Building Sector: Building up an ecological balancing act
New circular innovations are turning waste materials into new concrete material, roofing and other construction products, adds Angelica Buan in this article.
On the road to sustainability
The building and construction industry is a major economic growth engine, and also among the largest consumers of energy, accounting for over a third of global energy consumption. It is also material-intensive, accounting for about half of the total use of raw materials. Plus, it accounts for almost 40% of total direct and indirect carbon emissions, according to the International Energy Agency (IEA).
The growing global population, which a United Nations data predicts to breach 9.7 billion by 2050, is whetting the industry’s expansion.
Thus, reducing the environmental footprint of the industry is imperative – the sooner, the better.
With industries adopting the circular system whereby resources are retained and reused, the building and construction industry is also turning its attention to sustainability. Companies are beefing up their portfolios with products that are recycled or upcycled; and contain recycled, renewable, or sustainably-sourced materials.
Building blocks to sustainability
Green concrete, made with recycled or waste materials, is gaining traction among builders and developers that follow sustainability trends and global environmental policies. The global green concrete market is projected to post a CAGR of 9.45% over seven years from 2020, according to a report by Market Research Future. It is driven by the demand for economically viable solutions and sustainable building materials in the construction sector and a compliance with green building laws.
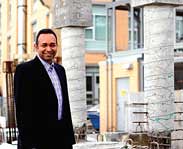
Despite the perceived increased use of green concrete, is it on par with conventional concrete in terms of strength and durability?
This burning question is addressed in a study carried out by researchers at the University of British Columbia (UBC) Okanagan’s School of Engineering, using recycled and conventional concrete in a building foundation and municipal sidewalk – two common applications for concrete. During the five-year study period, UBC researchers tested the compressive strength and durability of recycled concrete with the conventional form. It was found that the recycled concrete had a higher rate of compressive strength after 28 days of curing while maintaining a greater or equal strength.
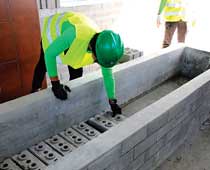
Crushed concrete replaced natural aggregate in the study’s recycled material. Recycled concrete is not widely recognised by international standards owing to its high porosity, a lack of reliably consistent sources, and a lack of field studies. But as a result of this study, funded by the Natural Sciences and Engineering Research Council of Canada (NSERC), OK Builders Supplies and KonKast Products, researchers said recycled concrete could be a 100% substitute for non-structural applications, and could start being a substitute for structural applications with improvements in the composition of recycled concrete.
Recycled concrete has found real world applications. In the Philippines, Manila-based real estate firm Ayala Land Inc (ALI) has converted plastic wastes into green construction products. As part of its circular waste management initiative, the company has recycled an estimated 28 tonnes of plastic waste from about 2.8 million plastic water bottles collected from its properties and communities and produced bricks to be used for pathways, sidewalks and fences for its estate developments.
ALI collaborated with Bulacan-based sustainable solutions provider Green Antz Builders, which upcycled the dry plastic waste into sustainable concrete or eco-bricks using its proprietary technology.
Green Antz’s system mixes the shredded plastic, usually non-recyclable laminates, with cement and additives to form bricks, pavers and casts. The ecobricks are said to be five times stronger than regular hollow blocks. Green Antz has collaborated with other major Philippine companies to provide eco-bricks for their construction requirements, which has led to converting thousands of waste plastic into eco-bricks.
Over in Australia, the Royal Melbourne Institute of Technology (RMIT) has conducted a research on converting flexible plastic into concrete. Partnering with Victoria-based recycling organisations, Replas, RED Group and SR Engineering, it developed a concrete material made from lightweight recycled plastic.
Melbourne-based consulting and recycling organisation RED Group is responsible for Australia’s REDcycle initiative to recover postconsumer soft plastic. According to RMIT, Australians turn over 1.3 million pieces/day of soft flexible plastic, like cling wraps and plastic bags that are difficult plastics to recycle, to REDCycle recycling
RMIT then worked with the industry to include Polyrok, a plastic aggregate made from soft plastics developed by Replas, in the concreting of the car park of a Coles’s supermarket and a footpath. RMIT teamed up with Replas, RED Group and SR Engineering to develop the mix methodology and material characteristics for the Polyrok material.

With the partnership, the group has diverted around 1 billion pieces of flexible plastic waste from landfills. There is the potential for 105,000 tonnes/year of soft flexible plastics to be converted into the dense plastic aggregate in a local factory in Melbourne, RMIT said, adding that it is looking to explore 3D printing to produce sustainable concrete structures in the future.
Where plastics meet the road
Recycled plastic wastes are viable alternative materials for road construction because of the cost saving advantages. Utilising recycled materials in construction applications, such as in asphalt, can conserve natural resources as well as create opportunities for innovative environmental friendly materials and technologies.
The asphalt industry, being a leader in recycling and sustainability, has been looking for ways to use these waste materials in roadways. As with any experimental material in roads, the proper testing needs to be done to ensure the process would result in long-lasting and high-performing roadways.
A project by US-headquartered Plastics Industry Association (PLASTICS) and the National Centre for Asphalt Technology (NCAT) affirm that recycled materials using waste plastics are viable in asphalt formulation. Its New End Market Opportunities (NEMO) for Film Asphalt Project focused on recycled polyethylene (rPE) film recovered from retail locations asserts that can provide the same benefits as that of traditional polymer-modified asphalt formulations.
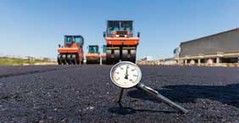
Extensive testing shows that the benefits from rPE asphalt formulation include improved performance, decreased cost, and increased lifespan of asphalt.
Research shows that even in small amounts, rPE could improve properties such as stiffness and resistance, without cracking due to low temperature or fatigue. With the right blend of rPE and a reactive co-polymer additive, new asphalt formulations match the effectiveness of traditional styrene-butadienestyrene block copolymer (SBS) at lower cost.
PLASTICS has been advancing research on the potential of consumer recycled PE films as polymer additives in asphalt binder. Together with NCAT, the team has conducted a battery of tests using federal and state transportation standards, a necessary step before large-scale implementation across the US.
Based on successful lab-scale research on the latest rPE formula, PLASTICS says it is now working with several companies to use it on privately-funded roadways and parking lots.
In the same token, a partnership between American chemical company Dow and China’s dairy brand Shiny Meadow is converting used milk bottles and recycled plastic into what is claimed as China’s firstever plastic road.
The “Milk Bottle Road” collaboration was launched in April this year at the East China Universityof Science and Technology (ECUST) Xuhui Campus. The project utilised Dow’s Elvaloy RET asphalt modification technology, whereby more than 6,000 used milk bottles and other plastic wastes were used to pave the polymer-modified asphalt (PMA) road. Accordingly, PMA roads demonstrate excellent performance and durability as compared to conventional neat asphalt.

Although milk bottles are easily recycled, recyclers avoid taking in such waste due to the high rate of contamination caused by leftover milk residue. To help dairy brands like Shiny Meadow to repurpose plastic milk bottles, Dow presented a solution where such hard-to-recycle plastic is collected and used. By doing so, plastic waste is kept out of the environment, and the reduction in the use of bitumen as well as the potential service life extension of the roads will in turn reduce greenhouse gas emissions and energy consumption, adds Dow.
Dow has already embarked on a few recycled plastic projects, previously tapped for recycled plastic roads in Depok City, Indonesia, in 2017; and a collaboration with India’s KK Plastic Waste Management, Rudra Environmental Solutions and two local governments to implement plastic-roads in the cities of Pune and Bangalore. A recent project is a collaboration with Thailand’s Siam Cement Group to improve asphalt roads with plastic in Thailand.
Raising the roof with recycled materials
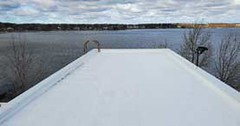
Not surprisingly, the advantages of plastics, such as durability, tensile strength, cost-effectiveness and flexibility, even in recycled form, are still inherent when applied to construction. So, recycled plastics as roof? Why not!
Kraft Heinz, a US-based multinational food company, has shown the viability of recycled plastic roofing with its new project.
The company’s pilot project demonstrates the use of roof board made from recycled flexible packaging, which Kraft Heinz uses across its product portfolio.
The test was made possible by the company’s participation in Materials Recovery For the Future (MRFF), a non-profit organisation that lays the groundwork for the future of recycling flexible plastic packaging. The project installed roofing material made from post-consumer flexible plastic in two Kraft Heinz manufacturing plants in Beaver Dam, Wisconsin, and in Holland, Michigan. The recycled roofing materials, which were installed in late 2020, comprised 4’ X 8’ boards. Each board has 94% postconsumer recycled plastic and fibre.
According to Kraft Heinz, the pilot project will be monitored and compared with standard building materials. It added that it will consider standardising use of this recycled material in the future, if the recycled materials will show to perform as well or better than standard building materials.
Similarly, GAF, North America’s largest roofing and waterproofing manufacturer, has unveiled a new patented shingle recycling process that has successfully produced the industry’s first asphalt roofing shingles containing recycled material from post-consumer and post-manufacture waste shingles.
GAF said that the new shingle recycling process reduces the amount of raw materials required to make new shingles without compromising product quality or performance. During its successful tests, over 90% of the waste shingle material, by weight, was recovered and to be reused in the manufacture of new shingles. GAF also demonstrated its ability to manufacture new shingles containing up to 15% recycled material that were UL-certified for their safety and effectiveness. The new shingle recycling process is covered by three US patents.

GAF is investing more than US$100 million to bring the recycling process to commercial scale, including the development of a pilot operation in 2021 that will enable additional R&D on the process.
According to GAF, the technology ushers in a future where homeowners are able to replace roofing with high-quality and affordable shingles made with recycled asphalt.
Further down the line, new technologies are being developed to increase the recovery and use of waste plastics and other scrap materials for sustainable applications in construction.
(PRA)
Subscribe to Get the Latest Updates from PRA Please click here
©2021 Plastics and Rubber Asia. All rights reserved.
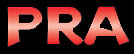
©2020 Plastics and Rubber Asia. All rights reserved.
Home Terms & Conditions Privacy Policy Webmail Site Map About Us