Additives extending the potential of materials
Innovative additives are helping industries like construction, electrical, and packaging meet rising demands for performance, durability, and sustainability by enhancing material properties like strength, heat resistance, and recyclability, adds Angelica Buan in this report.
Mightier materials with the right additives
The global plastic additives market is on the rise, with an estimated value of US$57.6 billion in 2025, forecast to reach US$69.9 billion by 2030, growing at a CAGR of 4.96%, according to Knowledge Sourcing Intelligence.
Demand for additives such as bio-stabilisers, antioxidants, and flame retardants are increasing as industries seek materials with improved performance. The packaging, automotive, and construction sectors are among key drivers of this growth. To stay competitive, market players are focusing on R&D, introducing advanced additives that enhance plastic properties while meeting regulatory and environmental standards.
Packing a punch with recyclability
Offering brand owners and converters a cost-effective way to extend the shelf life and recyclability of PET bottles, US firm Avient Corporation has launched ColorMatrix Amosorb 4020L, an oxygen scavenging additive.
The material, which meets direct food contact regulatory requirements, enhances shelf-life performance for packaging applications such as condiments, sauces, juices, and beverages, including certain alcoholic drinks. This non nylon-based additive is compatible with recycled PET (rPET), making it an option for brands looking to incorporate higher levels of recycled material (up to 100%) in their packaging.
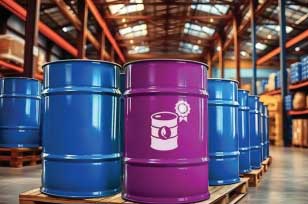
In a related effort, German specialty chemicals company Evonik’s Coating Additives business has launched a new co-binder, Tego Res 1100. This methacrylate copolymer enhances recyclate quality by making plastic film deinking processes faster and more efficient. It easily integrates into standard solvent borne ink formulations, offering broad solubility and compatibility with various binders and solvents, including alcohols and esters. Evonik says its testing shows that just 3-10% of the additive delivers deinking results, at temperatures as low as 40°C, with or without surfactants
Doubling down on sustainability while expanding its massbalanced additive portfolio, Evonik has also introduced Tego Wet 270 eCO, a substrate wetting agent with over 40% biocarbon, and Tego Foamex 812 eCO, a defoamer with over 60% bio-carbon.
Element of strength in construction materials
Construction materials need to be tough, durable, and built to last and that's where additives make a difference, while renewablecontent additives offer an extra advantage by enhancing sustainability.
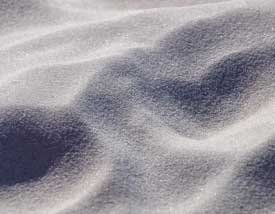
Additives supplier Baerlocher provides Baerophob hydrophobic agents, designed to improve the durability of building materials exposed to harsh weather conditions. These are mainly used in cementitious systems especially dry plasters, pasty plasters/paints, paving stones, and more. Plus, the products are compatible with building materials such as lime, cement, gypsum, and wood.
The Baerophob range is based on renewable raw materials; are silicone and paraffin-free and provide hydrophobic effects due to their dispersion in building materials. They also help decrease the frequency of renovations and associated costs, requiring only a low dosage for cost-efficient use, says the firm.
In line with sustainability, German chemicals company BASF and Swiss specialty chemicals company Sika have jointly developed a new amine building block for curing epoxy resins, now commercially available under BASF’s Baxxodur EC 151 brand. It is said to be ideal for flooring applications, such as in production plants, storage and assembly halls, and parking decks.
Baxxodur EC 151 provides epoxy resin flooring with low viscosity and optimal flow properties, making the coatings easy to apply and spread evenly. It requires significantly less thinner than conventional hardeners and reduces volatile organic compounds (VOCs) by up to 90%, plus allows for greater use of mineral fillers, lowering costs and contributing to sustainability, say the firms. Further, curing time is reduced by up to two-thirds, allowing for quick use after application.
As part of the research cooperation, Sika is applying the amine in Sikafloor coatings while BASF developed a suitable manufacturing process and scaled it up from the laboratory to production level.
(PRA)SUBSCRIBE to Get the Latest Updates from PRA Click Here»