Green news: Covestro opens pilot plant for biobased aniline; Corsair to supply pyrolysis oil to Shell Singapore
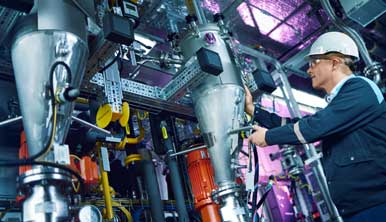
German materials firm Covestro says it is moving forward with the implementation of a unique process for producing the chemical aniline entirely based on plant biomass instead of petroleum for the first time. At its Leverkusen site, the plastics manufacturer has now put a special pilot plant into operation for this purpose.
Around 6 million tonnes/year of aniline are currently produced worldwide, with the volume growing by approximately 3-5% a year on average. With a production capacity of more than 1 million tonnes/year, Covestro is one of the leading aniline producers.
Initially, large quantities of bio-based aniline will be produced there, so that the new technology can be further developed for production and transferred to an industrial scale. In the plastics industry, aniline is used to produce MDI, among other things. This in turn is used for insulating foam, for example, which saves energy in buildings and reduces the CO2 footprint. Covestro believes it will contribute to the promotion of the Circular Economy, which the company is aiming to become fully aligned with.
In attendance at the opening ceremony were North-Rhine Westphalia’s Deputy Minister President Mona Neubaur as well as Professor Walter Leitner, Managing Director of the Max Planck Institute for Chemical Energy Conversion in Mülheim an der Ruhr. Together with Dr. Thorsten Dreier, Chief Technology Officer of Covestro, they discussed the significance of bio-based raw materials for a sustainable chemicals industry of the future.
“Among other things, aniline is a key raw material for foams used to insulate buildings and refrigerators,” explained Dreier, on the significance of the base chemical. “Until now, aniline has been produced from fossil raw materials such as petroleum, which releases CO2 and fuels climate change. With our new process, we are contributing to building up a circular, bio-based economy, and I am very proud that we have now succeeded in making the jump to the next technological level.”
Covestro developed the process, which has already won several awards, together with partners in the scientific community. Compared to conventional technology, the process leads to a greatly improved CO2 footprint of aniline. Covestro has made a seven-digit investment in the pilot plant at the Chempark Leverkusen.
Professor Leitner also underlined the importance of partnerships. “The project illustrates the cooperation between research-based industry and application-oriented science. There are many intersecting partnerships like these, especially in NRW. Germany needs more of this in order to assert itself as a research and technology location.”
The project also clearly showcases the potential contribution of the industrial (“white”) biotechnology to plastics production: in the new process, a customised microorganism helps convert an industrial sugar extracted from plants into an intermediate product through fermentation. This takes place under milder and thus more environmentally compatible conditions than in conventional processes. In a second step, chemical catalysis of the intermediate product then creates the aniline with one hundred percent plant-based carbon.
The research on biobased aniline will also continue to be funded by the German government. The German Ministry for Food and Agriculture is funding a follow-up project (Bio4PURDemo) from Covestro and partners, which started in March 2022 and runs until 2025.
The RWTH Aachen with the CAT Catalytic Centre and the University of Stuttgart, as well as the technology transfer initiative located there, are also participating in the project.
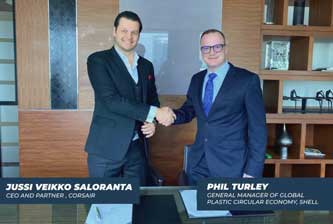
In other news, Thai waste recycling firm Corsair Bangkok Company Ltd (Corsair), which has its European head office in the Netherlands, will supply Shell Singapore Pte Ltd (SSPL) with pyrolysis oil, a mixed plastic waste feedstock.
Corsair operates a chemical recycling facility in Bangkok with an output of around 1 million litres/month of pyrolysis oil. It converts daily household plastic waste into what it calls advanced bio-oil.
Under the deal, Corsair will deliver pyrolysis oil from its plastic waste chemical recycling facility in Thailand to the Shell Energy and Chemicals Park Singapore on Bukom.
The pyrolysis oil will then be used to manufacture sustainable circular chemicals which are typically used in a wide variety of products found in everyday life like cleaning products, textiles, food packaging and others.
"At Shell, we believe chemical recycling offers a valuable and viable way to complement mechanical recycling measures, and is needed to achieve the higher recycling rates that are a must for the reduction of waste plastic into the environment. It is not just a partnership for innovation, but a commitment to a sustainable and circular future," said Phil Turley, General Manager of Global Plastic Circular Economy at Shell.
A consortium of companies, Corsair, which started its operations in Thailand and has recently expanded into Europe, has a target to expand Internationally for a greater positive impact on the environment, it adds.
Corsair aims to expand its plastic waste chemical recycling facilities globally, with its main focus on Asia, Europe and North America.
Corsair is also the developer and issuer of the plastic waste offset program, the CSR Plastic Credit. Through the CSR Plastic Credit, Corsair helps businesses and individuals to reduce and remove the impact their plastic waste has on the environment, by becoming Certified Plastic Neutral.
(PRA)SUBSCRIBE to Get the Latest Updates from PRA Click Here»