Materials News: Budding market for bioplastics
Also, download this story from the electronic issue here
The biobased plastics market is expected to blossom into a million dollar industry with the plastics sector’s commitment to sustainability remaining a strong driving force behind its growth.
Humanity depends heavily on plants as a source of food, the catalyst of the air it breathes, and the backbone of its environment. Now, plants are being utilised as feedstock for plastics, for industries to manufacture products from renewable resources such as crops, biomass and algae.
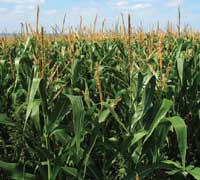
Biobased plastics or bioplastics, according to a report from BCC Research, rely on an estimated 0.01% of the global agricultural area of 5 billion ha. The UK research firm projects that bioplastics production could grow by 271% by 2020 from 2015, consuming some 0.04% of farm products produced from about 0.04% of total global agricultural area by 2020.
Another UK research firm, Smithers Rapra, pegs the global biopolymers consumption at 2.18 million tonnes this year, marked by varying growth rates due to availability of raw materials such as sugar cane, corn, and other useful crops, technology availability and policies favourable to bioplastics. By 2021, it says, global biopolymer demand is forecast to rise to about 6 million tonnes, growing at an annual rate of around 19%.
Demand for plant-based packaging
The global bioplastics market is driven by the emergence of renewable resources, biomass, and biobased raw materials such as starch and vegetable crop derivatives. In 2015, biobased bioplastics accounted for more than 80% of the global bioplastics market, in a number of applications such as packaging and domestic goods, thus weaning off overdependence on petroleum-based plastics.
According to Smithers Rapra, non-durable and semidurable applications of biopolymers occupy over 75% of the market. These applications are usually designed for one-time-use and usually they end up in a landfill. Biodegradable products degrade from naturally occurring microorganisms over a period of time. It is an important way to remove waste from the environment, breaking down organic matter into nutrients that can be used by other organisms. For this reason, biodegradability is considered to be the important application driver – a property that is well met by some biopolymers, especially PLA, PHA, PBS and a few other aliphatic polyesters and starch compounds.
Food and beverage are key drivers in the bioplastics packaging market, accounting for a CAGR of nearly 37% from 2014-2020, citing a research report by Persistence Market Research.
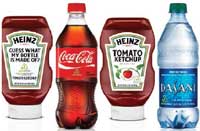
Major food companies, like Coca Cola, Danone, Heinz and Nestlé, have used plant-based packaging, thus further expanding the market potentials for bioplastics. These companies comprise the Bioplastic Feedstock Alliance (BFA), together with other consumer brand firms like Ford, Nike, Procter & Gamble, Unilever and World Wildlife Fund (WWF).
BFA supports the responsible development of plastics made from plant material, helping build a more sustainable future for the bioplastics industry. The primary focus of BFA is to guide the responsible selection and harvesting of feedstocks, such as sugar cane, corn, bulrush, and switchgrass, used to make plastics from agricultural materials. The group also addresses the potential impacts on land use, food security, and biodiversity.
Turning a new leaf with sugar-derived materials
This year, Dutch biobased industrial materials specialist Avantium and German chemicals group BASF established a mid-three-digit million Euro investment partnership to produce plant-based chemical furandicarboxylic acid (FDCA) utilising the plant’s fructose for making plastics. The joint venture named Synvina will also be marketing the new polymer polyethylenefuranoate (PEF) based on the new chemical building block FDCA.

The Amsterdam-headquartered joint venture is set for a production capacity of up to 50,000 tonnes/year at BASF’s site in Antwerp, Belgium, and to license the technology for industrial scale production.
FDCA is used for the production of PEF, a polyester with multiple application opportunities like packaging, engineering plastics, coatings, and fibres.
According to BASF, for packaging, PEF offers better characteristics, such as improved barrier properties for gases like carbon dioxide and oxygen, compared to conventional plastics, thus rendering a longer shelf life of packaged products. It also offers a higher mechanical strength, thus thinner PEF packaging can be produced and fewer resources are required. PEF is suitable for foil pouches, bottles for carbonated and non-carbonated soft drinks, water, dairy products, still and sports drinks and alcoholic beverages as well as personal and home care products.
FDCA can also be processed to polyamides for engineering plastics and fibres, to polyurethanes for foams, coatings and adhesives, and to esters for personal care products and lubricants.
Synvina is working with companies like Toyobo and Mitsui Chemical as well as those involved in the joint development platform for PEF bottles, including Austrian blow-moulded bottles specialist, Alpla, Coca Cola and Danone, to further the industrial potentials of FDCA.
Another key bioplastics producer, Netherlandsheadquartered Corbion, is steering its bioplastics market position along a sustainable curve. It recently published a white paper outlining the company’s stance on feedstock selection, as well as issues such as land use, feedstock efficiency and food security. Corbion says that the concerns of using biobased feedstocks for plastics can be successfully identified and managed, and that the many benefits of these biobased, renewable feedstocks far outweigh their challenges.
For the production of bioplastics like polylactic acid (PLA), Corbion’s key agricultural material is raw sugar from cane that is grown in Thailand. To a lesser extent, Corbion also uses sugar beet grown in Europe as a feedstock for its plant in Spain. Improving significantly its internal process yields, the company says it has been able to produce 1 kg of PLA using just 1.6 kg of raw sugar.
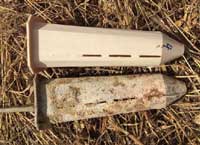
Likewise, part of this push for innovation strategies is introducing a new brand name, Luminy, which comprises the entire PLA range, including both high-heat and standard PLA resins, tailored to the most common plastics production technologies in various molecular weights, according to Corbion.
Furthermore, Corbion stressed in the whitebpaper the benefits of using biobased plastics in consumer goods. It says that biodegradable bioplastics can convert back to CO2, water and harmless substances at the end of their useful life. “This is a good option in case mechanical recycling of the end product is not (or no longer) feasible,” it adds. Equally notable is that the use of bioplastics curbs dependency on fossil fuels, therefore supporting a circular, local-for-local economy with the multiple end-of-life options provided.
Rooting for starch
Italy-headquartered bioplastics and biochemical maker Novamont Group has developed its own technology for producing hydroxymethylfurfural, furandicarboxylic acid and polymers for captive use, based on the roots of the cardoon plant, a close relative of artichoke.
“This is a complex system of integrated technologies with low environmental impact. The aim is to create a demonstration system and validate the product in certain initial applications from 2018,” according to Novamont.
The technology will enable the production of the
fifth generation of Mater-Bi bioplastic used in a variety
of applications such as carrier and organic waste bags;
nets for fresh fruit and vegetables; cutlery; and a range
of flexible packaging. Previous generations of Mater-Bi
include azelaic acid and pelargonic acid from oils (third
generation), and bio-butanediol from sugars using
bacteria (fourth generation).
Still on PLA, fibre-based materials manufacturer Ahlstrom is cornering the US single-serve coffee market with its PLA-based biopolymer for coffee pods.
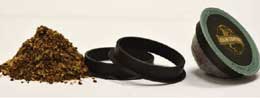
Ahlstrom has signed a multi-year agreement and will supply its biodegradable corn starch-derived PLA product to Canada-based roaster and packaged coffee products company Club Coffee. The biopolymer is combined with other natural fibres to obtain the pressure resistance properties needed for a good quality and filtering abilities to block residues from passing through. Club Coffee uses the material in its PurPod100 solution, which was recently cited with an "Innovation in Bioplastics” award by the Plastics Industry Trade Association (SPI) in the US.
Ahlstrom says its PLA-based materials can be also used in tea bags and other food packaging solutions.
Non-toxic solution
Algae, simple plants that live on water, are vital to the ecosystem. But instances like algae overgrowth, especially of the harmful algal blooms (HABs), can produce toxins. However, recent research findings offer solutions on how to constructively utilise algae.
US-headquartered non-prof it National Algae Association (NAA) is promoting the commercial value of algae oil as an alternative feedstock for the biofuels markets. It states that algae can be produced into high value products such as, to cite a few, cosmetics, food and bioplastics.
These benefits of algae are also confirmed by Dutch Wageningen University & Research (WUR), a collaboration between Wageningen University and the Wageningen Research foundation. It says that high-quality oils, proteins, pigments, hydrocarbons and sugars can be obtained from microalgae.
In an analysis conducted on two kinds of seaweeds, WUR researchers found that PLA obtained from Ulva Lactuca is suitable as a raw material for biobased soft drink bottles; and polysaccharides from Gracilaria Vermiculophylla, which can be used to make packaging film.
While the economic viability of seaweeds as material for bioplastics is still being established, the team’s analysis showed that seaweed cultivation has the potential to be eco-friendly. The team, led by Sander van den Burg of Wageningen Economic Research, reasons that “seaweed extracts nutrients directly from water and unlike the cultivation of maize or sugar beet, no polluting fertilisers are used. Seaweed also has the great advantage of not requiring valuable agricultural land.”
It is therefore not surprising that enterprising
individuals such as Rob Falken, Managing Director of
US-based companies Effekt and Bloom Holdings are
utilising a non-food renewable resource like algae for
fashioning marketable products like yoga mats and
sneakers. Working with algae bioproducts producer Algix
and its CEO Mike Van Drunen (who is also a Managing
Member of Bloom Holdings), Falken utilises the seaweed
collected from waste streams across US and Asia to
produce flexible algae foams, which contain around 15%
to 60% algae.
This innovation has the potential to produce other products. Expanding demand for algae could be more sustainable than conventional farming since they inhabit in water and do not require land for cultivation, experts say.
Growth on the horizon
Hence, the market for bioplastics is expected to continue to boom, and while the potential market for bioplastics is huge, consumption rates will depend on whether producers can grow their production capabilities fast enough and at acceptable cost/performance levels to meet demand. It is expected that the biopolymer sector will likely adapt an added-value business model. Unlike oil refineries, a biorefinery will be capable of processing many different types of biomass – including sugars, cellulose and various plant oils, says Smithers Rapra.
Other growth drivers will be legislation that will enable or impede producers in manufacturing biopolymers and converting them into useful consumer end-use items.
With the crude oil price being at its lowest since the year 2000, while this makes biopolymers less competitive against petropolymer equivalents; on the other hand, the unpredictability of oil prices encourage market players to look for alternatives that are made of raw materials that have a price that is easier to forecast.
Meanwhile, environmental issues will grow in importance and while new environmental regulations add additional costs to the industry, changing consumer views on sustainability open up new markets for biopolymer and recycled polymer markets.
(PRA)Copyright (c) 2016 www.plasticsandrubberasia.com. All rights reserved.