PRA Chinese
Rubber Journal Asia Injection Moulding Asia Energy, Oil & Gas Asia
VISIT OUR OTHER SITES:
PRA Chinese
Rubber Journal Asia
Injection Moulding Asia
Energy, Oil & Gas Asia
Can bioplastics fix the world’s waste mess?
Also, download this story from the electronic issue here
The environmental impact of non-degradable plastic waste has made the world rethink of how we use and produce environmentally-friendly plastics, says Angelica Buan in this report.
China to stop taking plastic waste from developed countries
The making of an environmental disaster is on the cards now that China has decided to stop the import of some 24 types of waste materials including plastics. With the ban coming in effect in March, more than 6 billion tonnes of global plastic waste will not be recycled in China.
China, which has topped the rank of global plastic polluters, can hardly be blamed. It said it has to fix its own environmental issues.
So what will happen since Europe and the US are two major exporters of waste to China?
In a bid to nearly halve Europe’s plastic consumption by end of 2019 and by a further 80% by end 2025, European Union has stepped up its plastic bag taxation drive. The US, on the other hand, which ships nearly 1.5 million tonnes of plastic waste to China to be recycled, will have to rely on its capabilities to manage its waste and recycling.
As well, what seems to be hoped for is that the rest of Asia will open its doors to recycling opportunities. This is ironic because the region is also contending with plastic waste troubles in its own backyard, with the top 20 polluting rivers found to be mostly in Asia, according to Dutch Foundation Ocean Cleanup.
Asia as a bioplastics hub
Against this backdrop, the push to use bioplastics is
growing with research house Knowledge Sourcing
Intelligence
forecasting
the global
bioplastics
market with
a value of
US $43.8
billion in 2022,
against US$17 billion in 2017, growing at a CAGR of 20%. The same growth
trajectory of 20%, driven by demand for biopolymers such
as polylactic acid (PLA) and polyhydroxyalkanoates (PHA),
was also cited in the European Bioplastics’ annual market
data update recently.
The Asian region is also flexing its capabilities on producing bioplastics withLuxResearch’s 2016 report pointing at Southeast Asia as a biochemical hub, given its local access to sustainable raw materials.
Thailand has sufficient supply of sugarcane and, according to the 2017 data of USDA Gain, has produced 11.2 million tonnes of sugar to more than meet the country’s consumption and cater to exports.
It is not surprising that large-scale bioplastics factories are coming up in the country.Total Corbion, a joint venture between Dutch PLA producer Corbion and French oil and gas company Total,is completing construction of a 75 kilotonne/year-PLA plant in Rayong, with start-up scheduled this year.
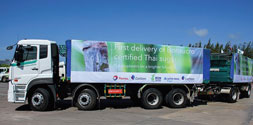
The second half of the year will also see the company’s expansion of its existing lactide plant, also in Rayong, by 25 kilotonnes/year. The PLA polymerisation plant will be producing Corbion’s Luminy portfolio of PLA resins. Total Corbion says it uses Bonsucro-certified cane sugar (a global non-profit network that sets standards to ensure sustainability) as a feedstock that is converted to lactic acid through fermentation, which in turn is used as a base for PLA bioplastics. The company sources its raw materials from Bangkok-headquartered Mitr Phol, Thailand's biggest sugar and bio-energy producer, which has two Bonsucrocertified mills.
PTT Chemical and Cargill’s joint venture NatureWorks Asia Pacific is also expanding its footprint in Thailand with a planned US$143 million bioplastic plant.
Over in Indonesia, reportedly the world’s second biggest plastic waste contributor, bioplastic alternatives, such as seaweed farming, are being pursued. Seaweed is not only sustainable but found to produce durable yet degradable materials. A local company, Evoware, is tapping on Indonesia’s abundant seaweed supply by using it for its patented seaweed-based packaging and also uplifting living standards of seaweed farmers, many of whom are from the poorest provinces in the country.
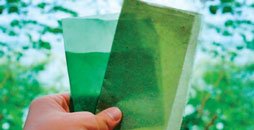
The seaweed packaging is 100% biodegradable, dissolves in warm water and has a shelf-life of up to two years. It is printable and heat-sealable and, while application potential is broad, it is suitable for small-format food sachets and wraps, as well as for non-food based items.
Malaysia’s palm oil, meanwhile, is being harnessed to produce PHA bioplastics. A 2,000 l-capacity plant, which started in 2011, was built through a partnership between SIRIM, Universiti Sains Malaysia (USM) Universiti Putra Malaysia (UPM), and the Massachusetts Institute of Technology (MIT). It is located in Shah Alam, Selangor.
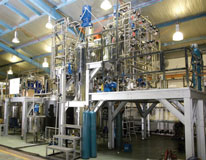
According to SIRIM, the plant employs a process that makes good use of the by-products of the palm oil industry, such as crude palm kernel oil (CPKO), palm oil mill effluent (POME), as well as solid biomass comprising empty fruit bunches (EFBs), mesocarp fibres (MFs), palm kernel shell (PKS), fronds and trunks. SIRIM says that the mills produce about 60 million tonnes of POME and 80 million dry tonnes of solid biomass, and these volumes could reach 70-110 million tonnes and 100 million dry tonnes, respectively, by 2020. In particular, POME, a waste liquid that has 100 times the oxygen-depleting potential of domestic sewage, is a major concern for the industry because of the environmental effects it has on soil and water when disposed, said SIRIM.
With the bioreactor and synthesising technologies now on hand, POME as well as CPKO can now be viable sources of PHA-based bioplastics.
Another Asian country, Vietnam, with a per capita plastic output of 41 kg/year in 2016, according to the Vietnam Plastics Association, expects that by 2020 plastic producers are likely to require about 5 million tonnes of materials for manufacturing, to satiate the growing consumption. Over that period, plastic waste will also grow exponentially. A project has been hatched so that by 2020, the use of non-biodegradable plastic bags, the biggest environmental polluter, will be reduced by more than half.
Thus, Vietnam is building its first eco-plastic plant in an industrial zone in Long An province. The US$10 million-plant, a joint venture project between Vietnam Plastic House and a Guangzhou-based biodegradable plastics firm, will have a capacity of 3,000 tonnes/year of bioplastic bags.
Reportedly, four more biodegradable plastic bag plants will be built in Vietnam and three similar plants in Cambodia, Laos and Myanmar.
The HCM City Plastic Association, which is involved in the project, explained that the eco-plastic resin is made from cellulose, tapioca and additives, which enable the plastic bag to disintegrate after two years.
Sweet success for sugarcane-based bottle and MEG
France was the first country to completely wean itself off the use of plastic plates and cutlery. Innovations to counter the proliferation of oil-based plastics include a recent biobased bottle design by French firm Lyspackaging. The sugarcane-based Vegan Bottle is 100% biodegradable, and has improved mechanical and barrier properties, according to Lyspackaging.
The eco-bottle can help reduce the number of oilbased bottles being used and discarded. Lyspackaging says 45% or 200,000 tonnes/year of plastic bottles are not recycled in France.
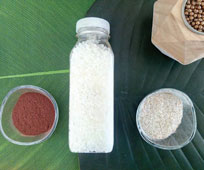
Elsewhere, Brazilian petrochemicals company Braskem and Danish firm Haldor Topsoe, specialising in catalysts and surface science, are to develop a pioneering route to producing monoethylene glycol (MEG) from sugar. MEG is a key component of PET resin. The deal also covers construction of a demonstration plant in Denmark that will start up in 2019.
The project is based on a two-step process developed at Topsoe's laboratories along with its own catalysts, and focuses on the conversion of sugar into MEG at a single industrial unit, which will reduce initial investment in the production and boost the competitiveness of the process.
The demonstration plant will conduct tests to validate the technology and confirm its technical and economic feasibility, as well as validate the technology in different raw materials, such as sucrose, dextrose and secondgeneration sugars.
Deriving bioplastics from organisms
Thinking out of the box, Arizona State University (ASU) has undertaken a study on producing fully biodegradable plastics using cyanobacteria (also called blue-green algae) that thrive in soil and water and can manufacture their own food.
Lead researcher, Taylor Weiss, explained that for the study a symbiotic partnership between two bacteria was created, each specialising a specific task. “The cyanobacteria use photosynthesis to create sugar and are engineered to constantly excrete that sugar. A second bacteria, called Halomonas boliviensis, consumes the sugar to alternately grow and produce bioplastics in cycles. Additionally, the cyanobacteria are captured in hydrogel beads made from seaweed extract that are submerged in saltwater filled with the bioplastic-producing bacteria.”
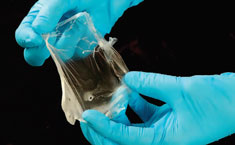
There are challenges, such as using as little of the hydrogel as possible and for as long as possible to also help keep costs down, but Weiss says this bacteria-bioplastic process is industrially viable, with the two bacteria and the hydrogel already having been industrialised.
Lowering costs, especially if targeted for industrial scale, was also a concern of a research carried out by a team of scientists from the Centre for Biological Research (CIB-CSIC) in Madr id to produce PHA bioplastics. Surmounting the challenge of extracting polymer f rom bacter ia, lead researcher Vi rgini a Martínez said an innovative extraction method had been developed. “What we did was to use the predatory bacterium B. bacteriovorus as a lytic agent to kill other bacteria, specifically the natural PHA producer, P. putida KT2440, and recover the intracellular bioproduct. We also engineered the predator so that it doesn’t degrade the bioplastic accumulated by the prey.”
With this novel system, bioplastic is thus recovered in a single step without requirement for complex equipment or toxic compounds. The findings of the study were published in Scientific Reports.
PHA bioplastic from non-GMO feedstock
Meanwhile, a company specialising in converting organic waste into bioplastics, Canada-headquartered Full Cycle Bioplastics (FCB), is manufacturing PHA bioplastic using a non-Genetically Modified Organism (GMO)-based process. It utilises organic and cellulosic waste as the feedstock, a novel option to commercially available PHA that is currently made from crop-based feedstock, such as food-grade sugar or seed oil. The FCB process uses food waste, agricultural by-products, cardboard and waste paper as raw materials. Even endof- life PHA products can be utilised as feedstock for the production of virgin PHA.
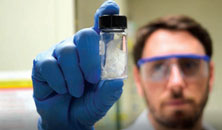
FCB’s proces s involves organic waste being broken down and becoming feedstock for PHA. Once the feedstock is perfectly adjusted, it is dosed in an environmentally conditioned tank of naturally occurring bacteria, where it is consumed and converted into PHA, then dried and processed into a finished resin product, ready for compounding.
FCB emphasised that i ts process significantly lowers production costs and eliminates the need for expensive laboratory-grade sterility or containment. Moreover, FCB said that licensing the technology can enable companies with large waste streams to produce PHA “to generate revenue and at the same time, curb disposal costs by creating the highest and best value from waste”.
Thus, the looming issue on waste plastics has the upside of encouraging further development of bioplastics as an attainable and sustainable solution to controlling waste plastics.
(PRA)Copyright (c) 2017 www.plasticsandrubberasia.com. All rights reserved.