Coperion to showcase new developments for high-accuracy feeding and conveying at K
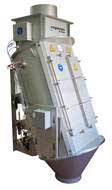
At K 2016, Coperion K-Tron will present a variety of new developments at stand B19 in hall 14. The new Electronic Pressure Compensation (EPC) system will be shown as well as a modified version of the Smart Flow Meter, which provides high accuracy feeding at high feed rates. The K-Vision line controller will also be on display.
The advantages of EPC system for their high-accuracy loss-in-weight feeders include improved accuracy and reliability as well as lower initial cost and easier installation compared to traditional mechanical pressure compensation systems. Coperion K-Tron has developed a clever but simple electronic solution for accurate and steady pressure compensation in feeder hoppers and outlets. The modular design incorporates pressure sensors and electronics tailored to interact smoothly with Coperion K-Tron’s KCM feeder control system. Retrofitting options for existing feeders are available. EPC can be installed on a majority of Coperion K-Tron gravimetric feeders in almost any application and all industries.
In a closed feeding system, pressure build-up inside a feeder can significantly impair weighing accuracy. The commonly installed mechanical pressure compensation systems are sensitive to structural factors and machine alignment and may therefore be intricate or even unreliable. Coperion K-Tron has now developed a clever but simple electronic solution for accurate and steady pressure compensation in feeder hoppers. The modular design incorporates pressure sensors and electronics tailored to interact smoothly with Coperion K-Tron’s KCM feeder control system.
Depending on set-up and requirements, sensors can be positioned on the feeder hopper and, if required, on the material discharge tube. The software implements a self-optimising compensation algorithm for best performance and dynamics identical to those of Coperion K-Tron’s SFT load cells, which allows for highly accurate feeding results, even in systems with perceivable pressure fluctuations. A separate field evaluation kit allows for the assessment of potential pressure issues in existing installations.
Meanwhile, in high rate applications, the Smart Flow Meter provides high accuracy feeding, at feed rates of up to 200,000 cu dm/hour (7,000 cu ft/hour). In addition to a lower purchase cost than a large loss-in-weight feeder, the Smart Flow Meter offers lower maintenance costs and reduced headroom.
The Smart Flow Meter is often employed in PE resin pelletising processes, where it accurately and gently feeds the main component, PE powder, into the pelletising extruder. Other areas of application include plastics, chemicals, animal feed, cement, coal, glass, aluminum, grain, etc. Typical particle size is approximately 0.02 mm up to 10 mm. The Smart Flow Meter is suitable for free-flowing bulk materials such as powders, granules, chips or fibres.
(PRA)Copyright (c) 2016 www.plasticsandrubberasia.com. All rights reserved.