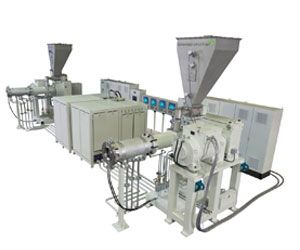
Bad Oeynhausen/Vienna-based Battenfeld-Cincinnati’s PWE 250 planetary roller for the production of EVA sheet for solar panels iis now making it possible to achieve an enormous outputs of up to 2 tonnes/hour. What gives this powerful machine the edge over other similar machine concepts is its “extremely gentle” treatment of the materials processed and as such, some 15 extrusion lines are already in operation worldwide.
Solar cells for photovoltaic modules are now regularly embedded in EVA sheet. The sheet, which must be electrically-insulating, highly transparent and tough, and UV-resistant, shield the silicon cells (which convert sunlight to electrical energy) against environmental damage such as corrosion or impact. . Each sq m of panel requires 500g of EVA per layer, i.e. a total of 1 kg.
About 90% of the growing energy market are now utilising the EVA sheet for its processing and long-term stability properties.
When producing the EVA sheet, plastic granulate must be plasticised gently at maximum 150° C and mixed with several additives. The planetary roller extruder is highly-capable for this process since it already achieves a highly effective dispersion and homogenisation performance at low processing temperatures.
The extruder consists of a conventional single screw as feed section; it also has a planetary gear section, which consists of a fixed roller cylinder with internal gear teeth, a teethed main spindle driven by a motor, and the revolving planetary spindles. All components of the planetary roller extruder are fitted with helical gears cut at an angle of 45°, with the teething of the planetary spindles being arranged at a counter-pitch to the other components.
The machine concept of planetary roller extruders is well known from calendar feeding in PVC processing, since here also, gentle plasticising at pre-defined low temperatures is a vital prerequisite.
Whilst single screw extruders of comparable size reach up to 800 kg/h and twin screw extruders up to 1,200 kg/h in output, the planetary roller extruder achieves a performance of up to 2,000 kg/hour, making it the optimal equipment for PVC processing as well as numerous alternative processes, such as EVA sheet production.
Apart from perfect transparency, optimal mechanical key values and low shrinkage are also important criteria for EVA sheet used in photovoltaic modules. Battenfeld-Cincinnati’s Multi-Touch roll stack meets these requirements to perfection. The concept consists of a two-roll stack for preliminary calibration and up to seven post-cooling rolls. This ensures even sheet tolerances, a uniform thickness profile, as well as optimal transparency, excellent flatness with only few orientations, and perfect mechanical properties.
(PRA)