The American passion for red cups becomes a trend; WM supplies machinery
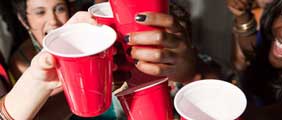
In marketing, the psychology of the colours used plays an important role in influencing consumers. A demographic research on colour demonstrates how important perceptions are, with colours being fundamental to visual codes. Individual colours can communicate precise feelings and have a psychological effect. For example, in a supermarket the colour connected to each sector is studied in every detail and customers have said that the colour of a product sometimes is the main element that influences their purchasing.
Red is a colour associated with fire and passion and can symbolise warmth as well, with different shades to denote the power of attraction, but also danger. It’s even a colour associated with the devil!
And red is the colour chosen for the iconic PP cup used by most Americans, which is the classic big-size disposable beverage holder anyone can remember in any US movie or TV series, half-filled with any sort of drink; crushed and thrown away.
The PP cup might seem only a simple object with little economical value, but it is actually a real piece of technology and engineering.
The PP cup design has been studied in every aspect to result in the perfect shape, so that it can be stacked easily and at the same time can be easily removed from the mould during the production.
The design takes into consideration the curved lip to avoid one cup from sinking too tightly to the next; the bottom being more rigid to allow more air flow between the stacked cups and also so that it doesn’t bend when it is filled.
Thus, Swiss maker of thermoforming machinery, WM Thermoforming Machines, has over the past year followed the American trend of the big size red PP cup.
It has to date delivered four In-line plants, two of them for the American market, where this type of production is “traditional”, the other two in Europe, where the big red cup is a new trend, says WM.
The machines delivered comprise the Intec FT 900/3, which
starts the process from the automatic dosing and feeding of the PP granules right on to the recycling of the scraps that are reduced to flakes and re-sent to the dosing unit at the end of the line.
The line is equipped with WM’s new extruder, N.EXT 75, which has a screw diameter of 75 mm and two co-extruders, N.EXT 45, with a diameter of 45 mm. The total extrusion capacity is 1,096 kg/hour.
The extruder also includes a flat die head that feeds a vertical laminating calender composed of three rolls, which produce a 930-mm width extruded sheet with a thickness ranging from 0.2 to 2 mm.
The sheet is then transported in line through a toothed chain system to the FT900 thermoforming machine, where the products take shape. The FT900, has a clamping force of 75,000 DaN, can use moulds with a maximum size of 880 x 520 mm and thanks to the tilting system of the movable platen is able to rotate up to 75 degrees, allowing for formed cups to be easily removed by the lower half mould.
The cups are formed and cut in-mould, removed with aspirating spindles and sent to a collection cage. The stacked cups are then sent by a conveyor belt to the rimming machine, with three rotating screws, which is also a WM production. The rimmed cups follow their way to the counting, packaging and boxing units ready to be delivered to the customer.
The advantages of the in-line system are reduced energy consumption, since it can produce 120,000 cups/hour, reducing waste and reducing the personnel necessary to manage the whole system.
WM designs in-line systems that can be used for many different production purposes, from PP cups to disposable plates made of co-extruded polystyrene as well as yoghurt, butter, margarine and ice cream containers, made of polypropylene, polystyrene or a multi-layer barrier.
(PRA)Copyright (c) 2017 www.plasticsandrubberasia.com. All rights reserved.