Recycling tie-ups: Mitsubishi Chemical/Agilyx show success in PMMA recycling; TotalEnergies/Plastic Omnium to focus on recycled PP for auto sector

Mitsubishi Chemical Methacrylates (MCM) and chemical recycling firm Agilyx Corporation, a wholly owned subsidiary of Norway’s Agilyx AS, have been successful in the full-scale production trial for polymethyl methacrylate (PMMA; commonly called acrylic) depolymerisation at Agilyx’s facility in Tigard, Oregon.
The full-scale trial, conducted in 2021, returned results consistent with the successful results of a laboratory-scale trial conducted in 2020. A mixed feedstock included both cast and extruded PMMA sheet, and the effects of different temperature settings were analysed to find the optimal conditions for PMMA pyrolysis.
Following the successful plant trial, experts from MCM and Agilyx are to focus on building an action plan that sets out the required next steps.
“The results at full production scale are very encouraging,” said David Smith, circular economy programme lead, Mitsubishi Chemical Methacrylates. “The teams at both MCM and Agilyx worked very well together, and all parties are excited at the prospect of building a new PMMA depolymerisation plant using Agilyx technology.”
The crude MMA produced during the plant trial is currently being distilled at MCM’s pilot plant in Wilton, UK, and will be used both for internal product development and to validate the purification solution that will be used in this process.
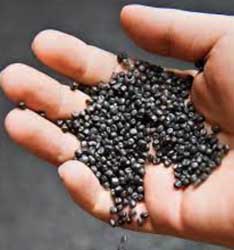
Meanwhile in other news, TotalEnergies and Plastic Omnium have signed a strategic partnership that will see them join forces to design and develop new plastic materials, made from recycled PP, which meet the demanding aesthetic and safety standards that apply to the automotive industry.
TotalEnergies and Plastic Omnium will pool their innovation and engineering skills to design new types of recycled materials that offer enhanced performance and are better for the environment while providing deliverable responses to the challenges raised by end-of-life plastics. These new materials, containing 20% to 100% recycled materials sourced from industrial and domestic waste streams, have a CO2 impact as much as six times lower than using virgin materials.
The use of plastics in automotive bodywork plays a key role in cutting the automotive industry’s carbon emissions. They make it easier to improve aerodynamic performance and reduce the overall weight of vehicles, helping in turn to cut the amount of fuel used by internal combustion vehicles and increase the autonomy of electric vehicles.
Valérie Goff, Senior Vice President, Polymers at TotalEnergies says: “This partnership with Plastic Omnium is a great example of collaboration and innovation to develop ever-higher and environmentally friendly recycled plastic materials that help our OEM and vehicle manufacturer customers to reduce their carbon footprints. This project will also contribute to addressing the challenge of the circular economy and to our ambition of producing 30% recycled and renewable polymers by 2030.”
Stéphane Noël, President and CEO of Plastic Omnium Intelligent Exterior Systems, adds: “Recycling plastic materials is a challenge to us as manufacturers, and a vital issue for our planet. This exciting partnership paves the way to providing responses that are better integrated and more environmentally friendly, reflecting our customers’ and suppliers’ carbon neutrality goals. This is absolutely central to a strategic partnership that seeks to support the far-reaching transformation the industry is currently undergoing.”
(PRA)
Subscribe to Get the Latest Updates from PRA Please click here
©2022 Plastics and Rubber Asia. All rights reserved.
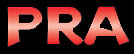
©2022 Plastics and Rubber Asia. All rights reserved.
Home Terms & Conditions Privacy Policy Webmail Site Map About Us