Emerging innovations, sustainable solutions leading the industry
Latest plastic innovations with bioplastics, biodegradables, carbon capture and PCR/PIR are driving sustainable plastics forward, according to Angelica Buan in this report.
Production of plastics has come a long way in reducing environmental impact. Advancements cover the entire lifecycle of plastics, from how they're made to how they're disposed of, focusing on producing fewer emissions, enhancing recyclability, and using renewable materials.
Still, scaling up sustainable plastics comes with challenges, including cost, efficiency, and technological limitations. Issues like production scalability, regulatory hurdles, cost reduction, and market acceptance remain key concerns.
Industry players are exploring new solutions to meet sustainability goals, while researchers continue developing technologies to make sustainable plastics a viable mainstream option.
Microorganisms reengineering biodegradable plastics
Biodegradable plastics break down through microbial activity, reducing waste and environmental impact. Derived from renewable resources, petrochemicals, or both, they offer a sustainable alternative to conventional plastics. Benefits include lower emissions, reduced landfill waste, and composting compatibility, making them useful in packaging, agriculture, and waste management.
Research continues to improve biodegradation efficiency and mechanical properties to rival traditional plastics, plus composting can also enhance soil health.
A study by the University of Connecticut (UConn) and bioplastics manufacturer Novamont found that Mater-Bi, a starch-based polymer, degraded by nearly 50% over nine months in a marine setting, exceeding traditional plastics. Published in the Journal of Polymers and the Environment, the study tested Mater-Bi compostable bags in seawater, excluding larger organisms that could interfere with results. The material lost 25% to 47% of its mass or area, with warmer temperatures accelerating the process
Led by researchers Hannah Collins, Larissa Tabb, and marine sciences professor Evan Ward, the study noted that biodegradable plastics like Mater-Bi could help reduce marine plastic pollution, particularly in aquaculture applications such as kelp farm lines and oyster grow-out bags. The collaboration with Novamont provided insights into real-world biodegradation beyond controlled lab settings, the researchers said.
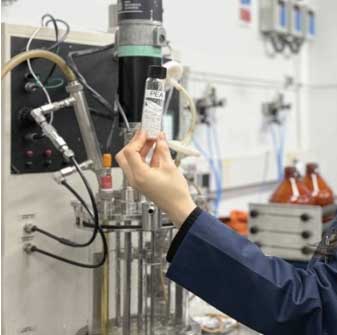
Beyond biodegradation, researchers are also exploring new ways to develop bioplastics from renewable sources. Scientists at the Korea Advanced Institute of Science & Technology (KAIST) have created a method to produce polyester amide, a next-generation bioplastic, using microorganisms instead of fossil fuels. Headed by Professor Lee Sang-yeop of KAIST’s biochemical engineering department, this breakthrough, published in Nature Chemical Biology, signifies the first successful microbial production of polyester amide.
Polyester amide, a durable plastic-nylon blend, is traditionally petroleum-based and polluting. The KAIST team engineered microbes to produce nine polyester amides from glucose, earth's most abundant biomass. Through an optimised fermentation process, they demonstrated the potential for large-scale production.
Testing by the Korea Chemical Research Institute confirmed that the resulting bioplastic has properties comparable to HDPE, making it a viable alternative to conventional plastics. Meanwhile, ongoing research is focusing on improving production efficiency for industrial uses.
Plastics from thin air: using carbon emissions as feedstock
Conventional petroleum-based plastics are making the industry a major contributor to greenhouse gas emissions. Currently, plastics account for about 8% of global oil consumption, a figure that could reach 20% by 2050 if current trends persist, according to the World Economic Forum.
Using carbon dioxide (CO2) as a feedstock offers a way to reduce this environmental impact by decreasing reliance on fossil fuels and lowering emissions.
Capturing CO2 from industrial sources or directly from the atmosphere and converting it into polymers presents a sustainable alternative for plastic production. Emerging technologies in this field could reinvent how plastics are made and used, supporting a circular economy.
Among several companies that have made a leap into carbon capture is Finland-based energy company Fortum Recycling & Waste, which says it has developed the world’s first biodegradable plastic made entirely from CO2 emissions.
Fortum’s Inga polyhydroxyalkanoate (PHA) material caters to applications including food packaging, electronics, and cosmetics. It is biodegradable across all tested environments; recyclable, and said to offer excellent barrier properties. Last year, Fortum produced the first sample of Inga, according to Tony Rehn, Head of the Inga development team.
Similarly, start-up ReSource Chemical Corp is developing a cost-effective way to produce plastics using renewable feedstocks like CO2 and agricultural waste.
Having raised US$15 million in funding from investors including Chevron Technology Ventures, Mitsubishi Gas Chemical Company, and angel investors Adam Winkel and Matt Berger, ReSource's innovation is based on 2,5-furandicarboxylic acid (FDCA), a molecule that serves as a building block for PEF, an alternative to PET resin.
PEF is said to offer superior strength, durability, and thermal performance while requiring less material. It also provides better oxygen, carbon dioxide, and moisture barriers, significantly extending product shelf life. Despite these advantages, traditional methods for producing FDCA have been too expensive to make PEF a viable alternative.
ReSource has developed a streamlined process that eliminates two-thirds of the complexity in conventional FDCA production. This advancement reduces costs and enables scalable manufacturing. The technology is based on CO2 chemistry pioneered by ReSource’s founding team at Stanford University.
Sustainability aside, FDCA-based plastics offer a major safety advantage. FDCA is naturally produced in the human body, making it an ideal substitute for toxic additives currently used in plastics. PEF and other FDCA-derived plastics biodegrade more easily, breaking down into their original building blocks much faster than common plastics.
ReSource will use the funding to build an FDCA pilot plant and expand its specialty chemicals, aiming to mainstream FDCA-based materials.
(PRA)SUBSCRIBE to Get the Latest Updates from PRA Click Here»