Biomaterials: Kuraray develops biobased, highbarrier, recyclable granulate for paper coating
Kuraray, the global speciality chemicals company headquartered in Japan, has launched a new grade of its sustainable, high-performance barrier material named Plantic. As a plant-based granulate developed specifically for extrusion coating, Plantic EP can is suitable for the development of sustainable gas and aroma-barrier solutions for paper, cardboard and traditional film substrates. A recent certificate awarded by Western Michigan University (WMU) confirms that this new material is repulpable and recyclable. It can therefore be used as the basis for sustainable barrier pouch and carton formats for brand owners and converters. Plantic EP gives the market a high-barrier material that is fully recoverable and recyclable in the US paper stream.
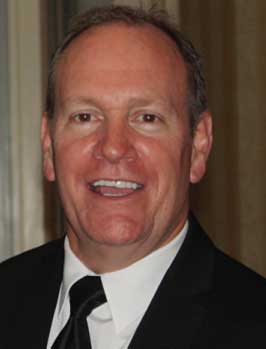
“Companies have recognised the importance of packaging that maintains product integrity and shelf life, while consumers don’t want to buy products that add to landfills,” says Tom Black of Kuraray’s Plantic unit. “We noticed a gap in the market and the need for a sustainable material that could be used to produce pouches and cartons with high barrier properties. It was clear that Plantic EP could be a game-changer. As well as complementing customers’ and retailers’ dynamic product ranges, Plantic EP helps them achieve their sustainability goals – thanks to certification from Western Michigan University that it is both repulpable and recyclable, enabling us all to leave behind a better world for our children.
Starch-based material with benefits
Plantic contains more than 80% corn starch, a renewable and fully biogradable raw material. Thanks to its high gas barrier properties, this highperformance film enables the development of sustainable multi-layer packaging that effectively keeps out oxygen and optimally preserves aromas. Therefore, Plantic can also in modified atmosphere packaging (MAP) for food with a longer shelf life, for example, for odour-free packaging of dry foods. In bags, trays, tubes and pouches, combined with paper or plastics, Plantic is said to be versatile and can be applied by extrusion coating, lamination or extrusion lamination
Since the Plantic layer simply dissolves in water, additional inner sealing layers can be separated cleanly from paper in the repulping process. That increases the yield of paper fibres, resulting in pulp without specks and impurities. The Plantic layer also dissolves during high-temperature washing in conventional PET recycling streams and decomposes into biomass, CO2 and water without any residues. Plantic biopolymer is certified for industrial and home composting. It is also produced without plasticisers and genetically modified raw materials and allows energy savings of up to 40% compared with conventional polymers.
Thus, it can significantly reduce the environmental impact compared with conventional packaging and enables re-use of materials that could not previously be recycled, according to Kuraray.
Recyclable, high-barrier properties
To develop a recyclable, high-barrier pouch, Kuraray applied Plantic EP to kraft paper using the extrusion coating process with a bonding/heat-sealing layer of polyethylene from Westlake. Flexible pouches and cartons with high barrier properties can be produced using Plantic EP in combination with multi-layer films. The additional structural layers can be separated, re-used and, where appropriate, recycled or composted.
“In this collaboration with Kuraray, we used all our application development resources to create a really unique offering,” says Amy Moore, Vice President of Westlake. “We see the benefits of Kuraray’s technology and look forward to working together on further developments as Kuraray commercialises the technology across the bandwidth of market segments and categories.”
Speciality chemicals expert Kuraray recognised brand owners’ the need for sustainability-certified packaging. Therefore, it asked WMU to assess the repulpability and recyclability of the Plantic EP/ Westlake pouch made from coated paper. Since it can be completely washed out in the recycling process, WMU certified the recyclability of the Plantic EP/ Westlake pouch in October 2022.
“WMU certification as confirmation of recyclability is an important first step in securing a How2Recycle label,” says Black. “When developing packaging formats for brand owners, producers want to see that the materials they are using have been vetted by WMU. Certification enables them to apply to How2Recycle for a pre-validation letter, which speeds up the introduction of Plantic EP-based high-barrier solutions.”
Plantic EP is currently available for testing and is already being used commercially by several brands around the world. Specific application scenarios include the production of pouches and cartons for products such as coffee, pet food, dry goods, and so on.
Kuraray adds that it is currently assessing the recyclability of this product in European recycling streams. Initial internal test results are now available and are promising.
"We see a great demand for materials that improve the sustainability profile of packaging," says Stefan Corbus, Market Development Engineer at Kuraray. "Food packaging is particularly demanding, because here ecological aspects must go hand in hand with functional properties - the sensitive food must be perfectly protected by its packaging. Many brand owners are already well on their way here, and with Plantic, Kuraray is making an important contribution to enabling our customers in the food industry to develop innovative packaging solutions."
Plantic Technologies Ltd. has been a part of Kuraray Group since 2015. Plantic is certified for renewable content, biodegradability in soil and water and compostability by independent international testing and certification companies in numerous countries, including TÜV Austria.
For further information please contact:
stefan.corbus@kuraray.com
Find out more on:
https://www.packaging.kuraray.eu/
(PRA)
Subscribe to Get the Latest Updates from PRA Please click here
©2023 Plastics and Rubber Asia. All rights reserved.
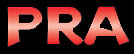
©2023 Plastics and Rubber Asia. All rights reserved.
Home Terms & Conditions Privacy Policy Webmail Site Map About Us