Chinaplas 2025: Auto industry drives demand for sustainable plastics
Automotive industry pushes for high performance and sustainability
The global automotive industry is undergoing constant transformation. Automotive plastics, as a key component material, are evolving toward high performance, eco-friendliness, intelligence, and electrification. Chinaplas 2025, the world's leading plastics and rubber trade fair, will take place at the Shenzhen World Exhibition & Convention Centre (Bao’an), PR China, from April 15 to 18, 2025.
The exhibition will bring together over 4,000 international exhibitors under one roof, showcasing the latest technology and process applications, including intelligent interior and exterior components, low-carbon environmental solutions, and enhanced safety and durability for the automotive industry—contributing to its sustainable development.
Online pre-registration for Chinaplas 2025 is now open. Admission tickets are available on a first-come, first-served basis.
Plastics technologies driving next evolution of NEVs
China's Ministry of Industry and Information Technology announced the mandatory national standard titled “Energy Consumption Limits for Electric Vehicles - Part 1: Passenger Cars” (Draft for Comments) on August 21, 2024. This standard establishes electric consumption limits for new energy vehicles (NEVs) as a mandatory requirement for the first time. The energy consumption of NEVs is closely linked to vehicle lightweighting, and a key advantage of high-performance plastics is their potential to replace heavier materials.
Meanwhile, autonomous driving technology is emerging as the “brain” of NEVs. The unique properties of high-performance plastics can meet the stringent requirements of related applications. Consequently, the use of automotive plastics in vehicle manufacturing is steadily increasing, and their applications are becoming more diverse in the automotive industry.
To refine the management mechanisms governing the energy consumption of NEVs
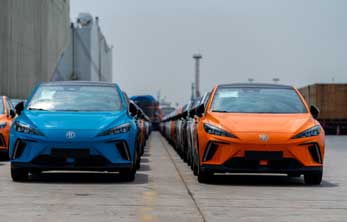
The calling for comments of the mandatory nation standard indicates the government's intention to enhance the energy consumption thresholds for vehicle models and to refine the management mechanisms governing the energy consumption of NEVs. These measures aim to promote the healthy development of the industry and encourage technological progress.
For models with fewer than three rows of seats and without four-wheel drive, energy consumption limits range from 10.1 kWh to 19.1 kWh per 100 km. Specifically, models with a curb weight between 1.09 tonnes and 2.71 tonnes must maintain their electric consumption below 13.92 kWh per 100 km. However, industry statistics indicate that as of August this year, only about 60% of these models meet the standard. This highlights the urgent need for effective means to reduce electric consumption.
The national standard requirement clearly indicates that curb weight will be a key assessment criterion. The high curb weight of NEVs is closely linked to their powertrains. For instance, many battery packs from various brands weigh over 500 kg, with some even exceeding 700 kg.
Currently, this mandatory national standard is in the consultation stage. Based on industry practices, it may take about two years before the official release. Therefore, this is the ideal window for automakers to refine their lightweight technology strategies.
Automotive plastics facilitates safe and lightweight battery packs
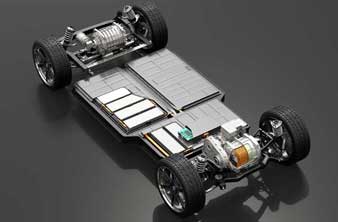
The traditional fuel vehicle powertrain (engine and transmission) operates in a high-heat, high-wear environment, resulting in limited use of plastic parts. In contrast, the new energy power system, particularly the battery pack management system and other components, offers more favorable working conditions, making it easier to incorporate automotive plastics.
Need for flame retardant - Automotive plastics play a crucial role in the thermal management of battery packs. Thermoplastics with excellent flame-retardant property can mitigate the risk of overheating in high-temperature and pressurised environments. Notably, polypropylene compounds (PPc) and long glass fibre (LGF) reinforced PP stand out.
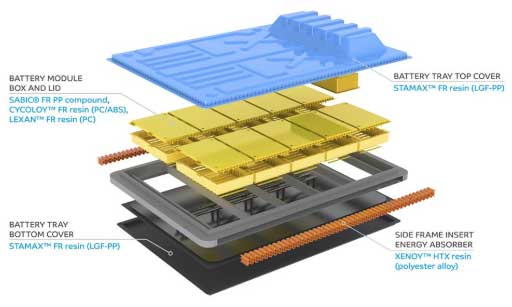
Leveraging the strengths of thermoplastics, SABIC has developed an innovative battery pack concept that integrates individual batteries into pouch cells. These cells are placed within a thin-walled housing molded with 30% glass fibre filled, flame-retardant PPc.
LG Chem and LX Hausys have also collaboratively created a special flame-retardant continuous fibre thermoplastic (CFT) designed to delay battery thermal runaway.
Need for dust and water resistance – Power battery packs require stringent dustproof and waterproof ratings, with the industry standard being IP67. Some automakers, such as Geely, NETA, and Arcfox, even claim capabilities of reaching IP68.
The key to enhancing the IP performance of battery packs lies in the sealing and securing of components around electrical connectors. These connectors, critical for maintaining the interface between the interior and exterior of the battery pack, must endure mechanical stress and environmental fluctuation.
Utilising high-strength, wear-resistant materials like polyamide (PA) or polycarbonate (PC) can ensure the stability and sealing of connections, preventing moisture, dust, and other impurities from entering the inner part, thereby guaranteeing the reliable operation of the electrical system.
In addition, the significant gas generated by the battery pack after thermal runaway must be discharged promptly to prevent potential explosion. The support structure for safety devices, such as explosion-proof valves, is often made of specially designed plastic materials that can react quickly in emergencies. This ensures effective internal pressure release, further enhancing the safety of the battery pack.
Replacing steel with plastics in structural components of battery packs – The structural components of battery pack are vital parts of the electric vehicle energy system, significantly influencing the vehicle's overall performance, safety, and driving range.
Traditionally, high-strength steel has been the material of choice for the stamping forming structure of battery packs, owing to its excellent mechanical strength and impact resistance, which helps maintain structural integrity under complex working conditions.
In recent years, there has been a growing trend toward the use of automotive plastics in battery pack design, particularly in module housings and pack sealing covers. This shift aims to enhance lightweighting while still ensuring performance and safety.
Plastic materials such as PC, PA (particularly reinforced), and polyurethane (PU) not only possess densities much lower than steel, but also achieve comparable or even superior mechanical property and environmental aging resistance under specific formulations and processes.
For instance, the LGF reinforced flame-retardant PA material newly introduced by Shanghai PRET Composites Co., Ltd. is used to replace steel in structural components of battery packs. The material reduces component weight by 40% and lowers manufacturing costs by 15%.
Structural components of battery packs face challenges from mechanical vibration, high temperatures, high humidity, ultraviolet radiation, and chemical corrosion due to their harsh working environment. This imposes stringent performance requirements on materials.
To satisfy these requirements, the industry has made substantial advancements through ongoing exploration and innovation. A notable example is the successful application of PU solutions for battery pack top covers.
In a series of rigorous standardised tests, including assessments of mechanical properties, high-temperature and high-humidity aging, xenon lamp aging, acid and alkali resistance, high-temperature resistance, and insulation properties, PU materials have proven their viability and superiority as structural materials for battery packs.
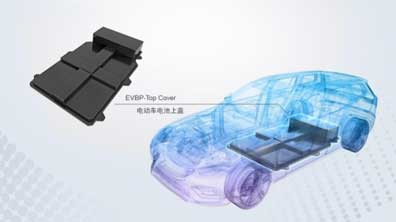
The Baydur HP-RTM (High-Pressure Resin Transfer Moulding) top cover for battery packs developed by Covestro is a key application of PU in NEVs. It is flame-retardant, lightweight and can be as thin as 0.8 mm.
Autonomous driving technology becomes new productive force – The “Opinions of the General Office of the CPC Central Committee and the General Office of the State Council on Accelerating the Construction of a Unified and Open Transportation Market”, was released in December 2024 to emphasise the continuation of pilot applications, including autonomous driving, to promote the green and intelligent transformation of transportation.
Over 50 cities in China have implemented autonomous driving demonstration policies, with automakers highlighting autonomous driving features as key selling point for NEVs.
Autonomous driving technology is emerging as a new productive force supporting the development of NEVs. It not only fosters new business models, such as shared autonomous taxi services, but also drives innovation in related technologies.
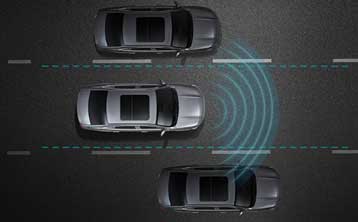
The Advanced Driver Assistance System (ADAS) employs sensors to detect and collect data, integrating it with navigation information for comprehensive analysis. Among its functions, the Navigate on Autopilot (NOA) stands out.
NOA is a technology that combines assisted driving with navigation capabilities. When a vehicle is on a highway, NOA enables it to automatically change lanes, enter and exit ramps, adjust speed, as well as manage lights based on the onboard navigation route.
High potential of plastics in autonomous driving applications – ADAS has specific and unique material requirements, and plastics offer significant potential for related applications. For instance, millimeter-wave radar delivers reliable and high-resolution information for long-range target, while the radar fairing protects the internal high-frequency antenna from weather and environmental damage. The materials used for the fairing must possess high strength and ensure that penetrating radio waves remain unaffected.
High-performance engineering plastics are not only easy to process but also exhibit excellent heat and chemical resistance. Additionally, certain plastics have a lower dielectric constant (Dk), enabling the radar's emitted radio waves to penetrate effectively, thus meeting the material requirements for millimeter-wave radar fairings.
As the ADAS market continues to expand, material suppliers are developing cutting-edge solutions. For instance, Envalior has recently launched a laser-weldable thermoplastic product portfolio for automotive radar, which includes polybutylene terephthalate (PBT), polyphenylene sulfide (PPS), and PBT + PC grades.
Among these, the PPS grade has a low Dk, which ensures high radar resolution and minimal signal loss. It also boasts heat resistance up to 210°C, excellent hydrolysis and chemical resistance, contributing to extended component life and improved system reliability. The PBT + PC grade, specifically designed for radar casings, combines high strength, exceptional hardness, and excellent heat and chemical resistance. Additionally, it features a wide injection molding process window and outstanding deformation resistance.
SABIC has introduced two new modified materials with a high dissipation factor (Df), enabling efficient noise absorption. This improvement enhances the signal-to-noise ratio of millimeter-wave absorbing devices, leading to increased sensor accuracy and transmission range. The ultra-high flow and minimal warpage properties offer greater design flexibility.
A promising future
Advances in materials science and innovations in manufacturing process show a promising future for the application of automotive plastics in the power systems of NEVs. The choice of materials for battery pack structural components will become increasingly diversified. Striking a balance between lightweight design and high performance will emerge as a key focus for the industry moving forward. Furthermore, automotive plastics can enhance the efficiency and safety of autonomous driving, facilitating the development of intelligent vehicles and transforming the transportation landscape.
Source: Song Yuan, Lecturer, Shanghai Donghai Vocational & Technical College; Adsale Plastics Network (www.AdsaleCPRJ.com)
Japanese companies increase demand for functional and eco-friendly materials
Japan's plastics industry is focusing on environmental initiatives to drive business development. While efforts are being made to promote energy-saving measures in production processes, recycling, and the development of bioplastics, global demand is soaring to unprecedented levels. Manufacturers are finding it increasingly difficult to cope with the current situation, placing their survival at risk.
Declining production and severe competition
In fact, Japan's plastic production is experiencing a significant decline. According to a summary by the Japan Plastics Industry Federation, the country’s plastic production in 2023 was 8.79 million tonnes, a nearly 20% decrease compared to a decade ago. Except for an 18% increase in plastics used for transportation equipment, primarily in the automotive sector, all other categories showed a downward trend. The decline was particularly notable in sheets and pipes, which dropped by over 30%, while films, construction materials, household goods, and miscellaneous items decreased by more than 10%.
In China, the production of all types of plastics is growing rapidly, with aggressive export strategies targeting overseas markets. As a result, Japan's plastics industry is at a disadvantage in terms of scale and cost competitiveness, gradually losing its presence in the mass consumer goods market. Moreover, discussions are underway in Japan regarding the restructuring of ethylene production facilities, which is expected to further reduce the output of all chemical products. To navigate these challenges, Japanese manufacturers need to focus on enhancing functionality and adopting eco-friendly materials.
Increasing demand for recycled plastics and eco-friendly materials
The demand for eco-friendly materials among plastics users is rising steadily. To enhance consumer appeal, there has long been a trend of using recycled plastics in certain components of home appliances and office automation (OA) equipment. Currently, as part of Corporate Social Responsibility activities by machinery manufacturers, the OA industry is heavily promoting environmental awareness. The Home Appliance Recycling Law enacted in 2001 mandates the use of eco-friendly materials in the home appliance sector.
In the automotive industry, in light of Europe’s implementation of the End-of-Life Vehicle (ELV) directive, which requires the use of recycled plastic products in vehicles, Japanese manufacturers have solidified their stance on mastering advanced utilisation technologies and establishing supply chains. To support the goal of using recycled plastics in 25% of total vehicle plastics, including 6.25% car-to-car recycled plastic, polypropylene (PP) is the initial focus. However, a comprehensive recycling system is necessary for all resin materials, including polyamides (PA), polybutylene terephthalate (PBT), and polyphenylene sulfide (PPS), as merely relying on PP and meeting the required recycling volumes remains unfeasible.
To further advance a circular economy in the automotive sector, Toyota established the non-profit organisation "Circular Core" in October 2024, initiating the development of a mechanism to recover plastics and metals from end-of-life vehicles for reuse in new cars. Additionally, in July of the same year, a group led by waste plastic recycling companies formed the "Sustainable Plastics Initiative" to expand the use of recycled plastics. Toyota also played a key role in this initiative, with its personnel serving as secretary-general. The organisation is actively building systems to collect and allocate funds for the production of recycled resin components.
“Japan's Resource Circulation Strategy for Plastics” formulated in 2019, set a target of introducing approximately 2 million tonnes of bioplastics by 2030. In addition to biomass plastics such as polybutylene succinate (PBS) and polyhydroxyalkanoates (PHA), there has been a growing adoption of the mass balance approach, which allocates biomass content according to customer demands. Many material manufacturers have obtained ISCC PLUS certification and are working to accelerate the adoption. However, challenges remain, including the time required to educate end consumers with the concept of mass balance and the high cost of raw materials such as bio-naphtha.
However, challenges remain, including the time required to educate end consumers with the concept of mass balance and the high cost of raw materials such as bio-naphtha.
Technology development and new application exploration
Like overseas manufacturers, Japanese plastics producers are advancing technology development and exploring new applications in both mechanical recycling and chemical recycling. In the area of chemical recycling, various technologies are being developed and tested, ranging from methods targeting specific plastics to technologies that convert mixed or composite plastics into oil. By the 2030s, chemical recycling could become a game changer, potentially transforming the structure of the petrochemical industry. Efforts are already underway to establish trial equipment for polystyrene (PA) and acrylic resins, and in the fibresector, the use of PA and polyester fibres is expanding.
Toray has been developing chemical recycling products for over 20 years. They process edge material produced during manufacturing by depolymerising and repolymerising it to create PBT, working to expand and enhance its functional grades.
There are many obstacles to recycle engineering plastics, such as the presence of alloys with other plastics, various additives like reinforced fillers, and bonding with different materials like metals. However, multiple technologies are being employed to address these challenges, such as using recycled materials in alloyed materials, depolymerisation using subcritical water, and separation technologies for multilayer films, all aimed at achieving a circular society. Mitsubishi Chemical Group and ENEOS have jointly introduced oil-based recycling equipment in Ibaraki Prefecture, with an annual waste plastic processing capacity of 20,000 tonnes. In the second half of 2025, Idemitsu Kosan will launch its first unit at its Chiba plant, with an annual waste plastic processing capacity of 20,000 tonnes.
On the other hand, with the development of automotive electrification, the use of engineering plastics is expanding. There is a growing demand for materials that replace metals to achieve light-weighting without compromising properties such as heat resistance, strength, and rigidity, as well as materials with insulation and flameretardant properties for high-voltage battery areas. A trend is emerging where thermosetting resins and engineering plastics are used to replace metals around vehicle battery housings. It is necessary to design materials that are easy to disassemble during material conversion and disposal, and resin producers must address these design and material demands. In terms of recyclability, rapid progress is being made in developing uniform component materials for food packaging.
At Chinaplas 2025, the event will showcase comprehensive application solutions for plastics. Japanese plastics manufacturers can gain insights into the latest developments of Japanese enterprises and global chemical companies, as well as cutting-edge trends in the industry. This will drive the plastics sector towards a more sustainable and resilient future. For more information, visit: www.chinaplasonline.com. (Press Release)
(PRA)SUBSCRIBE to Get the Latest Updates from PRA Click Here»