First nasal-only oxygen mask uses medical TPE
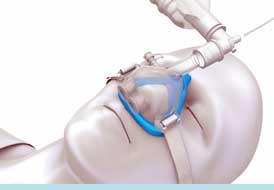
Relying on the sealing and cushioning capabilities of a thermoplastic elastomer (TPE), a small innovative company has addressed a longstanding problem in procedures involving sedation by creating the first nasal-only alternative to the standard full-face oxygenation and ventilation masks that medical practitioners have used for decades.
Unlike full-face masks, the patent-pending SuperNO2VA mask developed by Revolutionary Medical Devices (RMD) provides easy access to the oral cavity and is designed to deliver a greater flow of oxygen under positive pressure to the patient’s airways. The single-use mask consists of a transparent rigid PP component with access ports for an anesthesia circuit or hyperinflation bag, plus a TPE cushion that is over-molded onto the PP structure. The TPE cushion, moulded of Medalist MD-10105 medical elastomer from Teknor Apex Company, is said to play a critical role by providing a strong yet comfortable seal to the patient’s face.
The Medalist TPE is a gel-like 5 Shore A compound with sufficient “tack” and is designed to form a tight seal on the patient’s face.
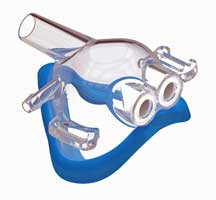
Use of sedation in medical procedures is increasing as a result of more sophisticated surgical techniques, an ageing population, and a greater incidence of obesity, according to Michael Pedro, MD, Chief Medical Officer and co-founder of RMD. “The SuperNO2 VA mask is an efficient and versatile alternative to full-face masks and nasal cannulae, and it is particularly advantageous for intra-oral procedures such as upper endoscopies and bronchoscopies. To optimise access to the oral cavity, we wanted a cushion that would present a lower profile than the traditional inflatable ‘balloon’ and provide a stronger seal. Teknor Apex’s low-durometer compound was a huge advantage.”
RMD uses the China-based contract moulding subsidiary of a US company to injection mould the components for the mask. The cushion part is produced in blue, green, pink, or yellow for purposes of colour-coding. Teknor Apex supplies the Medalist MD in pre-coloured compounds from a US plant and will supply identical grades from a plant in Singapore once it receives ISO-13485 certification, which is expected by December of this year.
“Over-moulding the Medalist TPE onto a PP substrate was challenging for two reasons,” said Chris Morehouse, market manager of regulated products for the TPE Division of Teknor Apex. “First, the lower the durometer of the TPE, the more difficult it is to make it adhere to PP. Second, the TPE part is complex, with thick- and thin-wall sections and recessed areas, or undercuts, that must retain their shape during ejection of the part from the mould.” Teknor Apex says it reformulated the TPE to attain the durometer required while still achieving a strong bond to the PP part.
The massive undercut at the nose section of the TPE cushion also calls for a compound with a high degree of strength and elongation, since typically an undercut with a material that soft would tear apart, “but the cushion came out of the mould with absolutely no problem”, according to RMD.
(PRA)Copyright (c) 2016 www.plasticsandrubberasia.com. All rights reserved.