Davis-Standard’s new medical tubing extruder offers easier maintenance
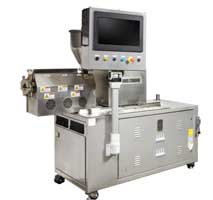
US extrusion machinery maker Davis-Standard has launched its upgraded MEDD extruder design for medical tubing applications. The sleek new design builds upon the first MEDD model to simplify extruder cleaning, maintenance, and operator accessibility. The MEDD is Davis-Standard’s signature extruder for tight-tolerance medical tubing applications, including microbore, multi-lumen and catheter tubing.
Operational advantages include a compact footprint, interchangeable barrel assembly, linear machine movement, a replaceable feed section liner, Windows® PLC control system, and the capacity to process a broad range of thermoplastic materials and high-temperature resins.
“The new MEDD design is essentially a more sophisticated version of our first model,” explained Kevin Dipollino, Senior Product Manager for Davis-Standard’s Pipe, Profile and Tubing business. “The electrical enclosure/machine base and cigar hood are now stainless steel to provide smoother surfaces for easier cleaning. In addition, we improved cable management throughout with specified cable lengths, cable storage, defined cable routing and an improved configuration. We also added access flip-down doors for easy access to simplify material draining and accessibility when changing the barrel.”
The ability to quickly change barrels for faster material change over or different diameter barrels is a significant benefit of the MEDD. This extruder design has a horizontal slide to easily move the motor and barrel section to mate to the customer downstream and a cantilevered feature at the front of the extruder for loading and unloading the barrel onto a cart during changeovers.
Additionally, the new model also has a bidirectional hood vent to improve air circulation. The MEDD is available in three product ranges, ¾-1 inch, 1-1.25 inches, and 1.25-1.5 inches.
In addition, Davis-Standard’s Technical Centre in Connecticut, which is equipped with the MEDD extruders, is also available for customers’ R&D needs. The company offers options for making parts for proof-of-concept, experimenting with new resins, conducting materials development, and testing equipment prior to making large capital investments.
The company adds that its engineering team is also able to customise feedscrew designs based on a customer’s process specifications.
(PRA)
Subscribe to Get the Latest Updates from PRA Please click here
©2021 Plastics and Rubber Asia. All rights reserved.
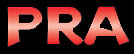
©2020 Plastics and Rubber Asia. All rights reserved.
Home Terms & Conditions Privacy Policy Webmail Site Map About Us