Recycling: Trinseo to build demo plant in Italy for PMMA recycling; Cyclyx to set up first waste plastics sorting centre in Houston
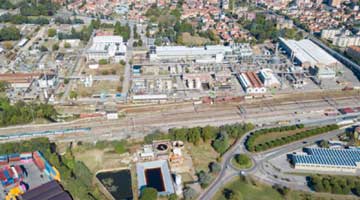
Materials provider Trinseo is to inaugurate its next generation polymethyl methacrylate (PMMA) depolymerisation plant in Rho, Italy, scheduled to be commissioned in Q1 2024.
PMMA, renowned for its versatility in various applications, will be transformed through this advanced recycling and purification process where it can go back into the plastics value chain and support the goal of circularity. This depolymerisation operation will be designed to enable the efficient recycling of end-of-life PMMA, as well as other difficult to recycle structures, which will ultimately be used to produce acrylic resins, sheets, and compounds containing recycled materials.
Depolymerisation is a chemical recycling technology which is complementary to more traditional mechanical recycling processes. While mechanical recycling is vital to a successful circular economy, depolymerisation creates brand new opportunities by reducing the polymer back to its constituent monomers.
This allows for the recycling of a wider variety of PMMA-based materials, supporting an increase in recycled content and overall recycling rates, and helping reduce the manufacturing demand for virgin materials.
Trinseo’s depolymerisation facility is being developed around a continuous recovery model to produce high quality recycled PMMA that matches the quality of its virgin counterpart, promoting a circular plastics value chain without compromising performance.
Using this advanced recycling technology, the introduction of recycled monomer into the supply chain helps support achieving targets for lowering carbon emissions, water consumption, and the conservation of natural resources, as indicated by the MMAtwo project's environmental benefits calculator.
A shift towards PMMA depolymerisation can help deliver sustainability benefits for consumers, manufacturers, and industries alike. From car lamps to signage and more, this technology creates the opportunity to give a range of everyday products a second life and beyond.
Material produced using the depolymerisation process will be integrated as part of Trinseo's distinctive “R-Life” portfolio designed around a commitment to sustainability, covering both mechanically and chemically recycled PMMA grades. These products find applications across mobility, construction, and consumer goods.
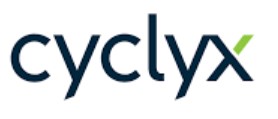
In other news, Cyclyx International, a joint venture among Agilyx, ExxonMobil, and LyondellBasell, announces a final investment decision (FID) to build the first Cyclyx Circularity Centre (CCC). The facility is designed to accept and process plastics that are currently going to US landfills for use in a range of recycling technologies. The facility, which is slated for start-up in mid-2025, will have capacity to produce 136,000 tonnes/year of feedstock for advanced and mechanical recycling.
"This milestone is evidence of the real progress we are making to increase the circularity of plastic waste as a resource," said Joe Vaillancourt, CEO of Cyclyx. "The first-of-its-kind CCC in Houston will serve as a blueprint, which we can replicate across the US to progress our long-term goal of increasing the recycling options for plastic waste. Cyclyx is proud to be an innovator and enabler for unlocking plastic's potential."
ExxonMobil and LyondellBasell are together investing US$135 million into Cyclyx to fund operating activities and construction costs for the new facility, which has an expected startup in mid-2025. Cyclyx is sourcing a combination of post-consumer, commercial, and industrial plastic waste of all kinds for the CCC.
Leveraging Cyclyx's proprietary technology, the CCC will accept, analyse, and process a wider range of plastic waste than what is traditionally accepted, including difficult-to-recycle plastics, such as food packaging, chip bags, and bottle caps. Cyclyx's technology has a comprehensive understanding of post-use plastics' complexity including polymer composition, additives, physical properties, and manufacturing processes. This comprises the Cyclyx feedstock database, which has been developed over 20 years, beginning at one of its founding companies, Agilyx.
The CCC will focus on sorting and custom blending collected material to ensure feedstock specifications and classifications meet expectations for ExxonMobil and LyondellBasell, who have offtake rights from the CCC. Throughout this entire process, Cyclyx adheres to stringent ISCC PLUS standards to ensure the delivery of traceable, certified feedstocks through the CCC.
Operations will create more than 100 jobs within the first CCC. Additional positions are expected to be created off site as a result of the CCC development, including in logistics and collection programs.
Cyclyx is exploring the development of additional CCCs across the US, with the goal of increasing the recycling rate of plastics and potentially diverting billions of pounds of plastic waste from landfills.
(PRA)
Subscribe to Get the Latest Updates from PRA Please click here
©2023 Plastics and Rubber Asia. All rights reserved.
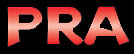
©2023 Plastics and Rubber Asia. All rights reserved.
Home Terms & Conditions Privacy Policy Webmail Site Map About Us