Coperion energy-efficient process for ABS blends licensed by Zhejiang Zonepic
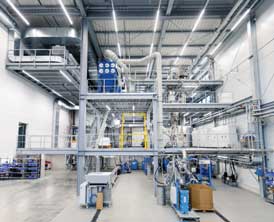
German compounding/extrusion machinery maker Coperion has developed a process solution for particularly energy-efficient manufacturing of acrylonitrile-butadiene-styrene copolymer (ABS) blends, with the Coperion ZSK Mc18 twin-screw extruder playing a key central role. Thanks to short raw material residence time in the ZSK extruder and gentle product handling, Coperion’s process solution achieves an extraordinarily high ABS blend product quality.
ABS is a thermoplastic engineering plastic which combines numerous positive mechanical properties and chemical stability, which make it ideal for multiple uses in the electric and automotive industries
Technology licensing and engineering company Zhejiang Zonepic Petrochemical Technology Co., located in Hangzhou City, Zhejiang Province, China, is a licensor for the emulsion grafting-bulk polymerisation ABS blend method that allows for the production of ABS blends in general grade, food grade, flame retardant grade and electroplating grade.
For this solution the company has permitted to design several large installations with multiple ZSK 133 Mc18 twin-screw extruders.
Two systems have recently started production: one plant is at Lihuayi Lijin Refining & Chemical Co. with an output of 200 kilotonnes/year, and the other at Zhejiang Petroleum & Chemical Co. with an output of 400 kilotonnes/year
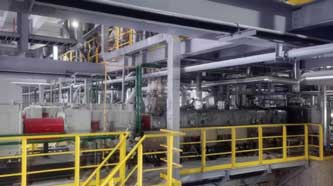
ZSK extruders for maximum energy-efficiency
ABS blends consist of synthetic rubber polymers HRG and SAN (styrene-acrylonitrile). Coperion has developed a particularly energy-efficient process solution for manufacturing ABS blends.
The ABS emulsion emerges wet from a reactor following its manufacture. In Coperion’s solution, it passes through a screw press before the HRG – still damp – is introduced downstream via a Coperion ZS-B side feeder into the process section of a ZSK extruder. The energy-intensive thermal pre-drying of the ABS is thus eliminated.
Using gravimetric Coperion K-Tron feeders, SAN and additives are likewise introduced into the ZSK extruder. SAN, additives and HRG are intensively and homogeneously mixed in the ZSK process section, all the while handled very gently, so that the product does not yellow, nor does the polymer break down.
In comparison to conventional manufacturing processes, Coperion’s solution operates with markedly lower energy consumption. Moreover, the portion of residual monomers is reduced to an absolute minimum.
Frank Lechner, General Manager of Process Technology and Research & Development at Coperion, is convinced of the importance of Coperion’s development: “We’re proud to see how both of these large installations from Zhejiang Zonepic Petrochemical Technology Co have successfully taken over production for ABS blends. These machines are already proving on a daily basis how energy-efficient their operation is. At the same time, they deliver a constant, extremely high product quality that underscores how our innovative process development precisely meets our customers’ requirements. Even our newest development, providing a way to further reduce ABS production’s energy consumption, has already met with great interest – as has our solution for manufacturing ABS blends for direct contact with food products.
New Coperion test centre for optimising plastics recycling
In other news, Coperion has successfully launched operation of its new Recycling Innovation Centre. In this high-tech test centre for plastics recycling applications, every recycling process step – from material handling and feeding to extrusion, compounding, pelletising, material post-processing and deodorisation – can be tested. Extensively equipped recycling systems are available that can be modified in myriad ways, depending upon the specific requirements of the recyclate to be produced.
Coperion says its new centre is the perfect complement to the Herbold Meckesheim Test Centre, where customers can simulate and test the mechanical pretreatment of plastic, allowing customers to experience first-hand the significant reduction in organic impurities by using Herbold Meckesheim’s hot washing system, as an example. Herbold Meckesheim has been part of Coperion’s Recycling Business Unit since 2022.
The recycling centre is located in Niederbiegen near Weingarten, Germany, directly adjacent to Coperion’s existing test centre for Bulk Solids Handling. Along with proprietary R&D projects, first tests have been performed for customers, in which new, sustainable products and recycling processes have been developed and tested.
Coperion says its process engineers can modify the available recycling technologies such that the recompounds are manufactured with the highest efficiency possible while maintaining a consistently high level of product quality. The results achieved can then be scaled up to production level thanks to the constant base parameters of all Coperion technologies.
Every new technological development from Coperion that optimises plastics recycling has been integrated into the recycling centre’s machinery and can be tested there.
For example, in the area of material conveying, the energy-efficient Fluidlift ecodry flash drying process is available – moisture remaining in recycling grinds following the washing process is reduced during material transportation.
Moreover, the Mix-a-Lot bulk solid mixer, which can create premixes including flakes or powders, and the innovative buffer hopper solution using the ARW discharge agitator as well as the Smart Weigh Belt (SWB) feeder are integrated in the system.
Coperion has also installed the ZS-B MEGAfeed side feeder, especially for extruding and compounding plastic recyclates with bulk densities starting as low as 20 kg/cu m at high throughputs. With its innovative design, the ZS-B MEGAfeed handles flakes and fibres such that they can be fed into a ZSK twin-screw extruder in large quantities without energy-intensive compacting.
(PRA)
Subscribe to Get the Latest Updates from PRA Please click here
©2023 Plastics and Rubber Asia. All rights reserved.
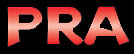
©2023 Plastics and Rubber Asia. All rights reserved.
Home Terms & Conditions Privacy Policy Webmail Site Map About Us