Solvay expands focus in aerospace; new composites facility in Germany
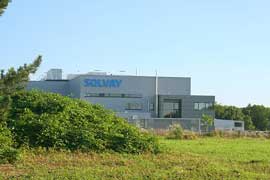
Belgian chemicals supplier Solvay is expanding its composite materials capacities with a facility and an upgraded site in Germany, to meet growing demand from aircraft customers for lightweighting materials and to provide products and services for parts like engine fan blades. This move follows its addition of a carbon fibre line at its US facility in August.
Located in Östringen, Solvay's latest site will produce and supply materials including for the LEAP engine produced by CFM International, the joint company between GE and Safran Aircraft Engines, for Airbus programs and Boeing.
It will produce its infusion resins and resins for reinforced composite materials from this facility, which is expected to come online in the second quarter of 2017 after customer qualifications. Resin infusion processing technologies are increasingly important in the manufacturing of composite parts as they meet demands from the aerospace industry for faster and higher volume processing of key parts.
In August, the company also opened a new carbon fibre production line at its US Piedmont Facility, South Carolina, doubling production capacity of a key raw material to make carbon fibre-reinforced composite materials and meeting increasing demand for lightweighting composite materials in the aerospace industry.
The new production line has won qualification by The Boeing Company to manufacture secondary structures such as wing movable flaps and engine nacelles, as well as interior applications.
The expansion covers the facilities and equipment to convert acrylonitrile monomers into standard modulus carbon fibres. This type of fibre is used to manufacture composite materials which have been pre-impregnated for use in applications on commercial and military planes.
Carbon fibre composite materials’ durability, strength and fatigue life allow them to increasingly and securely replace metals on aircraft, reducing their weight, noise and CO2 emissions. In addition, composites enable the moulding of multiple sub-components into one assembly part, lowering the number of parts required as well as the assembly costs.
(PRA)Copyright (c) 2016 www.plasticsandrubberasia.com. All rights reserved.