Green tie-ups: Consortium set up for supply chain of CO2-based polyester fibre; Plast Nordic/Norner to advance PET recycling at scale in Nordic region
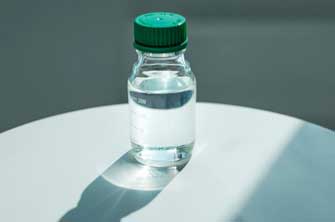
A consortium of seven companies across five countries has jointly established a supply chain for more sustainable polyester fibre. Instead of fossil materials, renewable and bio-based materials as well as carbon capture and utilisation (CCU) will be used in the manufacturing of polyester fibres for The North Face brand in Japan. The consortium parties are Goldwin, in the role of project owner, Mitsubishi Corporation, Chiyoda Corporation (all three from Japan), SK geo centric (South Korea), Indorama Ventures (Thailand), India Glycols (India) and Neste.
Neste will provide renewable Neste RE as one of the required ingredients for polyester production. The polyester fibre produced in the project is planned to be used by Goldwin for a part of The North Face products, including sports uniforms, in July 2024. After that, the launch of further Goldwin products and brands will be considered.
The seven companies apply a mass balancing approach to ensure credible traceability of material streams throughout the supply chain and will jointly continue to proactively promote the defossilisation of materials.
Regarding the production of para-xylene derived from CO2 as a raw material, the University of Toyama, HighChem Company Limited, Nippon Steel Engineering Co. Ltd., Nippon Steel Corporation, Chiyoda Corporation and Mitsubishi Corporation were granted a NEDO project (New Energy and Industrial Technology Development Organisation) status in 2020. They are conducting joint R&D. This project is to supply CO2 -derived para-xylene in the course of a trial. It has been produced during the operation process of a pilot plant installed in Chiyoda Corporation's Koyasu Research Park since March 2022.
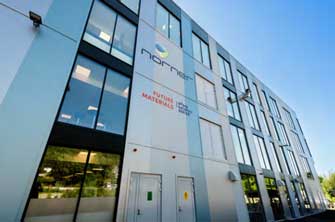
Meanwhile elsewhere, Plast Nordic has entered into a collaboration with Norner, with the intention to use alkaline hydrolysis technology to recycle PET waste back into raw materials.
Based in Porsgrunn, Norway, Norner operates advanced laboratories, polymerisation units, and process pilot plants at an industrial scale. Norner is owned by SCG Chemicals in Thailand and serves over 700 customers in more than 60 countries.
Plast Nordic will employ a technology known as alkaline hydrolysis. This conventional process is enhanced with patented microwave technology from Switzerland, providing the process with characteristics such as resilience to waste impurities - up to 30% impurities without affecting quality; chemical-free, utilising microwaves instead; speed - the process takes under 10 minutes, setting it apart from others-24/7 operation as the reactor runs continuously, not in batches and its ability to handle both plastic and polyester textiles.
Since 2019, Plast Nordic has been involved in industrial preparations for chemical recycling facilities in the Nordics. The end product for Plast Nordic will be chemically recycled PET resin for the plastic and textile industries, equivalent in quality to newly produced oil-based PET.
Currently, there is a demonstration plant of this type in Italy, and the first full-scale factory is scheduled to open in Spain in 2027.
Plast Nordic is currently in the process of qualifying locations for its first factory. The company has closely examined several relevant sites in both Norway and Denmark and hopes to open its first factory in the Nordic region by 2028.
"Plast Nordic has the potential to significantly increase sustainability in the plastics and textile industry. However, the company needs more specialised expertise. Norner has the capacity to contribute with business strategy, polymer science, and production technical assessments, which in turn increases the realisation ability of this large and important industrial project,” said Kjetil Larsen, CEO.
The framework for collaboration is now established through a Memorandum of Understanding (MOU), outlining a strategy for how the companies collectively contribute to Plast Nordic's strategic and commercial objectives.
In the Nordic region, there are over 400,000 tons of PET waste. With a completely new industrial solution, approximately 97% of this can be chemically recycled back into the same raw materials it was made from. Current exports of PET waste represent both significant energy loss and irrational management of substantial value.
Plast Nordic says it aims to keep this material within the circular economy, thereby creating new jobs, reducing transportation, and increasing access to valuable recycled materials. Several Nordic brands have already expressed significant interest in these products.
Chemical recycling of this kind represents the highest quality circularity, as it recovers the raw material value from the waste without any loss of quality, it claims.
(PRA)SUBSCRIBE to Get the Latest Updates from PRA Click Here»