Recycling: Topsoe joins Danish project to increase recycling by 20%; VTT spins out Olefy for extracting 70% components from waste
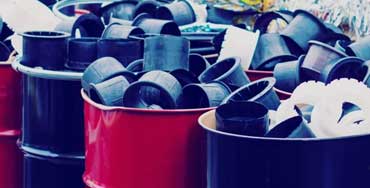
Today, many industrial products made of plastic are burnt or deposited after use because they either are not designed for recycling or because the available recycling technologies cannot handle the products. Several of the largest Danish companies prefer a change, and they would like recycling to increase by at least 20% before 2025.
Besides technology company Topsoe, the project partners comprise Coloplast, Novo Nordisk, Danfoss, BASF, Grundfos, and COOP. Danish Technological Institute has united the companies in a project called Circular Industrial Plastics.
The first step in the project will be to survey and investigate the plastic materials that are currently used in the companies and then create an infrastructure for further treatment and recovery.
At the completion of the project, the objective will be to demonstrate full-scale solutions for selected products within the categories of medical, technical, and consumer plastics, and to demonstrate the interaction of new recovery technologies in the circular flow.
Furthermore, the ambition is to give Danish companies access to new knowledge and technologies for establishing circular flows within plastics.
“The Circular Industrial Plastics project lays the foundation for a platform that matches materials and recovery technologies. This will give Danish companies easy access to co-operation and knowledge about specific solutions that can be implemented at once – but also to knowledge about innovation in the future. In brief, the project will be a catalyst for the transition from linear to circular production and use of plastics,” says Dr. Lars Haahr Jepsen from Danish Technological Institute.
The project is supported by the Danish Environmental Protection Agency and is a so-called flagship project where solutions will be tested and demonstrated in full-scale to inspire Danish trade and industry.
Participants in the Circular Industrial Plastics project
Plastics consuming industrial companies
Novo Nordisk A/S
Danfoss A/S
Coloplast A/S
Grundfos A/S
F&H A/S
Coop Danmark A/S
Reprocessing, infrastructure and recovery
Trebo ApS
Zirq Medical A/S
Makeen Power A/S
Crossbridge Energy A/S
Topsoe A/S
Marius Pedersen A/S
Geminor ApS
BASF A/S
Knowledge partners
Aarhus University
DTU, Technical University of Denmark
Danish Technological Institute (project manager)
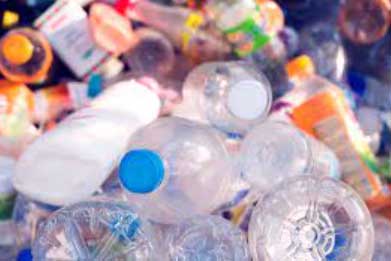
Meanwhile in other news, after four decades of thermal conversion technology development, Finland-based technology company VTT is spinning out Olefy Technologies, its patent-pending technology that can extract over 70% virgin grade plastics and chemical raw materials components from plastic waste, in October. VTT also announces eight patent applications for the process.
The Olefy process, which is based on gasification, breaks plastic waste into olefins and other valuable hydrocarbons. The working Olefy pilot is successfully running at VTT Bioruukki Pilot Centre in Espoo, Finland. The company is currently discussing partnerships and negotiating with investors for scaling, business development, and licensing of the technology. The first industrial demonstration operation is expected to be operational by 2026.
Today, only 8–10% of global plastics gets recycled primarily through mechanical recycling. However, only a limited share of plastic waste can be mechanically recycled. Furthermore, the resulting recycled plastic cannot be used in food packaging and pharma applications.
Most plastic waste ends up in landfills. The opportunity to get virgin quality plastic from previously unusable plastic waste means that with Olefy it is economically viable to recycle most of the world’s plastics with minimal sorting by consumers and businesses.
“Plastic waste is one of the five major global problems that VTT has strategically set itself to solve,” says Antti Vasara, CEO of VTT. “Olefy is a quantum leap in recycling that will change the way the world views plastic by making it truly circular and guiding us even faster towards carbon neutrality.”
A major advantage of the virgin quality materials produced from the Olefy process enables plastic to be recycled an infinite number of times.
“One of the problems with current recycling methods is that the quality degrades every time plastic is recycled. After several rounds of mechanical recycling, the quality becomes too poor, and the plastic is no longer usable and goes to a landfill. With the Olefy recycling process, the quality of the plastic is equal to virgin grade, so it can be recycled indefinitely and materials no longer need to end up in landfills,” says Matti Nieminen, Head of Technology at Olefy. “In essence, Olefy will make it possible for plastic to be a true part of the circular economy.”
Naphtha is a crude oil product normally needed for conventional plastic manufacturing. Olefy’s new technology eliminates the need for naphtha feedstock and is also able to produce enough energy for the process.
“The economic benefits of having virgin grade components from recycled materials can completely change the dynamic of global oil consumption. Olefy will significantly reduce the need to use new oil for making plastic and maybe even create a new economic incentive to clean up plastic from land and water as it becomes a valued commodity,” concludes Nieminen.
Major consumer product companies have set ambitious targets for incorporating recycled plastic into their products as well as packages – a typical goal being 25% of their total packaging by 2025. Around the world, demand for sustainable and recycled plastics is higher than ever. Essentially, with the Olefy process, it takes the same amount of ethylene or propylene based waste plastic as higher-cost naphtha feedstock to produce a ton of virgin grade plastic material.
At the same time, the process itself lowers the cost of production of recycled plastic so significantly that it can lower the bar for global companies to use it as a higher percentage of recycled material in their products and packaging.
“Demand for recycled plastics is growing much faster than the supply,” says Timo Sokka, Head of Business at Olefy. “All major brand owners are committed to fighting climate change, and they are responding to consumers' growing concerns on waste accumulation by utilizing recycled materials in their products. Olefy responds perfectly to these challenges by making plastics recycling truly feasible on an industrial scale.”
There are about 500 industrial steam cracker operations around the world. A steam cracker is a petrochemical plant that breaks down light hydrocarbons, such as ethane, propane, and light naphtha, to produce ethylene. Olefy’s new technologies economically open up a new world and value for plastic waste for these facilities.
“This technology enables direct parallel integration of the Olefy modules into existing steam cracker sites around the world to effectively produce virgin grade olefins, which are converted back to virgin grade plastics. Significantly lower capital expenditure requirements, accelerating market demand, and price premiums make these investments also very attractive for the steam cracker operators,” Sokka continues.
Olefy’s technology has been developed as part of VTT LaunchPad, a science-based incubator, where VTT researchers and technology are brought together with business expertise and investors to renew industries. VTT LaunchPad supports incubator teams to develop VTT-owned IPR into fundable spin-off companies.
(PRA)
Subscribe to Get the Latest Updates from PRA Please click here
©2022 Plastics and Rubber Asia. All rights reserved.
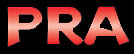
©2022 Plastics and Rubber Asia. All rights reserved.
Home Terms & Conditions Privacy Policy Webmail Site Map About Us