Coperion's side feeder allows for economical carbon-fibre recycling
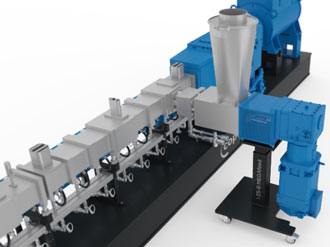
With the goal of making recycling of lightweight, high-volume fibre and flake recyclate much more economical and, in some cases even possible, German machine maker Coperion has developed a new version of its ZS-B side feeder. Using the innovative ZS-B MEGAfeed, plastic recyclate with a bulk density under 200 kg/m³, long considered intake-limited and thus not worth recycling, can be reliably fed in large quantities into Coperion’s ZSK twin screw extruder and be concurrently recycled and compounded.
The ZS-B side feeder’s novel design makes it possible to feed very high rates of fiber and flakes, such as PA, PE, PET, and PP. As a result, the ZSK twin-screw extruder’s high capacity can be fully exploited when the ZS-B MEGAfeed is used.
Coperion says high throughputs in both mechanical and chemical recycling of post-industrial and post-consumer waste are achieved.

With a ZSK 58 Mc18 twin-screw extruder, the throughput increase and thus the potential of the new ZS-B MEGAfeed becomes very clear. When recycling PA fibres with a bulk density of ~40-50 kg/m3, throughputs of 70 kg/hour were previously achieved using conventional equipment. When the PA fibres were fed into the ZSK extruder using the ZS-B MEGAfeed, throughputs increased about fourteenfold to 1,000 kg/hour. Similar results were achieved recycling carbon fibres with a bulk density of ~50-70 kg/m3; in this case, throughputs increased from 50 kg/hour to 2,500 kg/h using the ZS-B MEGAfeed. When recycling PCR flakes, throughputs increased from 50 kg/hour to 700 kg/hour, and from 80 kg/hour to 1,300 kg/hour with multilayer film flakes.
Plastics previously considered not recyclable are becoming a valuable raw material using the new Coperion ZS-B MEGAfeed. For example, PCR flakes or recyclate from carbon fibre-reinforced plastics can now be fed into the ZSK extruder at high feed rates and recycled economically, adds the Stuttgart-headquartered company.
In the case of mechanical upcycling, upstream processes necessary for compounding, such as compacting, melting and agglomeration, are completely eliminated using the ZS-B MEGAfeed technology. In this recycling process, flakes and fibers can be fed directly into the ZSK extruder, where they are melted, compounded, devolatilised, and filtered in a single step. In so doing, both investment costs and energy consumption drop. The production process becomes significantly more efficient. Moreover, the thermal product stress is reduced and recyclate quality increases.
Even when recycling PET, the feed rate is no longer a limiting factor. With the ZS-B MEGAfeed, PET flakes and fibres can be fed into the ZSK twin-screw extruder in large quantities with no pre-drying or crystallising, where they can be processed with the highest degree of profitability.
The ZS-B MEGAfeed can also feed large quantities of post-consumer waste, adding appreciable value to the chemical recycling process with the ZSKs. ZSK throughput rates are high with the ZS-B MEGAfeed. Preheating of the recyclate via mechanical energy input of the twin screws thus becomes even more economical for further processing in the reactor.
Coperion adds that existing extruders can be retrofitted with ZS-B MEGAfeed technology to greatly expand their spectrum of applications and increase their throughput rates.
Marina Matta, Team Leader of Process Technology Engineering Plastics at Coperion, is enthusiastic about the latest Coperion development: “We’re convinced that the new ZS-B MEGAfeed will play a pioneering role in plastics recycling. In particular, plastic fibres, which will be available in ever increasing quantities from textiles, had always been considered hardly recyclable until now. With the ZS-B MEGAfeed, this is now possible. Far more plastic waste can be recycled – and much more efficiently. For the plastics industry, the ZS-B MEGAfeed is another step forward on the path to a circular economy, and we are very proud of that.”
(PRA)
Subscribe to Get the Latest Updates from PRA Please click here
©2022 Plastics and Rubber Asia. All rights reserved.
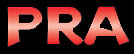
©2022 Plastics and Rubber Asia. All rights reserved.
Home Terms & Conditions Privacy Policy Webmail Site Map About Us