to achieve recycled content in their packaging ranging from 15 to 50% by 2025.
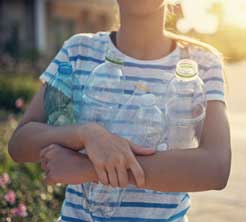
With the market shifting toward high-quality recycled plastic, additives are assisting recyclers in improving the quality of recyclates.
The Tego Cycle additives line from German specialty chemicals manufacturer Evonik attempts to convert plastic waste into valuable plastic materials. At a plastics recycling show in Europe in May, Evonik introduced a variety of additives, which can help customers enhance processes and raise the quality of recycled polymer and final plastics.
The Tego additive portfolio is designed to conserve energy during the mechanical recycling process while simultaneously improving polymer quality, allowing the plastics value chain to be transformed into a value cycle, Evonik said.
High costs and the technical challenge of producing quality polymers are causing comparably low recycling rates, according to Alper Aksit, Marketing Manager Compounds & Circular Plastics Region EMEA, Evonik, who also mentioned that Evonik’s initiatives like the Circular Plastics Program, which combined with its Tego additives can help speed up the plastic industry's transformation into a fully circular economy.
During the wet stage, Evonik's antifoams and wetting agents can be utilised to improve the efficiency of washing, separation, deinking, and drying processes, resulting in significant energy savings. Furthermore, during the compounding (dry stage), Evonik's odour absorbers, compatibilisers, dispersants, and processing aids help to optimise processing and polymer properties, resulting in lower costs and a considerably greater quality of recycled plastic content.
In addition, Evonik has also introduced its new organo-modified siloxane-based Tegomer Polymer Processing Aids (PPA) for converters wanting to replace typical PPAs made from fluoroelastomers in PE and PP processing.
Similarly, additives maker SI Group offers its Evercycle additives platform, which debuted in 2022 at a major trade show in Germany. According to SI, Evercycle enables process stability, colour control, and lower acetaldehyde levels for PET recycling and conversion. Its benefits for recycling polyolefins include process stabilisation and performance improvement, allowing for higher recycled content.
By enabling more plastics to be recycled back into the economy, making it possible consumer brands to increase the amount of recycled content, and allowing for multiple uses of their products to increase the sustainability of their products, SI's formulated additive solutions advance the transition to a more circular economy, according to Irfaan Foster, Market Development Director at SI Group.
Joey Gullion, Chief Commercial Officer at SI Group commented that the business continues to invest in innovation and provide new environmentally friendly products like Evercycle additives to the market, showcasing its capacity to assist clients in the shift to a circular economy
(PRA)
Subscribe to Get the Latest Updates from PRA Please click here
©2023 Plastics and Rubber Asia. All rights reserved.
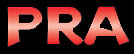
©2023 Plastics and Rubber Asia. All rights reserved.
Home Terms & Conditions Privacy Policy Webmail Site Map About Us