PRA Chinese
Rubber Journal Asia Injection Moulding Asia Energy, Oil & Gas Asia
VISIT OUR OTHER SITES:
PRA Chinese
Rubber Journal Asia
Injection Moulding Asia
Energy, Oil & Gas Asia
Kraiburg on route to making TPEs from sustainable materials
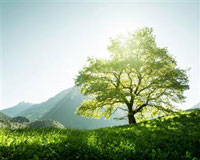
By developing customer-specific and application-specific compounds using renewable raw materials, German TPE maker Kraiburg says it is aiming to meet the growing demand for environmentally friendly and sustainable thermoplastic elastomers and is playing a pioneering role in the innovative developments involved. In close contact with its customers and with a reliable network of raw materials suppliers, the company is benefiting from its core competence in custom-engineered TPEs based on both existing and new, innovative formulations.
Climate change, finite oil resources and customers who are increasingly environmentally aware are leading more and more materials manufacturers and users to turn to “renewable” and “bio-based” solutions. However, “bio” is a broad term that is by no means synonymous with “sustainable” in the sense of a strategy for saving resources and protecting the environment. Because even renewable raw materials also have carbon footprints, as well as water footprints, that can have an impact on the environmental balance, depending on their provenance and the way they are grown. Factors that play a decisive role here include irrigation, fertilisers, transport energy and energy consumed for reprocessing.
“Part of the challenge involves taking into account the environmental balance of the materials’ whole life cycles, including their impact on ecosystems and people’s health,” emphasises CEO Franz Hinterecker of Kraiburg. “It has also become apparent that what our customers expect from the properties of ‘bio-materials’ varies widely depending on the application – while at the same time we have to meet strict criteria regarding the materials’ conformity and performance.”
The German firm has therefore opted for a basically customer-specific approach.
In its Code of Conduct, Kraiburg has committed itself to sustainable business operations and to protecting the soil, water, air and biological diversity. Environmentally harmful impacts are to be prevented by appropriate environmental protection measures, and resources are to be conserved. Based on this principles, its modular system makes it possible to develop customer-specific materials with different proportions of renewable raw materials. Typical performance characteristics that are also relevant here include mechanical properties such as tensile strength and elongation, as well as processability, heat resistance and adhesion to ABS/PC or PP and PE, for example. The requirements are determined in close collaboration with each customer and translated into a sustainable and cost-effective solution by our developers.
In classical approaches, it is technically possible to produce bio-based materials with very high proportions of renewable raw materials. However, materials of this kind usually suffer from very high raw materials costs, while providing only very limited mechanical properties. But the modular system has now enabled Kraiburg to resolve this contradiction almost completely by following a new approach beside the classical one.
The initial pilot projects based on the classical approach are showing a trend towards bio-based, certifiable proportions of 20% and more.
Their potential use extends to all TPE applications in the consumer, industry and automotive markets. Examples range from toothbrushes and hypoallergenic elastic watch straps to fender gaskets.
“The approach we’re taking is being well received particularly by customers who are looking for sustainable solutions but don’t want to do without cost-effectiveness and performance,” Hinterecker adds. “Our core competencies – a strong customer focus, global presence and trendsetting innovations – mean we are in a good position to meet these challenges.”
(PRA)Subscribe to Get the Latest Updates from PRA Please click here
Copyright (c) 2018 www.plasticsandrubberasia.com. All rights reserved.