Packaging: Smart, recyclable solutions for the packaging sector
The packaging industry is facing challenges, with consumers demanding sustainable solutions, while increasingly stringent regulations are being imposed. Thus, companies like ExxonMobil and Borealis are offering value-added solutions, to drive innovation in sustainable packaging solutions while addressing market needs.
UFlex and Borealis offer recycled materials for packaging
UFlex Ltd, India’s largest multinational flexible packaging company, says it the first Indian company to receive approval from the United States Food and Drug Administration (USFDA) for its recycling process. This approval allows UFlex to use recycled polyethylene (rPE) in food packaging, marking a major step in reducing plastic waste and supporting global brands in meeting their sustainability goals.
UFlex says its recycling process is categorised as super-clean recycling, with the ability to de-ink postconsumer recycled (PCR) materials by more than 95%.
Furthermore, to further strengthen its recycling infrastructure, UFlex is adds it is investing US$38 million in advanced recycling technologies. This includes the establishment of two new recycling plants at its Noida facility in India, with a combined capacity to process 39,600 tonnes/year of plastic waste. These plants will significantly boost the production of rPET and rPE materials for use in food packaging.
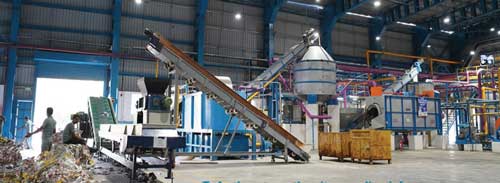
Additionally, the company has applied for US FDA certification to recycle polypropylene (PP).
At present, there are no specific guidelines for the use of rPE content in food packaging. However, there is a mandatory requirement under the Extended Producer Responsibility (EPR) regulations to incorporate recycled content in packaging. UFlex, in collaboration with industry players, adds it is actively engaging with government bodies such as FSSAI and BIS to help develop the necessary guidelines for the safe and sustainable use of rPE content in food packaging in India.
Currently, UFlex has recycling plants in India, Poland, Egypt, and Mexico, processing post-consumer multi-layered mixed plastic (MLP), multi-layer aseptic packaging (MLAP), and PET waste.
Meanwhile, Austrian materials firm Borealis has introduced Borcycle M CWT120CL, a recycled linear low density polyethylene grade (rLLDPE) for non-food flexible packaging. Produced with 85% PCR and 15% LLDPE booster, the flexible packaging grade is based on Borcycle M, Borealis’s mechanical recycling technology.
The new grade is tailored for blown film applications across primary, secondary, and tertiary packaging. Key applications include stretch film and stretch hood, and films for agricultural, industrial, and protective uses.
The new grade was developed together with Ecoplast, a member of the Borealis Group, in a project that began in late 2022. Its launch in January 2025 marks the culmination of more than two years of work to overcome the complexities of incorporating a high proportion of recycled content.
It adds that the result is a material with exceptional stretchability, achieved through low gel content, as well as an excellent toughness-stiffness balance. These properties make it an ideal solution for packaging manufacturers seeking to meet or exceed the requirements of the EU Packaging and Packaging Waste Regulation (PPWR) without compromising performance.
ExxonMobil, Kuraray, and Alico partner for PET and PVDC-free shrink bags for meat packaging
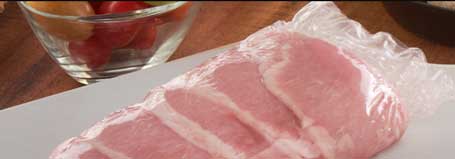
In a collaboration with materials manufacturer Kuraray, ExxonMobil Signature Polymers and Colombian packaging manufacturer Alico recently partnered to create a solution for local meat producers.
The firms developed Termoflex +B barrier shrink bags, utilising Exceed Tough+ m 0512, a Signature Polymers product, coupled with Kuraray’s EVAL's ethylene vinyl alcohol copolymer (EVOH) grades. The shrink bags were designed to address three key requirements: effective oxygen barrier properties, high shrinkage range, and optimal balance between mechanical and optical properties.
Manufactured in Colombia and now being implemented by local meat producers, the developed shrink bags are said to meet or exceed the performance of imported solutions, and eliminate the need for PET and PVdC while maintaining optimal barrier properties.
Furthermore, the bags achieve improved oxygen transmission rate at high humidity, compared to incumbent solutions.
The companies add that field trials prove the shrink bags’ ability to ensure comparable shelf life for fresh meats.
(PRA)SUBSCRIBE to Get the Latest Updates from PRA Click Here»