Eliminating microplastics with breakthrough innovations
The growing global problem of microplastics is prompting industry experts and companies to develop novel ways to banish microplastics from the environment, says Angelica Buan in this Materials News report.
Health-hazard particles up in the air
It is not a typical Hollywood film effect but microplastics falling from the sky are real – and should be taken seriously. Recent studies have shown that microplastics are no longer concentrated only in the oceans. Mismanaged wastes that are either landfilled or entering the oceans break down into tiny pieces, and are circulated in the atmosphere.
One recent study by researchers at Cornell and Utah State Universities says that microplastics from the oceans, roads and agricultural soils are purged into the atmosphere via mechanical processes. The airborne 2.5 micron or less in size microplastic wafts from urban areas to remote areas. The study, published in the Proceedings of the National Academy of Sciences (PNAS), found this plastic cycle to be similar to the biogeochemical cycles of water or nitrogen.
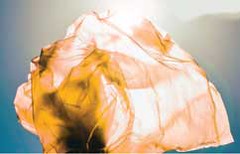
Inhaling contaminants is certainly bad for health, adds a study done by researchers from the Florida State University (FSU). Published in Chemical Research in Toxicology, the study says that exposure to microplastics, even only for a few days, may disrupt the lung’s cellular function. The team led by FSU Professor of Chemistry and Biochemistry Amy Sang, research specialist Joan Hare, doctoral students Kerestin Goodman and Timothy Hua, and former FSU graduate student Zahraa Khamis, exposed lung cells in a petri dish to small amounts of PS, used in common disposable items.
The experiment showed that microplastics can slow down the lung cells’ metabolism and growth; as well as alter the shapes. Declustering also occurred so that gaps existed in what is typically a solid sheet of cells. Additionally, the rapid migration of the plastics towards the nucleus resulted in the microplastic particles forming a ring around the cell’s nucleus, raising concerns that will be a focus of succeeding studies.
The findings may be helpful to understand the effect of microplastics, particularly for individuals with respiratory disorders like lung cancer, asthma, emphysema, pneumonia, fibrosis or chronic obstructive pulmonary disease (COPD), they said.
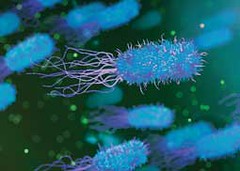
The team also added that while the experiment exposed the lung cells to common environmental levels of microplastics, they were directly exposed to the cells in a liquid solution. “The process of breathing in and out could not be mimicked and could potentially affect the amount that an individual inhales and ingests,” the researchers said.
Eliminating microplastics with microbes
Researchers have found various routes in removing microplastics from the environment, from deploying microbes to seize plastic particles to filtering microplastics at source, especially from wastewater that has been found to be highly loaded with microplastics.

Amid the growing ecological threat of microplastics, a team of researchers from the Hong Kong Polytechnic University developed a solution to trap microplastics using biofilms engineered with the Pseudomonas aeruginosa bacteria, which has been found to colonise microplastics in the environment. The sticky exopolymeric substances (EPS) biofilms aggregate the microplastics in a bioreactor, thus facilitating microplastic collection and recycling. The findings demonstrate the biofilms’ potential for use in wastewater treatment plants to prevent microplastics leaking into the oceans. The researchers also observed that the engineered biofilm showed potential application in curbing microplastics pollution in seawater samples collected from sewage pipes.
Along the same vein, experts from the Canadian Institut National de la Recherche Scientifique (INRS) have developed an electrolytic treatment of wastewater that degrades microplastics at source. The research is published in the Environmental Pollution journal.
Led by Professor Patrick Drogui, the study, which tested sample water that is artificially contaminated with PS using electrolytic oxidation, found that this process can have a degradation efficiency of 89%. Importantly, the technique does not require chemicals or involve physical isolation of contaminants.
The electrodes generate hydroxyl radicals that attack microplastics, they said, adding that the technique enables degrading the particles in CO2 and water molecules. The next step for the team is to test the process on real water, which according to them contains other materials such as carbons and phosphates that can impede oxidation and affect the degradation process.
Breakthrough processes to improve plastics biodegradabilty
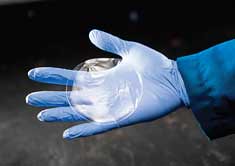
Compostable and biodegradable plastics have been touted as plausible solutions to plastic waste pollution. But these eco-friendly materials differ in their degradation processes. Some biodegrade slowly, while others break down into plastic fragments, or not disintegrate at all. There are also plastics under these categories that require industrial composting. According to experts, biodegradable plastics can still be improved so that they will not generate microplastics.
Scientists at the University of California (UC), Berkeley and the University of Massachusetts Amherst, in a project funded by the Department of Defence’s Army Research Office, developed an enzyme-activated compostable plastic that can break down by up to 98%, with just heat and water and within a few weeks. The novel process involves embedding polyester-eating enzymes in the plastic during its production.
Ting Xu, UC Berkeley Professor of Materials Science and Engineering and senior author of the study published in Nature journal, explains that these enzymes are protected by a simple polymer wrapping consisting of molecules called random heteropolymers or RHPs that prevent the enzyme from untangling and becoming useless.
When exposed to heat and water, the enzyme discards its polymer shroud and starts gnawing the plastic polymer, reducing it to its building blocks. In the case of renewable material-derived polylactic acid (PLA), it is reduced to lactic acid, which can feed the soil microbes in compost. The polymer wrapping also degrades. The process, thus, eliminates microplastics. The new technology should theoretically be applicable to other types of polyester plastics, potentially allowing the creation of compostable plastic containers, Xu said. The team is developing RHP-wrapped enzymes that can degrade other types of polyester plastic. Xu is also modifying the RHPs so that the degradation can be programmed to stop at a specified point and not completely destroy the material, a useful technique for remelting plastic to recycle it into new plastic.
Additionally, programmed degradation could be the key to recycling many objects. For example, computer circuits or electronics held together with biodegradable glue can be dissolved so that the devices fall apart and all the pieces can be reused or repurposed.
Plastic components with longer lifespan to curb microplastics
Almost 23% of global energy consumption can be attributed to friction losses. Components with reduced friction therefore represent an important contribut ion to conserving resources and achieving climate protection targets. In the case of plastics, reduced friction can also reduce microplastics in the environment.
With the development of microcapsules filled with liquid lubricants for plastics, the Potsdam Fraunhofer Institute for Applied Polymer Research IAP and the Plastics Center SKZ in Würzburg are supporting these goals. Their self-lubricating plastics achieve up to 85% less wear. Since March 2021, the successful research project has been continued for two years.
Whether it is sliding doors, laminate, plastic gears or other moving components – there is a variety of applications where materials are subject to friction. Plast ics manufacturer s are therefore somet imes incorporating solid lubricants into plastics to reduce component wear. However, there are only a relatively small number of solid lubricants suitable for plastics processing. In contrast, there is a much wider range of liquid lubricants, some of which are more effective. In a cooperative effort, the two research institutes have succeeded in encapsulating liquid lubricants in such a way that they can be incorporated into polymers as functional substances and later develop all the advantages of a liquid lubricant in the component.

"We managed to incorporate Fraunhofer IAP‘ s mi c rocapsules filled with liquid lubricant int o thermoplastics using a twin-screw ext ruder. The challenging task was to mix the microcapsules with thermoplast ics under high temperatures without damaging the capsules. Only when friction occurs in the final component the capsules should break and release the lubricant. This allows the component to lubricate itself automatically,” explains Moritz Grünewald, researcher in the Mater ials Development Group at SKZ. "Our friction and wear tests showed a reduction in wear of up to 85% on plastic-steel pairings. Thus, components last significantly longer and generate less microplastic."
Based on these results, the material system is being optimised further for potential applications. The development is now focusing on improved mechanical and thermal properties of the selflubricating plastics.
The additional use of reinforcing materials such as fibres is intended to make the self-lubricating plastics more mechanically stable. In the project, the researchers investigate, which type of fibre is best suited for thi s purpose and how the microcapsules can be optimally bonded to the plastic matrix. In addition, the capsules are also to be incorporated into higher-melting plastics to further widen the technical application possibilities. To this end, even more stable capsule wall materials are being developed in close cooperation between the project partners.
The researcher s say that numerous inqui r ies f rom the indust ry highl ight the need for novel plastics with optimised friction and wear properties. Microencapsulation technology has major advantages for companies in this regard: the wide range of liquid and advanced lubricants can now be used as internal lubricants with on-demand release properties.
The project is accompanied by a committee that includes companies from all sectors of the plastics industry, lubricant manufacturers and microencapsulator s and is also open to further partners.
(PRA)
Subscribe to Get the Latest Updates from PRA Please click here
©2021 Plastics and Rubber Asia. All rights reserved.
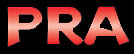
©2020 Plastics and Rubber Asia. All rights reserved.
Home Terms & Conditions Privacy Policy Webmail Site Map About Us