Recycling: Covestro’s chemical recycling of PU foam; Ineos Styrolution/Recycling Technologies/Trinseo to set up PS recycling plant in Europe
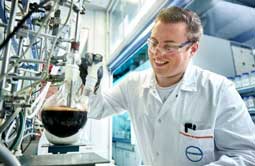
German materials firm Covestro says has developed a process for the chemical recycling of polyurethane (PU) flexible foam from used mattresses. It builds on its participation in the PUReSmart project, which is coordinated by Recticel company.
Each mattress contains on average 15-20 kg of foam. Covestro adds that its process is novel compared to other chemical recycling approaches, since it enables the recovery of both main PU components. In addition to the polyol, the primary product of the other component formed during recycling – the isocyanate – can now also be generated.
Since recently, Covestro has also been operating a pilot plant for flexible foam recycling, in order to verify the positive laboratory results achieved to date. With this project on the chemical recycling of PU mattress foam, the company has made significant progress toward the goal of a recycling loop.
"Our goal is to industrialise chemical recycling processes for post-consumer flexible foams in order to ultimately commercialise both raw materials derived from the recycling of mattress foam," explains Karin Clauberg, Venture Manager Flexible Foam Chemolysis at Covestro. "With our innovative technology we aim to deliver a high purity, high quality recycled polyol that fulfills customer specifications, and a recycled toluene diamine, or TDA, which is suitable for further processing to toluene diisocyanate. This isocyanate, or TDI for short, is used together with the polyol for the production of flexible foams."
Furthermore, in collaboration with the companies Recticel and Redwave – a division of Wolfgang Binder GmbH – and as part of the PUReSmart research project, Covestro has developed a sorting solution to separate the different PU foams from post-consumer mattresses. The software uses machine-learning algorithms for a proper recognition of the different types of foam, enabling clean material inputs for the subsequent recycling process. This development is a further component of the digitalisation strategy with the associated new opportunities for the entire chemical and plastic value chain.
The new pilot plant that Covestro has now commissioned is designed to expand recycling into an efficient industrial process. The aim is to validate laboratory results, optimise the process and develop products and applications on a small industrial scale.
The first phase is to focus on process development for polyol recycling, followed by the recovery of TDA as a precursor to TDI, scheduled to start this summer.
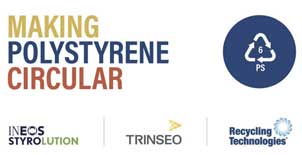
Meanwhile in other news, Ineos Styrolution, Recycling Technologies and Trinseo say they have reached a significant milestone in their plans to build commercial polystyrene (PS) recycling plants in Europe. Recycling Technologies has been selected as the technology partner.
Ineos Styrolution plans to build its full commercial scale recycling facility in Wingles, France. Trinseo announces its plan to build its own plant in Tessenderlo, Belgium, which is expected to be operational in 2023. Each plant would aim to convert 15 kilotonnes/year of PS waste into recycled styrene.
These three companies all share the same vision of making PS a circular material through depolymerisation. The unique properties of PS allow for full circularity where PS waste is returned to its chemical building blocks before being polymerised again. The recycled PS will have identical properties with virgin PS. Life cycle assessment calculations show significant decreases in greenhouse gas emissions when compared with PS production from naphtha.
Following a detailed assessment of technology options, UK-based Recycling Technologies was selected to join Ineos Styrolution and Trinseo as the technology provider for commercial scale recycling of PS. Recycling Technologies’ solution provided the highest yields in the conversion of PS to styrene monomer and provided the most scalable solution due to the company’s fluidised bed reactor combined with expertise of a highly skilled technical team.
Prior to building the commercial scale recycling plants, a PS recycling pilot plant will be built in the UK in 2022, and the technology will be further developed jointly by the three parties. The pilot plant will provide information and data related to chemical recycling and operations to support future development of the commercial scale recycling plants.
Sven Riechers, Vice President, Business Management, Standard Products EMEA at INEOS Styrolution, said, “Being the location of one of our polystyrene plants in Europe, Wingles is perfectly suited for our future recycling facility.”
Nicolas Joly, Vice President, Plastics & Feedstocks at Trinseo and President of Styrenics Circular Solutions, adds, “Polystyrene turns out to be a wonderful polymer. Not only is depolymerisation an effective recycling method, but it also allows for recycling while also maintaining food contact compliancy.”
Adrian Griffiths, CEO/Founder of Recycling Technologies Ltd., comments, “Our collaboration with Ineos Styrolution and Trinseo is a strong recognition of our technology’s ability to make polystyrene circular. We look forward to working with these two global leading companies to build Europe’s first chemical polystyrene recycling facility.”
(PRA)
Subscribe to Get the Latest Updates from PRA Please click here
©2021 Plastics and Rubber Asia. All rights reserved.
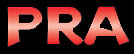
©2020 Plastics and Rubber Asia. All rights reserved.
Home Terms & Conditions Privacy Policy Webmail Site Map About Us