Packaging: Revolutionising the packaging sector
Graphene-biopolymer to reduce waste
While biodegradable plastics currently exist, they rely on
commercial composting, which uses energy to heat the
compost, as well as presenting other logistical challenges.
In addition, some bioplastics produce methane gas when
they decompose, a compound with a global warming
potential 25 times that of CO2.
Thus, UK biotech company Toraphene is preparing to unveil what it says is the world's first truly biodegradable, compostable and commercially viable alternative to plastic packaging. The company has developed a new material, also called Toraphene, that uses biopolymers that compost naturally and biodegrade, as well produce CO2 along with mulch that can be used to fortify topsoil.
The biopolymers are combined with graphene, which is derived from carbon and is stronger than diamond at an atomic level.

“Amidst a climate crisis, plastic waste is known to be a huge, global problem and many plastic alternatives now exist, so why don’t we see them everywhere?” asks Gaute Juliussen, CEO/Founder of Toraphene. “It’s because they need specific manmade conditions to biodegrade, and many degrade into microplastics, which contaminate our oceans and food chain for centuries”.
Such bioplastics have “effectively been ‘greenwashed’ and mis-sold to environmentally responsible consumers and companies,” continues Juliussen. “They also tear easily, shorten the shelf-life of the contents they contain and cannot be produced economically at scale”.
Due to the addition of graphene, Toraphene has been shown to be stronger, thinner, and less permeable than alternatives, improving food safety and shelf-life. This presents the first commercially viable alternative to plastics.
An entrepreneur, venture capitalist and former Associate Professor of Business, Juliussen founded Toraphene in 2018 with the initial aim of creating a green alternative to carrier bags and food and drink containers. Such plastics make up 23% of marine waste.
Ahead of the launch of Toraphene, which is patented in the UK, EU, and the US, Juliussen is launching an equity crowdfunding campaign on Crowdcube, encouraging anyone who cares for the environment to be part of the Toraphene journey.
Toraphene is renting production equipment from plastic bag manufacturers and plugging directly into existing supply chains. The company is already in talks with major consumer brands, retailers and food packaging suppliers.
Ultimately, Toraphene aims to render plastic packaging obsolete and disrupt the $4 trillion plastics industry.

Over 50% virgin plastics substituted in shrink film
Broadening the market potential of plastic recyclates
and thereby furthering the uptake of recycled content
across Europe is recycling company APK AG’s core
objective. The German firm has tested the performance
of its Newcycling LDPE recyclates in shrink films during
several projects undertaken over the course of this past
year. Primary test results showed that the recyclates
were able to deliver on the key functional issue of
shrinkage. Film thickness was able to be maintained at
the same level as with virgin plastics. Formulation of the
shrink films and extrusion parameters remained close to
the virgin feedstock version.
Collation shrink film is a demanding packaging application – for virgin polymers and all the more so for recycled materials. It needs to have a specific toughness, holding force, and shrink performance for it to guarantee package integrity as well as the necessary stability for storage and transport. Process parameters should remain constant when switching from virgin to recycled feedstock. Beyond this, as the film may be used as secondary packaging for bundling several products, making it the first thing the consumer sees, optics need to be of a highenough quality.
Collation shrink film is a demanding packaging application – for virgin polymers and all the more so for recycled materials. It needs to have a specific toughness, holding force, and shrink performance for it to guarantee package integrity as well as the necessary stability for storage and transport. Process parameters should remain constant when switching from virgin to recycled feedstock. Beyond this, as the film may be used as secondary packaging for bundling several products, making it the first thing the consumer sees, optics need to be of a highenough quality.
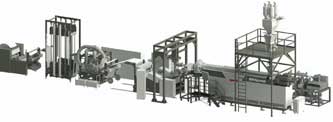
APK says its Newcycling dissolution recycling process can easily separate different polymers in multilayer plastic packaging – up to now, deemed non-recyclable – and transforms the target polymer into re-granulates with close to virgin properties.
Dissolution recycling is an advanced physical recycling technology. Building on a mechanical pre-treatment step, it adds a solvent-based process step, during which the target polymer is separated and purification of contaminants, such as various additives or organic residues, also takes place. APK’s recycled LDPE, used during the shrink film tests, is marketed under the Mersalen brand. It is derived from complex PE/PA multilayer film waste.
Increasing recycling quotas, potential mandatory use of recycled plastics in products across the EU market and a recently published Chemicals Strategy for Sustainability pushing strongly for a toxic-free environment: the European Commission has piled up a number of demanding challenges to the plastics and packaging value chains. However, bridging the gap between increased use of recycled plastics and attainment of the performance required for specific packaging applications can be facilitated by driving innovation in both design and technology.
APK’s Newcycling process generates plastic recyclates of close to virgin quality, which are suitable to be used in cosmetic packaging.
PET tray-to-tray recycling in one step
If a circular economy is to be realised, it will be necessary
to consistently recycle post-consumer thermoformed PET
trays back into PET trays. Currently, extensive use is made
of rPET from bottles in the manufacture of PET trays but
this supply of feedstock will continue to decrease. As part
of the circular economy, PET bottle flake is increasingly
recycled into new bottles.
The recycling of regrind from post-consumer PET trays to new sheet for PET trays presents challenges for the recycling process, such as the intrinsic viscosity of the regrind from PET trays is too low to permit direct recycling on a conventional sheet extrusion line. It is also unavoidable that tray regrind will be cross-contaminated with other polymers, as it is difficult to completely exclude other polymers, especially due to co-extruded or laminated layers.
Thus, for this demanding process of tray-to-tray recycling, machine maker Gneuss has developed the MRSjump extruder, which combines the decontamination performance of the MRS degassing extruder with a viscosity boost.
Furthermore, Gneuss says the extrusion process does not necessitate any pre or post-treatment of the input material, such as crystallisation or pre-drying of the recycled material or an IV boost in a solid state polycondensation (SSP).
It also adds that the high degassing efficiency of the extruder makes it possible to comply with EFSA and FDA limits without time and cost-intensive upstream or downstream material treatment.
Other benefits are the simple set-up, compact design and the ability to process a wide range of materials, from regrind from mono and multi-layer trays to material combinations that would stick together in a conventional thermal pre-treatment process (e.g. sheet regrind from PET/PE, GAG, certain copolymers).
Thanks also to the short process chain, the melt remains within a narrow, defined residence time spectrum. The thermal and mechanical stress on the material is kept low, allowing for mechanical and optical sheet properties.
Thus, recycling and decontamination are for the first time made possible with the MRSjump Extruder, within one single extrusion step, without upstream or downstream material treatment steps. This opens up new possibilities for the recycling of tray regrind.
(PRA)
Subscribe to Get the Latest Updates from PRA Please click here
©2020 Plastics and Rubber Asia. All rights reserved.

©2020 Plastics and Rubber Asia. All rights reserved.
Home Terms & Conditions Privacy Policy Webmail Site Map About Us