Recycling: A synergy of de-cluttering solutions
Also, download this story from the electronic issue here
The combined efficiency of technologies and human efforts are key to creating a zero-waste living, says Angelica Buan in this report.
Currently, waste is being generated at unabated levels. The World Bank reports that the world's cities are currently producing some 1.3 billion tonnes/year of municipal solid waste (MSW), or 1.2 kg per city-dweller/day. By 2025, the volume is projected to swell to 2.2 billion tonnes, or 1.4 kg/person.
World Bank projects that lower income countries may incur five times more the cost of solid waste management than more affluent countries. By 2025, the latter countries will incur waste management costs of more than US$375 billion.
Meanwhile, achieving desired recycling rates are easier said than done. The US, for example, generates about 258 million tonnes or about 2 kg person/day of MSW; with 75% of this considered as recyclable. However, the US’s recycling rate was roughly 34%, according to the US Environment Protection Agency (EPA).
The industry is likewise going through decline, according to Recycle Across America (RAA), a US-based 501 non-profit organisation that has introduced society-wide standardised labels on recycling bins. It cites several reasons for what it calls as the “collapse of recycling”, including high contamination levels in the recycling stream.
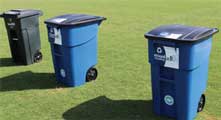
“Contamination cripples the economics of recycling, as the process to remove contamination reduces profitability, driving up the cost of recyclables, thereby preventing many manufacturers from reusing recycled materials. As a result, they continue to deplete finite natural resources at alarming levels,” states RAA.
Comparatively, the European Union (EU) has demonstrated a recycling rate of 44% during 2014. According to the European Environment Agency (EEA), 475 kg/person MSW was generated (or about 1.3 kg of MSW daily). By 2030, EEA targets a recycling rate of 65%.
In Asia-Pacific’s more affluent countries, recycling rates vary yet are impressive. US-based organisation Planetaid cites that in 2015 South Korea’s recycling rate was 49%; Japan, 21%; Taiwan, 60%; Singapore 59%; and Australia 30%.
Waste pickers, hands-on in waste collection
Meanwhile, quite a number of dwellers in developing countries with informal recycling sectors are making a livelihood out of picking waste for recycling.
According to a document titled Informal recycling sector in developing countries, from the World Bank’s Public-Private Partnership in Infrastructure Resource Centre (PPPIRC), about 1% of the urban population or 15 million people from developing countries make a living “salvaging recyclables from waste”.
Various initiatives to improve the earnings and living conditions of waste pickers are being hatched.
Brazil is piloting an initiative to include waste pickers into the MSW systems via cooperatives, as well as taking up a national solid waste policy that recognises waste picking or castadores in the native parlance, as an occupation in the 2001 Brazilian Classification of Occupations. Succeeding laws also allow municipalities to contract waste picking organisations, without the bidding process, to provide selective waste collection services.
Waste picking groups worldwide, in Latin America, South Africa, Asia Pacific, Eastern Europe and other regions, are also being recognised by their national policy-makers.
Opportunities that would benefit waste pickers continue to open up. An Amsterdam-based group, Reflow, has pitched a recycling initiative of using collected wastes, specifically PET bottles, as 3D printing material. The group explained that initially working with PET bottles enables easier sourcing of materials. At the same time, PET’s chemical composition is more standardised globally than other plastic types like ABS, which may contain recycling contaminants.
For a project based in Dar es Salaam, Tanzania, Reflow
hires waste pickers to collect PET bottles discarded by the
curbside or from designated locations like restaurants, bars
and hotels; and to bring them to its facilities.
At the same time, Reflow encourages a sustainable recycling system by producing the filament also in the source country, as well as ploughing 25% of their profits back into waste picker communities.
For Mexico’s waste pickers also known as pepenadores, global firm Danone’s water brand in Mexico, Bonafont, co-created a project with local partners Ashoka, a global social entrepreneurs association, and a non-governmental organisation, Mundo Sustentable, to help waste-pickers pick PET bottles from landfills of Mexicali city. This is recycled to rPET and, thus, Bonafont is able to secure its supply of rPET material. It is the first Danone company to have achieved a 100% rPET bottle.
With the EUR100 million-Danone Ecosystem Fund, the company is able to make its Mexican value chain more sustainable and efficient. The project also created a new Segregation Centre that also provides life skills training for pepenadores so they recycle better, which means better earning than their average US$219 a month.
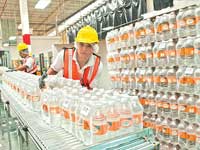
Moreover, Danone adds: “Because the r-PET circulates in a closed loop, its price is much easier to control, meaning a steady income for the waste pickers. Bonafont’s productivity has increased, too, because of the good-quality rPET it receives, and the model has proven replicable, which means that the benefits can be scaled up.”
In like manner, Danone has teamed up with Philadelphia-headquartered Nestlé Waters, and California-based startup, Origin Materials to form the NaturALL Bottle Alliance. The partners will develop and launch at commercial scale a PET plastic bottle made from 100% biobased materials.
The project uses biomass feedstocks, such as previously used cardboard, sawdust and wood chips, and later on other biomaterials , such as rice hulls, straw and agricultural residue. Danone and Nestlé Waters are providing expertise and teams, as well as funding to help Origin Materials make this technology available to the entire food and beverage industry. According to the alliance’s press statement, this next-generation PET will be as light in weight, transparent, recyclable and protective of the product as today’s PET, while being better for the planet.
Origin Materials has already made samples of 80 % biobased PET in its pilot plant in Sacramento. Construction of a pioneer plant will begin this year, with production of the first samples of more than 60% bio-based PET to start in 2018. The initial volume goal for this first step is to bring 5,000 metric tonnes of biobased PET to the market. Meanwhile, the NaturALL Bottle Alliance aims to develop the process for producing at least 75% biobased PET plastic bottles at commercial scale as early as in 2020, scaling up to 95% in 2022. Moreover, the team said continuous research will be undertaken to increase the level of bio-based content to 100%.
Zero waste community, a reality
For Japan’s fifth smallest community, Kamikatsu, waste management takes the form of manual sorting and mindful waste disposal. The rural mountain town has a small ageing population, which was less than 2,000 in 2015 and is expected to shrink further by 66% in 5 years.
Nevertheless, the 109.6 sq km-land town has been hailed as a model for zero-waste living. Akira Sakano heads the Zero Waste model and is Chair of the Zero Waste Academy, Japan, a non-profit organisation for Zero Waste policy implementation and advocacy; and co-founder of RDND, an enterprise delivering community development services in Kamikatsu.
The Zero Waste model as defined in the context of the Kamikatsu community is a sustainable, waste-free lifestyle, with waste management not requiring incineration or landfills. Kamikatsu, which used to dispose of waste by burning or dumping it on farms, now implements 34 steps or categories to separate, recycle or reduce waste. These include from proper segregation and recycling of household items and packaging, such as aluminium/steel cans, glass/PET bottles and paper packaging, to reduction of use and reuse of personal items.
Kamikatsu’s residents take their trash to a collection
facility and sort the trash themselves according to the
categories. The centre has bins for each of the categories,
correspondingly labelled with recycling information. Meanwhile, the Zero Waste Academy also manages the
town’s “kuru-kuru” shop where residents can drop off
their used items or pick up used items for free. Some local
residents also undertake upcycling of items, like bags and
clothes, in a “kuru-kuru” factory.
With three more years to 2020, the community is anticipated to clinch its zero-waste goal with collective efforts to responsibly manage its wastes.
Recycling technologies remedy sorting challenges
Recycling has become a widely adopted waste management activity in various countries worldwide. Efficient recycling begins with proper sorting of waste.
Brussels-headquartered Bureau of International Recycling (BIR) reports that there are an estimated 1.6 million people worldwide who are active in the recycling industry and who manage more than 600 million tonnes/ year of recyclable wastes.
For recycling plastics, which makes up about 12% of the total global waste stream, the 760-country member association finds sorting a challenge. Fortunately, technologies are being developed to break the limitations on sorting. Colour-swaddled packaging can be visually pleasing but can add up to the work of sorting in recycling facilities.
A US-headquartered firm, National Recovery
Technologies (NRT), is promoting a system to sort
coloured waste. Its ColorPlus-R uses an image processing
system to detect materials based on colour analysis and
object recognition. Unique to ColorPlus-R is the ability to
colour-analyse opaque objects, such as black plastics.
NRT stated that all ColorPlus models employ transmissive detection, placing the material between the light source and the detection camera. It provides the strongest signal strength and accuracy. In addition, the ColorPlus-R has added a second LED light source above the material to facilitate reflective detection. Whereas, opaque materials before were only recognised as objects, the ColorPlus-R’s simultaneous use of reflective and transmissive detection enables colour analysis.
Likewise, zeroing in on sorting problematic black
plastics are researchers at the Fraunhofer Institutes for
High Frequency Physics and Radar Techniques FHR in
Wachtberg, for Optronics, System Technologies and
Image Exploitation IOSB in Karlsruhe, and for Intelligent Analysis and Information Systems IAIS in Sankt
Augustin. The researchers have developed a sorting
system called blackValue that is capable of picking up
every plastic colour, including black, both in real time
and in large quantities.
Fraunhofer says its system has a terahertz line scan camera that enables the sorting of coloured and black plastics according to type. With this technology, black plastics are no longer off-limits to recycling streams. A wide array of ebony-coloured plastic items such as car consoles and laptop casings can now be recycled on an industrial scale, according to the researchers. The radar camera is available to recycling centres and offered commercially this year.
Extending the value of PET
It is no doubt that PET packaging is a common packaging type for food and beverages. Opaque PET (with a white exterior and grey interior) is specifically favoured over HDPE as the former weighs 25% lighter and also eliminates the use of aluminium metal seals on bottle caps, thus providing material savings for manufacturers.
Opaque PET, however, has a downside as it is not recyclable by conventional processes and thus, recyclers are rejecting it from their recycling systems, according to Carbios, a French green chemistry company.
To remedy this challenge, Carbios, which also specialises in enzymatic bioprocesses applied to plastic and textile polymers, has introduced a technology that allows PET packaging to be 100% recyclable.
Since 2012, Carbios has undertaken extensive R&D of an enzymatic recycling process for PET. The work has demonstrated 100% depolymerisation of PET-based commercial products to original monomers: terephthalic acid (TPA) and monoethylene glycol (MEG). Carbios says its proprietary technology enables the recycling of all PET products (transparent, multi-layer, opaque and complex), including opaque PET milk bottles.
Meanwhile, to combat the odour that comes from recyclate of packaging waste, Austrian recycling equipment maker Erema introduced its ReFresher equipment at the K2016 show last year.
The ReFresher eliminates odours caused by
migrated substances, i.e. residues that include food
particles, cleaners/detergents and cosmetics. It is placed
downstream of the extrusion process and keeps the
recyclates at the required temperature at which volatile
materials can be discharged. The equipment is available
in various expansion stages depending on the end
application. While the firm’s Intarema TVEplus prevents
unpleasant odours from developing in the course of
the extrusion process, the odours caused by migrated
substances are more difficult to contain. Erema now says
its customers will have access to a mobile unit for tests to
enable them to carry out on-site trials and evaluate results.
Another equipment for recycling PET comes from
Austria’s Next Generation Recyclingmaschinen (NGR)
and Germany’s Kuhne that have teamed up to offer
a solution for producing virgin material-quality foodgrade
PET sheets. The integrated system consists of a
shredder-feeder-extruder combination for producing
plastic melt; the P:REACT unit from NGR for improving
the quality of PET and the extrusion line from Kuhne for
producing PET sheets. Both PET sheet producers and
thermoformed part manufacturers will benefit from the
result, the tandem said.
On a final note, recycling is integral to economic growth and to ensure successful recycling outcomes, it requires peoples’ conscientious waste management and technologies.
(PRA)Copyright (c) 2017 www.plasticsandrubberasia.com. All rights reserved.