Plant set-ups: Trelleborg opens PU centre in UK; Evonik constructs PMMA facility for aircraft; BASF sets up R&D centre in India
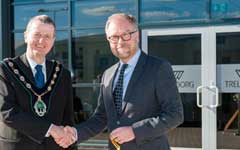
Swedish firm Trelleborg’s applied technologies operation inaugurated its new purpose built facility in Retford, England, further enhancing its polyurethane manufacturing capabilities. Ulf Berghult, Chief Financial Officer for Trelleborg Group, said: “By combining our local expertise from several Trelleborg facilities in the area into one, we will reduce our footprint and environmental impact on the local area. Our investment into this facility demonstrates our long-standing commitment to accelerating performance for our customers both locally and globally.”
The facility in Retford consolidates four sites; one in Retford, two in Coventry and one in Knaresborough, into a single facility. It combines the experience and expertise that has made these facilities successful to date, says the firm. Constructed using lean manufacturing principles and with a focus on environmental efficiency, the 7,225 sq m facility will manufacture the current product portfolio of Trelleborg’s applied technologies operation.
Meanwhile, Germany's Evonik marked the start of construction of a new stretching and polishing plant at the Weiterstadt
site with a groundbreaking ceremony recently. The Essen-based Group is investing a two-digit million Euro amount in the plant to become a complete provider of cast and stretched polymethyl methacrylate (PMMA) sheets for the aviation industry. It is the world's only producer of these extra-large format stretched PMMA sheets.
The new plant will be the most advanced of its kind in the world, says Evonik, for production of stretched aircraft materials made from Plexiglas. It is being constructed directly next to the existing production facility for the cast PMMA blocks that serve as the primary products for the stretching process. The plant allows production of stretched PMMA sheets that are more than twice as large as the currently available formats, yet satisfy the stringent standards (Mil-P-25690 and EN 4366) of the aviation industry.
Compared with cast PMMA materials, stretched PMMA sheets have higher impact strength and increased chemical resistance, says Evonik. The material is therefore especially well-suited to meet the extremely high requirements of the aviation industry. While registering attractive growth, the market for stretched aircraft materials is characterised by limited capacities on the part of suppliers.
The aviation industry is gaining a double benefit from the new format. For one thing, the new formats make production of aircraft and helicopter glazing more efficient. In addition, entirely new designs, such as particularly large cabin windows, are now possible.
This is Evonik's second investment in quick succession at the Weiterstadt site: The construction of a production plant for high-grade PMMA flat film was announced as recently as mid-February, with investment again in the two-digit million range.
In related news, Germany chemicals company BASF recently inaugurated its new Innovation Campus Asia Pacific, located
in Mumbai, India. The project will involve a total expected investment of up to EUR50 million, and marks the Group’s largest R&D investment in South Asia. All global research operations at BASF Innovation Campus Asia Pacific (Mumbai) will be housed under BASF Chemicals India Private Limited, a 100% subsidiary of BASF SE. The new innovation campus will expand the company’s existing R&D activities in India to include global and regional research on a wide range of speciality chemicals. Topics will cover personal and home care, process development, organic synthesis, crop protection and many more.
The Innovation Campus significantly expands BASF’s research capacities in India, which were established in 2005 and expanded in 2014 to cover agricultural research, organic synthesis, molecular modelling and advanced process research. The new Innovation Campus includes laboratories for chemical synthesis, application and process development, as well as analytics.
“We see the demand for innovative solutions in many industries in India, including automotive as well as food and nutrition. Moreover, India is now home to a wide range of high calibre scientists and excellent domestic research capabilities,” said Sanjeev Gandhi, Member of the Board of Executive Directors, BASF SE, responsible for Asia Pacific. BASF has expanded its presence in India during the past several years, both in terms of local manufacturing as well as in providing tailored solutions for the challenges of mobility, housing, environmental protection and hygiene. Through its local subsidiaries, namely BASF India Limited, BASF Chemicals India Private Limited and BASF Catalysts India Private Limited, BASF Group has invested actively in India to realise these opportunities, with approximately EUR300 million investment over the past four years in manufacturing and R&D.
The approximately 20,000 sq-m campus is a collaborative space housing scientific and technical laboratories, modern offices, a full-scale auditorium, cafeteria and employee amenities.
In 2016, BASF Group’s research pipeline encompassed around 3,000 projects, and spending on research and development was EUR1.863 billion. Around 10,000 employees work in R&D worldwide.
(PRA)Copyright (c) 2017 www.plasticsandrubberasia.com. All rights reserved.