Front Cover: TPEs find a niche in PPEs and pharma packaging
Given the rise of pandemics like Covid- 19, the role of Personal Protective Equipment (PPE) in protecting the healthcare workforce has never been more important. Meanwhile, with product shelflife being a priority in the development of packaging materials, TPEs are finding a niche in this sector, too.
TPEs on an upward trajectory
Packaging and personal protective equipment (PPE) share one thing in common: a judicious use of plastics. Plastics make for lightweight, flexible, and designversatile packaging, to name a few advantages. The efficiency of plastics for packaging makes it an economical and sustainable material solution. Likewise, these intrinsic properties of plastics make them also suited for PPEs.
However, not just any standard plastic types can fit the bill for medical use. Innovative materials such as thermoplastic elastomers (TPEs) respond to the functional issues related to PPE designs and medical packaging, owing to their versatility and durability.
TPEs continue to traction in the global supply chain, with a market that is projected to exceed US$19 million by 2022, according to a Grand View Research report. Thus, TPEs present advanced material benefits that make them a more suitable replacement for thermoplastics and standard elastomers.
TPEs: a strong suit for safer PPEs
PPEs provide protection against cross-infections and pathogenic transmissions and have the potential to block infections originating in blood, body fluids or respiratory secretions.
Global organisations, among which include the World Health Organisation (WHO) and the UNICEF (United Nations Children's Fund), cannot emphasise enough on the safety and effectivity of PPEs, including disposable surgical masks and gowns, face shields, goggles, glasses, and shoe covers. According to the UNICEF, PPEs both for medical use and those specified only to protect the user, must ensure the safety performance as well as quality, among other criteria.
The US Food and Drug Administration (FDA) has also laid out regulatory criteria for manufacturers to follow, which cover fluid resistance, leak protection, filtering capacity and tear resistance.
PPEs also have to be durable, comfortable to wear, and to provide adequate barrier against contact with body fluids and respiratory secretions; plus able to withstand the rigours of patient care for healthcare workers and medical front liners.
The advantages of mechanical properties coupled with biocompatibility, make TPEs well-suited for medical applications in parts sealing, strips, handles, and more.
Cross-contamination and viral transmission are also significant issues PPE makers have to contend, most especially during this current Covid-19 situation. At best, PPEs offer ample protection for users, acting as barrier against pathogens and contagious bugs.
As such, TPEs respond to the functional issues related to PPE designs, owing to their versatility and durability. For medical device applications, TPEs are sterilisable and offer advantages of mechanical properties as well as biocompatibility, making them well-suited in parts sealing, strips, handles, and more.
Medically fit compounds
KRAIBURG TPE, a global TPE manufacturer of a wide range of thermoplastic elastomer products and custom solutions for multiple industries, offers custommade TPE compounds, such as the THERMOLAST M materials for medical PPE applications.
Due to the use in of the compounds in a critical sector, KRAIBURG TPE says its THERMOLAST M TPE compounds are produced exclusively on a special medical unit.
The compounds also meet the requirements of the VDI 2017 guideline for medical-grade plastics (MGPs), issued by the Association of German Engineers (VDI), as well as the Reach and RoHS standards and Regulation (EU) No 10/2011, for use in medical applications. The US DMFlisted compounds also conform to US CFR 21 FDA (raw material conformity), and are certified to ISO 10993-10 (Intracutaneous irritation), ISO 10993-4 (Hemolysis), USP <88> (Biological Reactivity, Class VI), ISO10993-11 (Acute systemic toxicity) and ISO 10993-5 (Cytotoxicity).
In addition to the easy sterilisation properties, important features of the TPE compounds in THERMOLAST M are the elasticity and soft, flexible surface.
Targeted at the medical sector, the THERMOLAST M compounds are free of allergens such as latex, as well as avoid potential environmental pollutants such as PVC, phthalates, and BPA (bisphenol A).
Durability factor of compounds
The THERMOLAST M includes the MC/LF series that can be applied in breathing masks, goggles, sealing for face shields and handles of glasses to protect users against viral and bacterial contaminants.
Benefits of this series are the hardness level of 30-90 Shore A, low surface friction, abrasion and scratch resistance and the translucent colour. Furthermore, the MC/LF series of compounds can be easily processed through injection moulding and extrusion, with properties of adhesion to PP.
THERMOLAST M MC/LF series
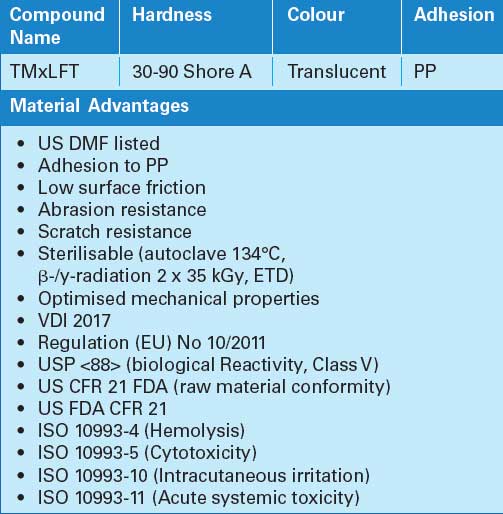
Meanwhile, the MC/AD/PA series in the THERMOLAST M TPE compounds are suitable for applications such as face shield head comfort pads and face mask seals that are used to protect users against infectious diseases.
Properties of the injection mouldable compound are the hardness level of 60-70 Shore A, and its adhesion with nylons, such as PA6 and PA12. Available in a natural colour, it is also easily colourable in effect colours, to allow for customisation in medical PPE applications.
Read more...
(PRA) Subscribe to Get the Latest Updates from PRA Please click here
©2020 Plastics and Rubber Asia. All rights reserved.

©2020 Plastics and Rubber Asia. All rights reserved.
Home Terms & Conditions Privacy Policy Webmail Site Map About Us