Green news: Steer’s compounding technology for rice resin in Japan; Maag’s melt pump technology for bioplastic PLA in China
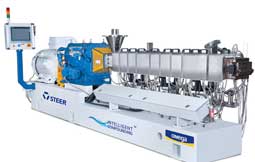
In a bid to push for environment-friendly alternatives to oil-based plastics India-based extruder firm Steer Engineering has announced that its patented technology is now being deployed for the development of biomass resin. It adds that it recently supplied three units of its Omega 60 class extruders to Biomass Resin Holdings in Japan.
The extruders help accelerate development and commercialisation of compound materials of inedible rice with polyolefin resins, called “Rice Resin”. Using these compound materials, products such as trash bags, shopping bags, cutlery (plastic utensils), and toys, can be manufactured for end customers. In the long term, these products significantly reduce plastic waste through environment-friendly polymer.
The Omega series extruders come with Steer’s patented ‘fractional lobe geometry’ special elements that are designed to enhance process efficiency and quality of output, while delivering returns on investment. It also enables manufacturers to increase their production capacity by up to 25% due to the increased volume and higher torque capacity, according to Steer.
Omega extruders with their special fractional lobe processor features, are said to revolutionise efficiency in handling difficult to process materials and many other applications that need lower residence time and/or tightening of residence time distribution.
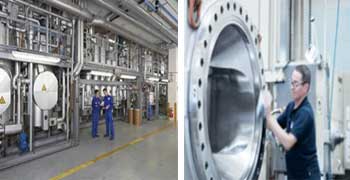
Meanwhile in other news, Swiss integrated machinery firm Maag Group says it has supplied its latest the art x6 class melt pump technology for the first fully integrated sugar-to-PLA (polylactic acid) plant in China. The plant is based on a Sulzer technology and key equipment for converting lactide into PLA. The lactic acid and lactide production is made from sugars (in this case won out of locally grown corn).
Maag says not only is the plant reducing the carbon footprint because of using plant-based resources instead of hydrocarbons, but by using its x6 class gear pump technology, the specific energy requirement is optimised furthermore.
MAAG Group’s pumps are used in the polymerisation reaction stage, making sure that the efficient Sulzer SMR reactors are working smoothly in all operating conditions. But they are also used in the devolatilisation stage, where, a minimum level is required when unreacted lactide is removed from the PLA melt to achieve a good product quality. In the last stage, Maag’s melt pumps are used to build up the necessary pressure to process the melt through the downstream equipment, up to the underwater pelletiser.
A key feature of the melt pump technology is the reduced back-flow to lower the energy consumption. The x6 class melt pump helps to save up to 50% energy and reduces material recirculation in the pump of about 50%.
While the reduction of 50% of energy is possible in exceptional cases and in extreme operating conditions only, the trend is true for all the applications when the x6 class technology is used.
The efficiency of the pumps is offering a wider operating range as compared to other technologies. It allows for example that low viscous pre-polymer can safely be processed through the Sulzer plug flow reactor when the polymer conversion is progressing and the viscosity is continuously increasing in the same.
It also keeps the bearing temperatures lower than in former pump technologies, allowing a stable film of polymer, lubricating the turning shaft. The favourable shaft geometry, where the length over centre distance ratio has increased, allows the operation of extraction pumps at a lower fill level than it was possible before at a given connection size to the vessel.
Only like this, can the PLA be fully concentrated, says Maag. But also, the reliability has increased. Not only are the bearing surfaces almost 30% bigger, providing a better cushioning, but the pump is also working with bigger gaps, allowing potentially small foreign particles entering the system to pass the pump easier without damaging it.
(PRA)
Subscribe to Get the Latest Updates from PRA Please click here
©2021 Plastics and Rubber Asia. All rights reserved.
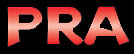
©2020 Plastics and Rubber Asia. All rights reserved.
Home Terms & Conditions Privacy Policy Webmail Site Map About Us