Green news: Borealis’s feasibility study to increase chemically recycled feedstock; BASF’s plasticisers for PVC based on renewable and chemically recycled feedstock
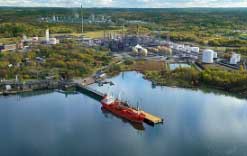
Austrian chemical firm Borealis, together with partner Stena Recycling, has commenced a new project to secure an increased supply of chemically recycled feedstock for the production of more circular base chemicals and polyolefin-based products. A feasibility study for a chemical recycling unit to be established at the Borealis production location in Stenungsund, Sweden, is now underway.
Funded in part by a grant awarded by the Swedish Energy Agency, and based on a successful feasibility study and final investment decision, operations are expected to begin in 2024. Borealis Stenungsund has been ISCC PLUS certified since February 2021.
Borealis will also co-operate independently with Fortum Recycling and Waste on a project involving the sourcing of plastic waste to the chemical recycling unit; Fortum will apply for public funding for a feasibility study to this end.
As a complement to mechanical recycling, chemical recycling has an important role to play in closing the material loop on plastics circularity. This is because plastic waste streams of lower quality can be recycled chemically into high-quality base chemicals (including olefins) and polyolefins. In fact, olefins produced from chemically recycled synthetic crude oil offer the same high quality as olefins produced from fossil fuel-based crude oil. This allows for the production of high-end polyolefin-based applications. These include healthcare and food packaging materials subject to stringent quality and safety regulations which cannot always be met by mechanically recycled materials.
Borealis’s Borcycle C is the driving force behind Borealis endeavours in chemical recycling. Along with Borcycle M – in which “M” stands for mechanical recycling – it forms the Borcycle portfolio of solutions for plastics circularity based on the technology suite Borcycle launched in 2019.
The chemical recycling feasibility study is being carried out with Stena Recycling. Stena will recover plastic waste and, after sorting to remove materials suitable for mechanical recycling, will deliver it to the new chemical recycling unit to be built by Borealis. Stena Recycling plans to invest in their own facilities to enable circular plastic solutions by producing feedstock of plastic waste to Borealis.
Fortum Recycling and Waste, a leading provider of recycling and waste management services in the Nordics, is also applying for public funding to carry out a feasibility study. The study would define the technical requirements for the pre-treatment of plastics, quality control, and the sourcing of suitable materials. It should also determine the necessary requirements for permitting and investments with the aim to produce feedstock from plastic waste to Borealis chemical recycling unit. This integration of waste management and processing directly into a steam cracker would be one of the first of its kind. Once operations commence as expected in 2024, Borealis would operate the unit.
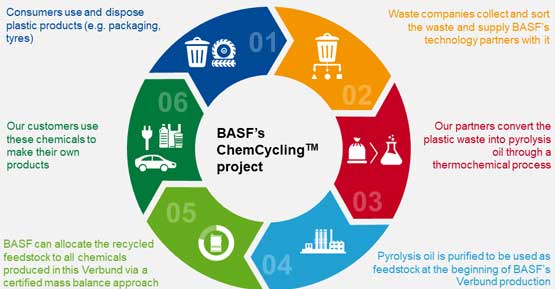
Meanwhile in other news, German chemical firm BASF says it now offers part of its plasticiser portfolio based on circular feedstocks. For this purpose, either renewable or chemically recycled feedstock is used at the beginning of the value chain instead of fossil resources. The alternative feedstock is allocated to the sales products according to a mass balance approach.
BASF has launched biomass balanced (BMB) plasticisers based on renewable raw materials under the names Hexamoll DINCH BMB, Palatinol N BMB, Palatinol 10-P BMB and Plastomoll DOA BMB. Instead of fossil resources, the required amount of bio-naphtha or biogas is used. These materials are derived from organic waste or vegetable oils. Biomass balanced plasticisers have a lower carbon footprint than the conventional ones and help save fossil resources.
With Hexamoll DINCH Ccycled, BASF additionally launched its trusted non-phthalate plasticiser based on chemically recycled feedstock. In the manufacturing process, BASF uses pyrolysis oil obtained from previously non-recycled plastic waste instead of fossil resources at the beginning of the value chain. The oil is supplied by partners as part of BASF’s ChemCycling project. The allocation to Ccycled sales products is also done by using a third-party certified mass balance approach. The resulting products contribute to the recycling of plastic waste.
BASF adds that for customers it does not take additional effort to either switch the production to the new plasticisers or to produce special editions. Thanks to the same specifications and technical properties as regular plasticisers, there is no need for additional sampling or release testing of the new plasticisers. Transportation and warehousing can also be done together with the regular products.
Plasticisers are used in many different applications, including films, insulation for cables and ducts, coatings, flooring, hoses and profiles. They are also an essential part of sensitive applications such as toys, medical products, sports and leisure equipment as well as food packaging. They give flexibility to PVC products and at the same time they offer protection against the effects of weathering and temperature, thereby helping to maintain the products’ functionality.
(PRA)
Subscribe to Get the Latest Updates from PRA Please click here
©2021 Plastics and Rubber Asia. All rights reserved.
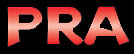
©2020 Plastics and Rubber Asia. All rights reserved.
Home Terms & Conditions Privacy Policy Webmail Site Map About Us