Plants: Sibur starts construction of massive Amur Gas complex; Duqm selects LyondellBasell’s PP/HDPE tech for Oman plant
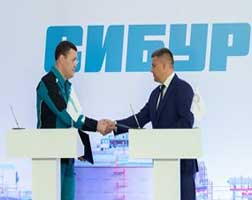
Russian petchem firm Sibur has started construction of its massive US$10 billion Amur Gas Complex, which is set to house the world’s largest steam cracker as well as downstream polymer production plants to be located in the Svobodny district of Amur region. The project is scheduled for completion in 2024 and commissioning in 2025.
The official ceremony was held online and was attended via video conference by Mikhail Mishustin, Prime Minister of the Russian Federation, relevant Ministers, Vasily Orlov, Governor of the Amur Region, Dmitry Konov, Chairman of the Management Board at Sibur Holding, and other representatives of government authorities, the company and its partners.
The Amur GCC project envisages construction of a basic polymer production facility with a total capacity of 2.7 million tonnes/year (2.3 million tonnes/year of PE and 400 kilotonnes/year of PP). The facility will feature a unique and the world’s largest cracking unit for the first-stage processing of incoming feedstock.
Amur GCC will be launched together with the gradual ramp-up of Gazprom’s Amur Gas Processing Plant to its full capacity. The polymer facility will receive ethylene and propylene from the cracker being built at the same site.
Completion of the project is set for 2024–2025 and is set to take the company’s overall capacity to 4.2 million million tonnes/year, following on from the recently completed ZapSib petrochemical complex in Russia’s Tobolsk region.
Sibur said the company will partner with Chinese petrochemical firm Sinopec in the Amur project, with the country being a target market for Amur GCC.
Most on-site preparations at Amur GCC have been undertaken with contracts for detail design and equipment and materials supplies for the facility’s key process units being fulfilled, said Sibur.
Sibur’s technology partners are Linde and NIPIgaspererabotka (cracking units), Univation Technologies and Chevron Phillips (ethylene polymerisation) and LyondellBasell (propylene polymerisation).
NIPIgaspererabotka will be responsible for project management, procurement and construction of off-site facilities.
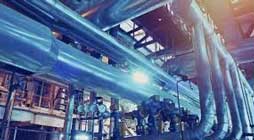
Meanwhile, in other news Duqm Refinery and Petrochemical Industries Company LLC (DRPIC)has selected polyolefin licensor LyondellBasell’s polypropylene (PP) and high-density polyethylene (HDPE) technologies for a new facility that will be built in Al Duqm, Oman.
The new plants will comprise of a 280 kilotonnes/year PP plant that will utilise LyondellBasell’s Spheripol PP process technology and a 480 kilotonnes/year HDPE plant that will utilise LyondellBasell’s Hostalen ACP process technology.
“LyondellBasell’s market leadership in polymer process technologies is once again confirmed with this significant award by DRPIC,” said Neil Nadalin, Director of Licensing at LyondellBasell. Nadalin added: “The selection by DRPIC of the Spheripol technology as the benchmark manufacturing platform for polypropylene resins and the Hostalen ACP technology as the leading low-pressure slurry process for the production of HDPE resins shows once again the confidence operators have in products produced with our technologies.”
“The Spheripol and Hostalen technology licenses forms part of 12 technology license packages awarded by DRPIC to international technology providers, advancing the FrontEnd Engineering and Design progress toward achieving shareholders’ Final Investment Decision in 2021. Due to the increasing global demand for petrochemical products, the DRPIC Petrochemical Project will become a significant player in the region, benefiting from its strategic location on the Oman eastern sea board with direct access to international markets. Working with long established technology licensors enables us to develop a world class project empowering the future development of downstream petrochemical industries in the Special Economic Zone of Duqm,” said Dr. Salim Al Huthaili, CEO of DRPIC.
Spheripol has more than 30 million tonnes of licensed capacity. The latest fifth generation Spheripol technology includes process improvements that further maximise operational efficiency.
The Hostalen ACP process technology manufactures high performance, multi-modal HDPE resins with an industry-leading stiffness/toughness balance, impact resistance, high stress cracking resistance and process advantages used in pressure pipe, film and blow moulding applications.
The DRPIC Spheripol plant will commence operations using Avant ZN catalyst. The Hostalen plant will commence operations using Avant Z501 and Avant Z509-1 catalysts to produce a full range of multi-modal HDPE products.
(PRA)
Subscribe to Get the Latest Updates from PRA Please click here
©2020 Plastics and Rubber Asia. All rights reserved.

©2020 Plastics and Rubber Asia. All rights reserved.
Home Terms & Conditions Privacy Policy Webmail Site Map About Us