K2016 presents an array of new technologies and machineries
Also, download this story from the electronic issue here
Materials
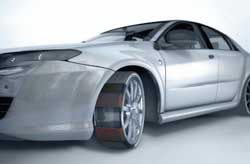
- Germany-based Lanxess will debut a new generation of Durethan PA6, BKV 30 XF (XtremeFlow), as a successor to Durethan DP BKV 30 XF. It is 30% glass fibre reinforced and is said to be more than 17% easier flowing, targeted at mounts and brackets in vehicles. Also new are three PA6 compounds reinforced with 30% glass fibres and microbeads: Durethan BG 30 X XF, BG 30 X H2.0 XF, and BG 30 X H3.0 XF. The H3.0 thermal stabilisation compound has a low copper and halide content and is customised for natural and lightly coloured applications in electrical/electronic parts such as plugs, plug connectors, and fuse boxes, while the H2.0 version is for black components that are subjected to higher heat loads.
Recycling Equipment
- Under the banner of Careperformance, Austria’s Erema will unveil its recycling 4.0 initiative at the K2016 show.
Building on the high level of automation of its Interema recycling technology, introduced at K2013, the company has developed what it calls a smart factory package for recyclers and producers. Careperformance will be shown live in action at an outdoor 480-sq m Recycling Centre, with an Intarema TVEplus 1108 integrated with Laserfilter, which will be recycling some of the plastic waste from the K show on site. The machine, quality and process data will be transferred in real time to Erema’s booth in Hall 9, Stand C05. The closed product loop, from production to reuse, will likewise be presented in live demonstrations.
And lastly, the Recycling Centre will feature an exhibition of products made with recycled material. It will open at 11 am on 19 October in the outdoor area (FG 09.1). Furthermore, re360 is linked to the Spare Parts Online, Erema's online webshop. Any upcoming maintenance work and the replacement of individual parts are displayed by re360 and spare parts can be ordered directly. The customers' respective Erema systems and previous orders are stored at Spare Parts Online. At the last K2013, Erema launched the Intarema system, based on Counter Current technology. It is said to provide process stability while maintaining flexibility with easy operation and less energy consumption. This stability enables automation processes such as Smart Start or the Recipe Management System, which in turn form the basis for Industry 4.0 applications. Since its launch in 2013, more than 450 Intarema systems have been sold worldwide.
- Italian manufacturer of recycling lines Gamma Meccanica has sold lines in the Turkish and Japanese markets. In Turkey, Gamma Meccanica supplied a GM125 Compac for recycling of PP and PE waste. It comprises a Compac feed with cutter-compactor, single-screw extruder with degassing, screenchanger and pelletiser. The Compac cutter compactor is controlled by the Ecotronic system to provide significant energy savings. Water is no longer used to control temperature. It also affords the possibility of recycling materials with high moisture content. An important feature is the presence of the feeding screw that allows for a steady controlled flow of material into the extruder, which has a degassing station with two ports to facilitate the escape of gases produced during the melting of the material. New extruder screw designs have been incorporated to increase the production outputs of the machines while the barrel is heated by optimum heaters for this type of application. The exterior casing has improved insulation with ceramic fibre to prevent heat loss and ensure increased energy efficiency. Compac’s feeding screw was fundamental in the customer’s choice, says Gamma Meccanica. “Comparing the laboratory tests on the quality of the granules produced and the hourly production of major Italian and qualified foreign manufacturers of recycling plants, the Gamma Meccanica line ensured the best quality recycled granules and especially a higher hourly production.
The line produces about 10% more than competitors' lines of the same size,” says the firm. In Japan, a GM90 Compac line for stretch and packaging film recycling has been delivered to one of the largest stretch film recycler. The screw and barrel of the extruder are designed to process LDPE, LLDPE and PP. “Also in this case, the comparison of the Gamma Meccanica line with competitors has shown a more constant hourly production; it works in a more automated mode and has a very low energy consumption,” said the firm.
Thermoforming
- Swiss machine maker WM Thermoforming Machines will debut the Twist700, designed to produce containers in PP, PP/EVOH, and PET that require high quality and narrow dimensional tolerances.
Extruders/Dies
- US-based Davis-Standard will exhibit a 90-mm extruder with a new frame, feedscrew design and quick screw exchange (QSE), for high temperature processes up to 300°C and speciality copolymer resins for film, coating, adhesion and moulding applications. The extruder frame is built with additional space to simplify maintenance and improve heater access. Upgrades include computer designed screws; electrical barrel heating with
air-cooled blowers for each zone; temperature controlled water cooling for gearbox oil cooler, water-cooled screw and feed section; and fixed die support and thermal expansion capability. The QSE adapter enables processors to easily change the screw without dismantling the melt pipes, feed block and other components. An extraction tool is included to manually change the breaker plate melt filtering inserts. The adapter is engineered with an
electrical pressure gauge, manual or motorised pressure spindle, double thermocouple for every heating zone, and breaker plate with two-screen pack.
- Davis-Standard is also one of only a few manufacturers worldwide to offer a high-speed extruder for demanding processes where rates and energy savings significantly impact profitability. Its 75-mm, 40D extruder offers processing versatility due to a favourable surface to volume ratio, compared to conventional extruders. The potential for improved processing is especially evident for high-speed sheet, fibre and extrusion coating processes, at outputs up to 1,500 kg/hour. It can be supplied with a direct drive AC motor or permanent magnet synchronous motor, offering energy savings of 10-15% when compared to traditional systems. Additionally, the screw speed and drive unit can be adjusted to accommodate different processing conditions.
- Germany’s Reifenhäuser will show its Evolution Ultra Die for barrier films, which combines benefits of stack dies and spiral mandrel designs to offer flow channels that are about 70% shorter than competitors. This allows processors to make quicker job changes for symmetric or asymmetric barrier structures. The die has a smaller diameter and is heated from both the inside and outside, which leads to shorter heat-up times for start-up of the line and change of raw materials.
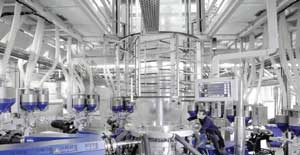
Film/Sheet/Cast Extrusion
- Germany’s Windmöller & Hölscher (W&H) is keeping under wraps its new innovations but says it will continue to focus on the concept of Packaging 4.0, “showing how intelligent machines, integrated processes and intuitive handling are already increasing efficiency and flexibility of the production.” The family-owned company will also have an open house at its 3,000 sq m technology centre at its headquarters in Lengerich. Innovations include a new generation cast film line and machine demonstrations for printing, converting and blown film.
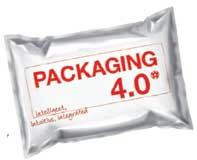
- Davis-Standard’s popular dsX systems for extrusion coating, cast film and blown film processes have had a positive industry response due to a competitive advantage in price, performance and delivery, says the firm. The 450 m/minute-dsX flex-pack (extrusion coating) provides converters and printers an adaptable configuration for a variety of emerging applications, including salted snack and noodle bags, toothpaste tubes, personal care products, condiment packs and stand-up pouches. The dsX s-tretch (cast film) is the first all-in-one system of its kind for in-line, pre-stretch cast film processing. Integrated technology eliminates the The dsX flex-film (blown film) is built to support applications like films for laminating and converting, bag making shrink film, hood shrink film, collation film, multi-unit packaging films, roll stock and surface print films. Unlike similar systems, processors can take advantage of upgrades that balance productivity against capital investment.
This includes multiple extruder packages and options for greater efficiency. need for traditional pre-stretching methods, resulting in thinner films, faster line speeds and improved film strength. Films as thin as 6 microns at speeds from 550-1,000 m/minute can be run in three, five and seven-layer configurations. As an added benefit, the dsX s-tretch has a narrow footprint for installation in tight spaces. It is also available with coreless winding to reduce waste.
- India’s Rajoo Engineers will be the only Asian company to demonstrate live its Pentafoil five-layer all-PE blown film line, in a throwback to K2013 where a five-layer barrier film line was running, to commemorate its 30th anniversary. This line incorporates advancements in technology such as cylindrical spiral die (CSD), internal bubble cooling, circumferential profile control with elevated air ring and triple lip, full automatic winder and touchscreen-based supervisory control panel. It is packaged in an affordable price, Rajoo says. With a maximum output of 650 kg/hour, the line can produce PE film in the thickness range of 30-250 microns.
Continue reading... here
(PRA)
Home | Terms & Conditions | Privacy Policy | Contact | Webmail | Site Map
Copyright (c) 2016 www.plasticsandrubberasia.com. All rights reserved.