Year-end Summary: 2020, trouble in paradise for major industry sectors
Companies are rewriting their growth stories – with new perspectives of connecting directly to their customers, as well as collaborating with industry peers, and quickly responding to changes, says Angelica Buan in this report.
Pandemic blues – economies tumble
The struggle is real for economies that succumbed to the hydra of Covid-19. The global economy is projected to potentially incur a US$1 trillion-loss due to the pandemic, aggravated by supply chain disruptions from China and a drastic drop in oil prices, according to the United Nations Conference on Trade and Development (UNCTAD).
Though China, the world’s factory, has been forecast to witness a 0.1% drop in GDP in 2020, with further reduction of 0.4% in annual growth due to its trade tiff with the US, its economy has gradually recovered to be the world’s largest, overtaking the US, according to the IMF’s World Economic Output 2020 report.
Over and above, the pandemic has marked an unprecedented disruption across industries globally. It has been a tough year: with industries hit by low to zero sales and demand, streamlined workforce, lockdowns and mobility restrictions.
The airline industry, for example, has seen massive layoffs as fleets had been grounded for months on end; the automotive sector, which had already been in a slump, saw declining demand for light vehicles and passenger vehicles from China, Europe, the ASEAN and the US.
Medical and packaging sectors fly high
Contrariwise, the medical and packaging sectors have grown this year, which provided a positive outlook for machine manufacturers catering to the mentioned sectors.
The medical sector witnessed a windfall with demand shooting up for personal protective equipment (PPE) and telemedicine technologies.
The rising Covid-19 cases and risks of infections accelerated the demand for PPEs. The World Health Organisation (WHO), as well as several governments, distributed PPEs to countries that indicated rising counts of infected patients. At the onset, an estimated 89 million medical masks/ month; 76 million gloves and 1.6 million/month of goggles were required for the Covid-19 response, according to WHO.
WHO also urged industries and governments to increase their production of PPEs by 40% to meet rising global demand. But even then, PPE manufacturers, going beyond their maximum capacities already, are still short of fulfilling the continuous demand that is increasing day by day.
Machine makers rise up to the challenge of meeting PPE shortages
Some machine makers took the bull by the horns to meet the demand for PPEs by repurposing their production lines.

One such machinery firm SML started industrial production of PET sheet, the main component in plastic face shields, at its headquarters in Redlham, Austria. Production is taking place on a line for calendered sheets, with the extrusion line producing enough material for up to 10,000 face shields/ hour. The sheets are processed into face shields by compatriot extrusion machine supplier Kiefel in Freilassing, Bavaria. Two types of face shields are produced - based on 0.3 mm and 0.15 mm thin PET sheet, respectively. The PET sheet can be recycled 100%, for example, along with PET bottles and other PET products.
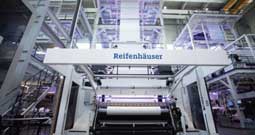
German extrusion line maker Reifenhäuser, in March, temporarily produced meltblown to make about 1 million face masks/day at its technology centre. It also converted another pilot line for production of protective film for the manufacture of medical coveralls for use in hospitals. The same line type was also capable of producing hygienic film for use in diapers, besides certified medical protective film. Ultra Stretch technology can also be used in other advanced applications, such as recyclable All-PE film (PET replacement). The production unit can therefore be used flexibly to respond to a wide variety of market demands outside of an emergency or crisis, Reifenhäuser said.
Indian machinery maker Rajoo Engineers, meanwhile, built a fully automated N95 mask making machine capable of producing 1 mask every 2 seconds, or 1,800 masks/hour. The automation ensures that the masks are hygienic and produced with minimum wastage as well as minimal human intervention, said the blown film and sheet extrusion line machine maker. The Rajkot-based company offers either the entire fabricto- mask solution or just the mask making machine, depending on the needs of the processor.

German machine maker Arburg has also been active during the pandemic. An example is the multifunctional face mask, which was developed in collaboration with partners and made ready for series production in only 41 days. In May, it started production of face masks made from LSR and PP, for everyday use, followed by the design and manufacture of a supplementary disposable filter that can be easily attached to the mask opening. Its partners in the project were Sigma Engineering (LSR component and mould simulation), Polar-Form (LSR mould), Foboha and Wilhelm Weber (thermoplastic moulds), Ewikon (cold runner), Elmet (LSR dosing unit), Männer and Günter (hot runner technology), Barth Mechanik (gripper), Wacker and Borealis (material), Karl Küfner (filter design), Herrmann Ultraschall (welding technology) and Packmat
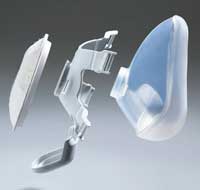
The question as to whether Arburg will be producing masks for the market as an injection moulding company in future is clearly answered in the negative, with the company saying it does not want to earn money with the production of masks, “but rather wanted to show how such high-quality products can be developed quickly and manufactured economically in series production."
Order backlogs create good vibes for some
Meanwhile, all was not lost for many companies that had glimmers of hope in 2020, and are hoping for a windfall in 2021, especially since recovery rates from the pandemic are rising and with the imminent availability of vaccines.

For Austria-headquartered Wittmann Group, which encompasses injection moulding machine maker Wittman Battenfeld and Wittmann (auxiliary equipment), 2021 could offer an increase in turnover, due to “good order backlog”, said Managing Director Michael Wittmann. However, he averred that there is “uncertainty behind any forecast because of the health situation”. The company’s turnover dropped by 17% to EUR310 million, compared to the previous year.
However, Wittmann relayed that the company’s order income for 2020 “has seen strong recovery in the second quarter with an incredible pick-up in business.” One of Wittmann Group’s latest offerings is the Ingrinder, an energy-efficient injection moulding system for recycling plastic waste, and which runs with coldrunner technology moulds. It consists of a sprue picker, granulator and vacuum conveyor and has been developed for the 110-tonne EcoPower machine and the 90-tonne SmartPower series.
According to Japanese machine manufacturer Sumitomo (SHI) Demag’s CEO Gerd Liebig, from January- August 2020 – during the active months of the downturn – its machine orders increased by 24% to EUR183 million, owing to the increased demand in medical technology, as well as in electronics, and packaging sectors.
The packaging industry has augmented orders for SHI’s all-electric machines, especially for applications with low and medium injection speeds, with its market share having significantly increased to 30%. Incoming orders and sales are also anticipated to ring up incomes to EUR275 million and EUR250 million, respectively, for the fiscal year 2020, Liebig said, adding that Europe accounted for 50% of all small and medium-sized machines.
Canadian tool maker StackTeck Systems, likewise, attested to demands for high volume injection moulds for medical applications this year. StackTeck offers solutions for medical-disposable items, labware, testing and diagnostic plastic components. Jordan Robertson, VP Business Development & Marketing, commented that enquiries poured in for high volume medical applications during the pandemic, but with challenging lead time requirements.
Read more...
(PRA) Subscribe to Get the Latest Updates from PRA Please click here
©2020 Plastics and Rubber Asia. All rights reserved.

©2020 Plastics and Rubber Asia. All rights reserved.
Home Terms & Conditions Privacy Policy Webmail Site Map About Us