Manufacturing Industry: Trends in plastics manufacturing
The prevailing challenges faced by plastics manufacturers are being addressed through the implementation of strategies focused on digitalisation and new product development. Furthermore, despite the lower-than-expected adoption, technologies like AI present are a silver lining, says Angelica Buan in this report.
Exploring transformative potential of Industry 4.0/5.0
The plastics manufacturing industry is grappling with persistent challenges like potential economic uncertainty, a skilled labour gap, supply chain disruptions, and regulations for achieving net-zero emissions. To bolster production, competitiveness, and investments, the industry is poised to adopt strategies that target these obstacles head-on.
Certainly, in 2024, technology will play a significant role, helping manufacturers tackle upcoming challenges while improving efficiency and business resilience.
Smart factories, the integration of Artificial Intelligence (AI), and the development of new and sustainable materials are among the scenarios companies are exploring to elevate their operations and generate added value.
Manufacturers, worldwide, including those in the ASEAN region, are increasingly exploring into digital technologies under the banner of Industry 4.0. This surge is propelled by advancements in storage and computing capabilities, resulting in widespread adoption across various industries.
Insights from consultancy firm McKinsey’s survey conducted in the ASEAN region reflect a notable confidence in the transformative potential of Industry 4.0/5.0. The majority of respondents anticipate the emergence of new business models and improved performance through the adoption of these frameworks.
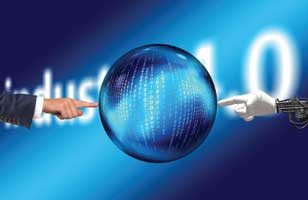
Yet, within the region, there's a spectrum of adoption rates: some are limited adopters, some are lagging behind, and others are leading the charge in digital technology.
Against this backdrop, PRA queried Raimund Klein, CEO of Singapore-based International Centre for Industrial Transformation (INCIT), about how the Asian manufacturing sector is adapting to global trends such as Industry 4.0/5.0 and the Internet of Things (IoT).
Klein emphasises that, both in ASEAN and globally, the implementation of Industry 4.0 across processes, technologies, and organisations is still in its early stages. On a global scale ranging from 0 to 5, the aggregated digital transformation data stands at "1.55," signifying the early phase of this transition, he explained.
Klein also touched on Industry 5.0 and the encryption of physical systems, highlighting the necessity of establishing communication protocols among collaborative robots (cobots) for effective cooperation.
Regarding IoT connectivity, he noted a deficiency in products, especially in supporting SMEs and mediumsized companies. Despite these businesses prioritising automation, Klein emphasises the strategic importance of measuring the impact of their technologies. Enabling IoT is crucial to drive productivity and visualise the real impact of these advancements, he said.
Consequently, it is evident that ASEAN manufacturers need to catch up in seizing the vast opportunities presented by these technologies, avoiding the risk of overlooking potential benefits.
Rise of smart manufacturing with AI
According to audit consultancy Deloitte’s 2024 manufacturing industry outlook, the majority of surveyed manufacturing executives believe that smart factory solutions will drive competitiveness in the next five years. Deloitte’s research consistently demonstrates improvements in cost, throughput, quality, safety, and revenue growth through smart factory technologies, combining capabilities in IoT, cloud and edge computing, AI, and vision systems, among others.
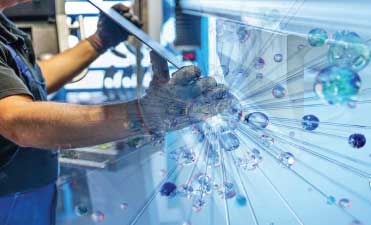
The implementation of smart factory solutions enhances asset efficiency, labour productivity, product quality, and significantly reduces costs while prioritising safety and sustainability within manufacturing operations. Smart manufacturing encompasses various technologies and solutions, including AI.
Augury, a provider of industrial AI solutions enhancing machine and process health, recently released its The State of Production Health 2023 report. This study surveyed over 500 US and Europe-based manufacturing executives, primarily from organisations representing consumer packaged goods, food and beverage, paper, building materials, cement, wood, mining, oil and gas, and chemical industries, with global revenues exceeding US$100 million.
The report indicates a mixed sentiment regarding the manufacturing direction. While most executives believe that technology adoption will positively impact workforce upskilling efforts, the goal of implementing Industry 4.0 remains for only a fraction of manufacturers globally.
External factors such as supply chain disruptions, workforce challenges, environmental crises, and impending regulations are accelerating the industry's need to adopt technology rapidly.
Regarding AI investment, the report signals a surge in commitment, with only a small fraction planning to reduce AI spending in 2023 (3%), while a substantial majority (63%) plan to increase their AI budgets.
However, despite widespread AI use, there's considerable variability in quantifying its impact, leaving leaders uncertain about its overall value. The report identifies upskilling the workforce as the primary objective for leveraging AI in 2023, followed by increasing capacity and streamlining supply chain visibility.
In terms of AI applications, the report emphasises production health—integrating insights from machines, processes, and operations—as a key area, ranking closely behind supply chain optimisation.
Augury's CEO/Co-Founder, Saar Yoskovitz, stresses the importance for industrial leaders to address existing challenges while viewing AI as a supportive tool for jobs. Strategising for scalable success and making substantial progress in sustainable production goals are crucial, leading to enhanced workforce skill sets, reduced environmental impacts, and improved financial performance for organisations embracing this approach, he adds.
(PRA)
Subscribe to Get the Latest Updates from PRA Please click here
©2023 Plastics and Rubber Asia. All rights reserved.
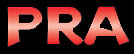
©2023 Plastics and Rubber Asia. All rights reserved.
Home Terms & Conditions Privacy Policy Webmail Site Map About Us