Masterbatches/Additives: Creating a sustainable version of plastics
Plastics are becoming more sustainable as a result of new additives that improve recyclability and durability while also raising the quality of post-recycled materials.
Granular-sized solutions benefit the environment
Despite criticism of plastics, the industry is working to create polymers that not only overcome the negative connotations associated with them -- such as their inability to be recycled or getting washed into the environment as microplastics -- but also support their sustainability goals.
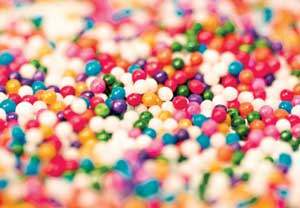
With advances in material technologies, addressing the environmental impact of plastics while improving their properties to meet a wide range of industry requirements for the material is no longer rocket science.
Thus, incorporating masterbatches and additives into virgin polymers in the production of plastics can improve the properties of plastics such as the colour or modify the materials with stabilisers, antioxidants, antistatic agents, flame retardants, or other plastic additives that are compatible with different applications.
The masterbatch market is expanding. According to research company Ceresana, global demand for masterbatches is expected to reach 5.5 million tonnes by 2031, with colour masterbatches dominating the demand and plastics for packaging accounting for 36% of the demand share, followed by construction, transportation, electrical, and industrial applications.
Brands pivoting to more recycled content
Consumer brands want to see more recycled plastic content in their products and to enable multiple uses of their products to increase their sustainability.
Major global trade platforms, such as the recent K2022 Show in Germany, are championing this strategy. The former highlighted the most recent plastic masterbatches portfolios, whose increasing use is enabling plastic circularity.
US-based materials firm Milliken & Company showcased its new DeltaFlow viscosity modifier for recycled polypropylene (rPP). The company, which claims to be the only one offering this latest chemistry in an easy-to-handle, non-dusting, solid concentrate form for the recycling market, believes that DeltaFlow grades will benefit PP recyclers by increasing the melt flow rate of rPP for injection moulding processes.
According to Allan Randall, Global Product Line Manager, the technology also has lower volatile organic compounds (VOCs) and improved organoleptics, and it could complement the advances being made in recycling.
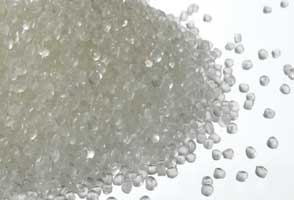
The product allows rPP to replace virgin resin in a wide range of end-use applications, and it allows brands to incorporate more rPP into their products, making it easier for them to meet their sustainability targets.
Stabilisers to improve recycling
Recycling is central to the circular economy vision. Mechanical recycling, which has remained the most important and widely used recycling method, is being supplemented by advanced recycling technologies.
Mechanically recycled plastics will eliminate more than 1.7 million tonnes of virgin polymer feedstock by 2030, up from 688,000 tonnes in 2020, according to S&P Global Platts Analytics.
Songwon Industrial, a South Korean specialty chemicals manufacturer and exhibitor at K2022, is focused on mechanical recycling of PCR with its range of re-stabilisation antioxidants.
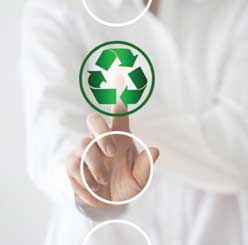
The primary and secondary antioxidants in the Songnox binary blends family have been “specially evaluated” for mechanical recycling of polyolefins (POs), Songwon said. The blends enhance processing as well as long-term thermal stability, enabling recyclers to provide better, more affordable recycled resins.
Without stabilisers added during processing, the melt-flow characteristics of mechanically recycled PP changes quickly, sometimes drastically, leading to poor processing and the loss of mechanical properties. According to Thomas Schmutz, Leader Global Technical Service, Testing & Application Development at Songwon, using the company’s blends results in higher-quality, more cost-effective materials.
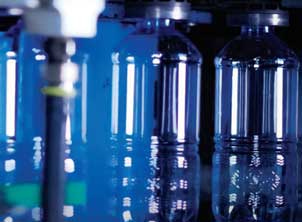
Also at the K2022, additives manufacturer SI Group rolled out its Evercycle additives brand for recycling. For PET recycling, it is said to provide process stability, colour control, and lower acetaldehyde levels. Benefits of polyolefin recycling include process stabilisation and improved performance, allowing for higher recycled content.
Other Evercycle products on display at the show included the PET-102D for colour control in PET bottles, trays, and fibres (pellet form); PET-103D for colour control in PET bottles, trays, and fibres (liquid form); PP-101S for stabilisation in HDPE and PP flexible packaging, and LD-101S for stabilisation in LDPE rigid packaging.
According to Irfaan Foster, Market Development Director at SI Group, the formulated additive solutions encourage more plastics to be recycled back into the economy, resulting in a more sustainable industry.
(PRA)
Subscribe to Get the Latest Updates from PRA Please click here
©2022 Plastics and Rubber Asia. All rights reserved.
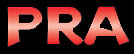
©2022 Plastics and Rubber Asia. All rights reserved.
Home Terms & Conditions Privacy Policy Webmail Site Map About Us