Thermoplastic Elastomers: Growing footprint of TPEs in key industries
From medical devices to sneakers, TPEs are redefining material innovation across industries, adds Angelica Buan in this report.
I f there is one advanced material that stands out for versatility, thermoplastic elastomers (TPEs) are hard to beat. Their ability to serve a wide range of industries makes them highly sought after, not to mention their role as a “canvas” for material innovation.
In the medical device industry, TPEs are valued for their flexibility, purity, and ability to replace latex and PVC. They’re also widely used in consumer goods for their soft-touch feel and colourability. Moreover, TPEs are found in athletic wear, sneaker soles, and shoe inserts, offering support and comfort. And with the growing focus on sustainability, TPEs tick that box, too.
Sustainable TPE with recycled content
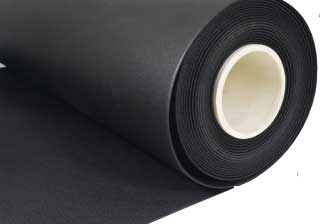
Recent developments highlight new solutions that incorporate recycled rubber and medical materials, reducing waste while maintaining durability and quality.
US clean technology company Prism Worldwide and Canadian thermoplastics extruder Sherwood Industries have partnered to integrate Prism’s sustainable TPEs into extruded rubber sheets, providing a high-performance, eco-friendly alternative for industries such as automotive, household products, and sporting goods.
Prism’s patented technology converts 100% of crumb rubber from end-of-life tyres (ELTs) into fully reusable thermoplastic rubber while retaining valuable polymers, additives, and carbon black.
Since April 2024, Sherwood has incorporated Prism’s ELT-based Ancora polymer into its production. Following successful test runs and positive customer feedback, Sherwood is moving forward with commercialisation and has invested in a new extruder for the ISO 9001:2015-certified sheets. Meanwhile, Prism’s recent US$40 million funding will further its efforts in sustainable materials development.
In the same manner, Taiwanese synthetic rubber materials manufacturer TSRC has developed Taipol recycled TPE (rTPE), a product line that blends performance with sustainability. Made from recycled medical materials, TSRC says it is able to transform reclaimed inputs into high-value, high-performance compounds. The product line includes variants containing 30% and 70% post-consumer recycled (PCR) resins, addressing the increasing demand for sustainable solutions across industries.
Compared to traditional materials like polyolefin elastomers (POEs), Taipol rTPE is said to offer improved impact resistance while using less material, resulting in cost savings and lower carbon emissions. Its pliable, flexible properties make it well-suited for soft compound formulations across a variety of applications. Additionally, it complements styrene ethylene butylene styrene (SEBS) by providing a more sustainable option with higher PCR content and reduced environmental impact.
Taipol rTPE is targeted at automotive components, consumer goods, and industrial products, including bumpers, electronics casings, wires, cables, and packaging materials. Certified under the Global Recycled Standard (GRS), it ensures full traceability throughout production and sales.
Safer and more efficient TPEs for medical uses
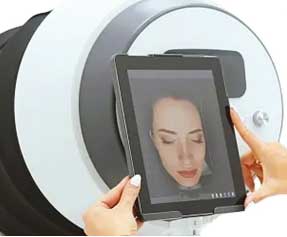
TPEs offer safer and more efficient alternatives to conventional materials in medical and healthcare applications. As leaders in this space, TSRC and Kraiburg TPE, a global manufacturer of TPE compounds, have introduced advanced TPE solutions designed to improve product performance, safety, and sustainability.
TSRC’s Vector medical solutions offer a range of TPEs tailored for the medical industry, featuring high, medium, and low molecular weights, along with high flowability and vinyl content. Rigorously tested for safety and reliability, Vector meets the ISO 10993-5 cytotoxicity standard.
As a plasticiser-free alternative to PVC, Vector TPE ensures environmental benefits as well as transparency in infusion bags, kink resistance in tubing, and resealing properties in medical stoppers, minimising fragmentation and contamination risks, it adds.
Meanwhile, Kraiburg TPE has introduced the Thermolast H HC/AD1/AP series for the Asia-Pacific market. Designed for healthcare and medical device applications, this TPE series is recommended for smart skin diagnostic device probe protectors, offering strong adhesion to substrates like PC, ABS, and PET while forming a durable seal that extends component longevity.
Fully colourable, it allows for customised designs that enhance user experience and brand recognition. Free from animal ingredients, it meets ethical standards, while its optimised mechanical properties ensure reduced maintenance needs. Its soft-touch surface improves control and precision during use, and its sterilisable nature allows for easy cleaning.
Compliant with GB/T 16886.5, ISO 10993-5, Regulation (EU) No. 10/2011, and US CFR 21 FDA (raw material conformity), Thermolast H HC/AD1/AP is ideal for flexible connectors in microneedling devices, films and seals for skin cleansing tools, handles for photon rejuvenation devices, and other medical and cosmetic applications.
(PRA)SUBSCRIBE to Get the Latest Updates from PRA Click Here»