Sustainability: Partnerships for sustainable solutions
Midea, GER and Ineos Styrolution create large-scale home appliance from ABS Eco grades
Styrenics manufacturer Ineos Styrolution says that its ABS Eco grades, manufactured from post-consumer recycled (PCR) ABS produced by GER , have been successfully validated by Chinese household appliances firm Midea for its range of household appliances, including air conditioners, refrigerators and water dispensers.
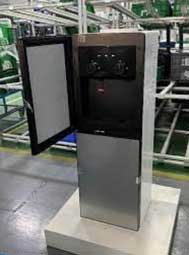
Established in 1968 and headquartered in Southern China, Midea is the global leader for household appliances and air conditioners, owning the most comprehensive white goods portfolio; while GER is a waste recycling enterprise based in China’s Jiangxi province. Recently, Midea demonstrated the production of the pilot product using the new recycled material provided by Ineos Styrolution.
This first step is an important milestone for the establishment of a closed-loop circular economy system, by which Ineos will produce ABS Eco and PS Eco grades using Midea’s products at their end-of-life, after being dismantled and recycled by GER. These grades, specially tailored made for Midea, will then be used as a drop-in solution to manufacture Midea’s home appliances.
The next steps are for Midea, GER and Ineos to validate the use of PS Eco grades on a commercial scale at Midea’s production facilities, finalising an integrated supply chain solution starting from Midea’s finished goods, to recycling after their end-of-life, and turning them into PS Eco and ABS Eco grades exclusively for Midea.
Alpla’s packaging for beauty products reduces emissions by 71%
Packaging and recycling specialist Alpla has realised a carbon-optimised prototype solution as a showcase for future products with its Canupak beauty care packaging. The ultralight packaging system has a bottle made entirely of recycled HDPE (rHDPE) sourced from the company’s own plants in the EU and produced using renewable energies.
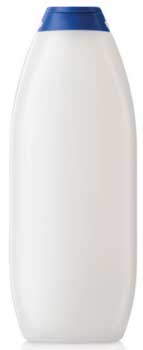
The ultralight Canupak packaging system boasts around 71% less carbon consumption than with comparable packaging types, allows for complete recyclability of the bottle and cap, and a total weight of approximately just 14 g.
Alpla says Canupak is a prime example of how the potential to minimise emissions can be explored with packaging systems.
The carbon footprint was calculated in cooperation with ClimatePartner. The product carbon footprint (PCF) comprises all the emissions throughout a product’s life cycle, including its disposal. The areas of package contents, retail and use phase were not taken into account as these are not relevant to the climate impacts of packaging.
As no clear standards currently exist for climate-neutral products and offsetting certificates, Alpla adds it is focusing on reducing emissions within its own sphere of influence.
“We are focusing on further optimising our products and on maximum recyclability based on design for recycling, and are on the lookout for partners who wish to take the next step in reducing their carbon footprint together with us,” reports Project Manager Karina Pölzl.
Alpla is also targeting all packaging to be fully recyclable by 2025, with PCR material accounting for 25% of the materials processed. The company is investing EUR50 million a year in recycling activities to this end.
TotalEnergies, W&H and Mitsubishi Chemical develop recyclable PE packaging
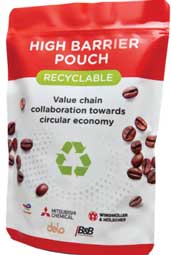
Chemical firm TotalEnergies , German extrusion machinery maker Windmöller & Hölscher (W&H) and Mitsubishi Chemical have developed a fully recyclable high barrier packaging, to replace multimaterial structures (like e.g., metallised BoPP/PE or metallised BoPET/PE), in line with brand owners’ commitments to 100% recyclable packaging by 2025.
Composed of 98% PE and less than 2% EVOH, required for barrier properties, the new solution exhibits identical performances without any compromise on recyclability, allowing to enter available recycling streams and thus contributing to address the challenge of plastics end-of-life.
It consists of a Machine Direction Orientation (MDO) film and a sealing film, laminated together by Dettmer Verpackungen GmbH .
Machine manufacturer B&B Verpackungstechnik then transformed this structure into a stand-up pouch that could be used for demanding applications, such as coffee packaging.
The MDO-PE film recipe, composed of TotalEnergies Supertough, and Lumicene HDPE together with Mitsubishi Chemical’s Soarnol, was running on a W&H Varex II equipment at the K2022 show.
Domenico De Angelis, General Manager Sales Soarnol, P&C MMA Business Group EMEA of Mitsubishi Chemical Group said that the combination of chosen barrier materials, together with machine technology, met the needs of high water-vapour, oxygen and aroma-barrier for the packaging. “Furthermore, the structure can be declared by definition as mono-layer solution, and it is also fully mechanically recyclable,” he explained.
Sabic and Cabka collaborate on transport packaging solutions
Chemical firm Sabic and sustainable and reusable transport packaging firm Cabka have collaborated to launch the CabCube 4840, said to be the next generation in foldable large containers and an alternative to traditional metal/ wooden cages for the transport of goods.
Cabka approached Sabic looking for a 100% recyclable lightweight polymer material solution to produce its CabCube 4840. Within less than six months, the two companies had collaborated to develop several high performance PP compounds.
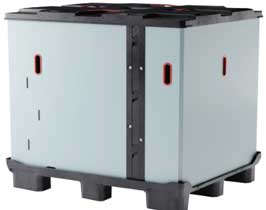
These compound-solutions provide improved processability, high compression strength, high impact, and weight reduction. Some of these compounds are unique grades in Sabic’s foam and lightweight portfolio as they are flame-retardant, halogen-free and UL94-V0 certified.
“Sabic offers more than 20 innovative foam and lightweight solutions enabling customers and partners across the entire value chain to overcome the challenges they face to meet consumer demand for smarter, more sustainable solutions,” said Abdullah Al-Otaibi, ETP & Market Solution General Manager at Sabic.
Sabic and Cabka are also working together on polyolefin compound solutions containing mechanically recycled content. In addition, the two companies aim to join forces to improve Sabic’s logistical/ packaging systems – replacing ‘one way’ wooden pallets and cardboard octabins with lightweight, returnable plastic alternatives, starting at the Sabic compounding asset in Genk, Belgium.
SML’s C-PET light cup for hot-filling promotes recycling
At K2022, Austrian extrusion machinery firm SML presented the results of its joint R&D activities with Sukano AG and Kiefel Packaging a C-PET light cup that combines transparency and recyclability as well as suitability for thermoformed hot-filling or microwavable products. Further advantages include short cycle times during thermoforming and a high stiffness. The newly developed C-PET light can thus be a reasonable option for manufacturers looking for an economic and easy-to-recycle alternative to PP and PS.
“Because easy recyclability is becoming increasingly important, we opted for a transparent C-PET solution at an early stage of our joint research and development work,” says Max-Phillip Lutz, Product Manager at SML. Compared to coloured PET or PP and PS products, the recycling process of C-PET light is considerably easier.C-PET light products do not cause any problems in existing recycling streams and facilities of post-consumer or post-industrial PET materials.
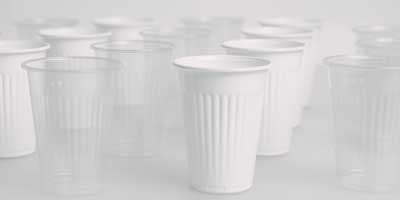
In general, C-PET is temperature resistant up to 220°C. However, this is not necessary for many applications and limits the output in thermoforming. In contrast, C-PET light was developed to withstand a maximum temperature of 100°C. The new C-PET light enables the manufacturing of transparent thermoformed products for hot-fill applications up to 100°C at output rates comparable to those of conventional A-PET processes. Especially the shorter cycle times during thermoforming are an economic advantage compared to conventional C-PET.
All three project partners shared their specific expertise and their profound experience in their respective areas in order to improve every single step in all processes. The main technical challenges were to find the optimum dosage for the additives, to adjust the formulations and the process technology during film production, and to find the right parameters for the thermoforming process.
Key characteristics of C-PET light are that it is suitable for transparent applications; allows for short cycle times and high output compared with C-PET, has high stiffness compared with PP and is recyclable.
SML’s stretch film line processes Braskem’s PCR resin
At K2022, SML’s PowerCast XL, a 4.5 m-wide stretch film line with a net output capacity of up to 3,400 kg/hour, was processing a new type of PCR resin developed together with Brazilian materials firm Braskem into premium stretch film. Plus, a technical highlight of the PowerCast XL is its patented triple turret winder: said to be the first in the market for manufacturing 2” stretch film hand rolls on a 4.5 m wide line.
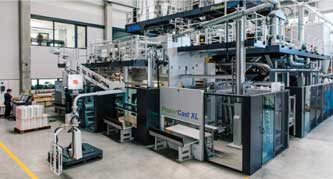
“SML PowerCast XL can be fitted with a 7 to 67 layer feedblock, and it comes with the biggest chill roll of 1,600 mm in the field. Nevertheless, it requires only 240 sq m floor space,” said Thomas Rauscher, Product Manager at SML.
The PowerCast XL was able to process 30% PCR material that came from mechanical recycling. The newly developed Wenew DL085C resin is a 100% PCR resin and allows the production of completely transparent stretch film with excellent mechanical properties on SML stretch film lines. SML adds that these films are highly resilient and withstand strong mechanical loads, i.e. in the area of transport safety or for automatic applications in the beverage industry.
Rauscher speaking about the joint development works with Braskem said that at first it seemed impossible to find a sustainable and economical solution, especially when it comes to downgauged products. “Finally, after two years of very close collaboration, development work and countless trials together with Braskem, we are now in a position to offer the market a solution to the PCR demand in stretch film production which is certain to delight end users. And a satisfying answer on both the raw material side as well as the manufacturing side,” he added.
Furthermore, SML’s newly patented turret winder W4000- 4S-3T, a “three-turrets-in-one-frame” concept supports significantly higher production speeds for maximum output quantities – especially at the lighter 2” rolls.
“The possibility to manufacture also 2” rolls on that 4.5 m wide increases the product diversity and productivity of our PowerCast stretch film line significantly,” added Rauscher.
Until now, it was only possible to run 2” hand rolls on lines up to 3 m width, thus the new development boosts the output of hand rolls by about 50 %. As before, 3” hand rolls, machine rolls and jumbo rolls an also be manufactured, with ease, with this new solution, according to SML.
(PRA)
Subscribe to Get the Latest Updates from PRA Please click here
©2022 Plastics and Rubber Asia. All rights reserved.
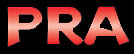
©2022 Plastics and Rubber Asia. All rights reserved.
Home Terms & Conditions Privacy Policy Webmail Site Map About Us