Plants: Polyplastics to expand COC output to Germany; Ineos Styrolution/Trinseo to set up PS recycling plant in France
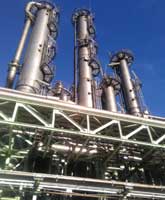
Japan-headquartered materials maker Polyplastics plans to construct a cyclic olefin copolymer (COC) production facility in Leuna, Germany, to meet the growing global demand for its Topas COC polymers. The new plant, to be operated by local Polyplastics subsidiary Topas Advanced Polymers, will have a capacity of 20,000 tonnes/year, more than doubling the company’s current output. The facility will be operational by mid-2023.
The company’s existing COC production plant is located in Oberhausen, Germany, about 400 km west of Leuna. Since the opening of the Oberhausen plant in 2000, a broad range of applications for COC has been developed. The material has become a crucial component in many medical devices based on its outstanding purity and glass-like properties, adds Polyplatics.
In packaging products, COC is said to have raised the performance of commodity polyolefins, enabling the development of simpler, better recyclable and sustainable solutions. Mono-material structures based on PE enhanced with Topas COC are more easily recyclable than multi-material solutions using layers of PET or other PE-incompatible polymers. Topas COC has been certified as a recyclable polyolefin as part of the EU initiative for a circular economy.
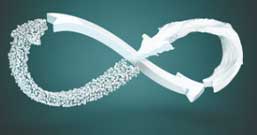
Meanwhile in other news, Ineos Styrolution and Trinseo, manufacturers of polystyrene (PS) and other styrenic materials, say they are advancing plans to build the first-of-its-kind PS recycling plant based on depolymerisation in Wingles in the north of France.[1] The planned full commercial scale recycling facility will be capable of processing up to 50 tonnes/day of post-consumer PS feedstock and is expected to be fully operational by mid-2023. Just recently, both firms also entered into an agreement with AmSty to jointly explore recycling options for PS.
In previous project milestones, the depolymerisation of PS has proven to be an ideal recycling process showcasing its unique intrinsic capability for full circularity. The plastics-to-plastics depolymerisation technology converts PS food packaging waste directly back into its original liquid monomer, which then can be repolymerised into recycled PS for the same high-quality end applications, including food contact applications much like virgin PS.
During the conceptual design phase two technology concepts from chemical recycler Agilyx and Recycling Technologies will be evaluated with regards to quality, efficiency and adaptation to different waste streams. Agilyx has evaluated the composition of the waste feedstock and successfully recycled it back into its original liquid monomer, using its proprietary depolymerisation technology. This project demonstrated PS’s unique intrinsic capability to be fully recycled.
“We are excited to move to the next phase of engineering of this plant, as we are well on track to deploy the game-changing depolymerisation technology with the construction of this recycling plant in France,” said Nicolas Joly, Vice President, Plastics & Feedstocks at Trinseo and President of Styrenics Circular Solutions. “This plant will be part of establishing a novel recycling infrastructure for styrenics in Europe together with key players from across the entire value chain, which will mark a step change in polystyrene recycling.”
Sven Riechers, Vice President, Business Management, Standard Products EMEA at INEOS Styrolution, said: “Our collaboration between Trinseo and Ineos Styrolution is a significant commitment of capital and resources and a major milestone in truly closing the loop with food grade recycled content. It forms part of Ineos Styrolution’s and Trinseo’s commitments to use, on average, 30% recycled content in products destined for polystyrene packaging in Europe by 2025.”
Both companies are founding members of Styrenics Circular Solutions (SCS), the value chain initiative to increase the circularity of styrenics.
(PRA)
Subscribe to Get the Latest Updates from PRA Please click here
©2020 Plastics and Rubber Asia. All rights reserved.

©2020 Plastics and Rubber Asia. All rights reserved.
Home Terms & Conditions Privacy Policy Webmail Site Map About Us