PRA Chinese
Rubber Journal Asia Injection Moulding Asia Energy, Oil & Gas Asia
VISIT OUR OTHER SITES:
PRA Chinese
Rubber Journal Asia
Injection Moulding Asia
Energy, Oil & Gas Asia
Plant Openings: PolyOne starts TPE line in India; Jilin COFCO Biomaterial commences first PLAneo PLA line in China
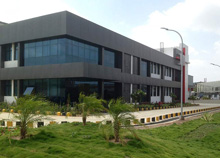
US compounder PolyOne has opened a new thermoplastic elastomer (TPE) production line at its Pune facility in India. In addition, the company opened a new Technology Centre that will house an advanced laboratory for new and existing R&D activities.
The highly automated and dedicated TPE line is the first of its kind in India, and is designed to manufacture GLS TPEs exclusively. Adding this line also increases PolyOne’s global footprint for consistent material formulations in all global regions.
Making these materials available locally rather than importing them will improve lead times and the ability to collaborate on custom formulations. Both the new TPE line and Technology Centre are staffed by dedicated and highly skilled associates.
“India is an emerging market with one of the fastest growing economies in the world,” said Holger Kronimus, Vice-President, Europe, at PolyOne. “We are committed to serving the needs of local and multinational manufacturers who operate here, and this recent expansion illustrates that commitment.”
PolyOne opened a new facility in Pune in 2014, initially focused on the production of colourant and additive concentrates to serve end markets such as transportation, electronics & electrical, healthcare, wire & cable, and packaging. The company expanded manufacturing capability to include specialty engineered materials last year. With the most recent addition of TPE production, PolyOne enables manufacturers to source all of their specialty polymer requirements from a single domestic source.
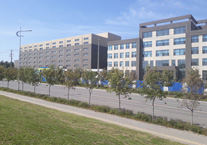
Meanwhile, in other news, the world’s first commercial plant based on the patented PLAneo polylactide (PLA) technology recently started production in Changchun, China. It is operated by the Jilin COFCO Biomaterial Corporation, a subsidiary of COFCO, China’s largest food and beverage group. The new plant produces all standard PLA types, among other things for the production of eco-friendly packaging, fibres, textiles and engineering plastics.
German company Thyssenkrupp developed the manufacturing process for the bioplastic PLA.
Sami Pelkonen, CEO of the Electrolysis & Polymers Technologies business unit of Thyssenkrupp Industrial Solution, expects the bioplastics market to continue to grow in the coming years, “not least due to the increasing environmental awareness of industry, governments and consumers,” he said. “With our PLAneo technology we want to do our bit to make the plastics sector more sustainable and resource-friendly. With it we enable our customers to produce high-quality bioplastics with a wide range of properties – at a price that is competitive with conventional plastics.”
PLA is a 100% bio-based and compostable plastic which thanks to its physical and mechanical properties can replace conventional oil-based polymers in many areas. The starting material for PLA production is lactic acid, which is recovered from renewable resources such as sugar, starch or cellulose.
PLAneo technology converts lactic acid into PLA in a particularly efficient and resource-friendly way. Another advantage is its transferability to large-scale plants with capacities of up to 100,000 tonnes/year.
In developing the technology, Thyssenkrupp’s subsidiary Uhde Inventa-Fischer profited from decades of expertise gained from the construction of more than 400 polymerisation plants and extensive experience in the scale-up of new technologies.
For the new plant in Changchun, Thyssenkrupp provided the engineering, key plant components and supervision of construction and commissioning.
(PRA)Subscribe to Get the Latest Updates from PRA Please click here
Copyright (c) 2018 www.plasticsandrubberasia.com. All rights reserved.