PRA Chinese
Rubber Journal Asia Injection Moulding Asia Energy, Oil & Gas Asia
VISIT OUR OTHER SITES:
PRA Chinese
Rubber Journal Asia
Injection Moulding Asia
Energy, Oil & Gas Asia
Food fills the appetite of biobased solutions
Also, download this story from the electronic issue here
Food need not go to waste. Today, with technology getting more sophisticated, even common food sources and scraps can be turned into plastic material! Considering the prevalence of food shortages, repurposing it into something practical, yet highly valuable, is a virtuous move.
New technologies on bioplastics, materials that are derived from renewable biomass, are lifting the burden on petroleum as the chief resource for producing plastics.
When landfilled, food wastes release greenhouse gases, alleged to be 25 times more harmful than carbon dioxide. Thus, bioplastics not only lend the opportunity to tap into food to develop a high-value raw material but also to produce material with lower carbon footprint and lower toxicity.
Cost-effective process for producing PHAs
Cost is also another factor. Full Cycle Bioplastics (FCB), collaborating with California-based Fresno State University, has successfully been able to upcycle organic and cellulosic waste, including food, agricultural by-products, as well as cardboard and waste paper, into fully compostable polyhydroxyalkanoates (PHAs), in a cost-effective process.
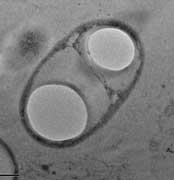
In its patented process, waste is broken down and becomes feedstock f o r PHA. On c e the feedstock is perfectly adjusted, it is dosed into a tank of naturally occurring bacteria, where it is consumed and converted into PHA. FCB says no Genetically Modified Organisms (GMOs) are used in the process, thus significantly lowering production costs and eliminating the need for expensive laboratory-grade sterility or containment, unlike PHAs produced by other processes. In the last step, the PHA is dried and processed into a finished resin product, ready for compounding.
The advantage of PHA is that it naturally degrades in marine and terrestrial ecosystems, unlike petroleum-based plastics like PE and PP, plus it caters to broad commercial application potential, including commercial food-grade packaging and agriculture films.
FCB, which works with waste producers and licenses its technology, is seeking partners with experience compounding PHA and other bioplastics such as PBS, PBAT, PLA and starches.
Nourishing biobased goals with milk-derived feedstock
Founded in 2014, French start-up Lactips has been making plastic out of casein, the main type of protein found in milk, on an idea that started as a research project at the University of Saint-Etienne and was under development for seven years.
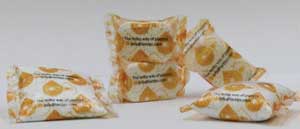
Using similar machinery available in the market, Lactips’s thermoplastic pellets can be extruded into compostable biodegradable films, said to biodegrade within 18 days. The Lyon-based firm currently uses milk powder produced in Eastern Europe, but is looking into using milk waste.
The bioplastic will make its commercial debut later this year as wrapping for dishwasher detergent. Because it’s soluble in water, the wrapping disappears during washing and degrades naturally in the environment. Besides water soluble films, the edible plastic, which also has oxygenbarrier properties, is targeted at novel edible packaging applications.
A year after receiving funding of EUR1.2 million from European private equity fund Demeter and Emertec, Lactips has recently received a European subsidy of EUR1.5 million over two years. It expects to set up a facility by 2018, to tackle the international market.
The sea’s answer to green materials
Adhesives that work even when submerged in water are underway. In a project funded by the US Office of Naval Research, scientists from Purdue University have found a clue from mussels for adhesive material, inspired by shellfish’s ability to stick to surfaces under water.
Citing current commercial adhesives poor at wet bonding, the researchers say that mussels, barnacles, and oysters can attach to rocks with apparent ease. In order to develop new materials able to bind in harsh environments, the team made a biomimetic polymer that is modelled after the adhesive proteins of mussels.
The findings, published in the ACS Applied Materials and Interfaces journal, showed that the biobased glue performed better than ten commercial adhesives. Compared with the five strongest commercial glues, the new adhesive performed better when bonded with wood, Teflon and polished aluminium.
How mussels do their sticking stunt is by extending hairlike fibres that attach to surfaces using plaques of adhesive. Proteins in the glue contain the amino acid, DOPA, which harbours the chemistry needed to provide strength and adhesion.
The researchers incorporated this chemistry of mussel proteins into a biomimetic polymer called poly(catecholstyrene), creating an adhesive by harnessing the chemistry of compounds called catechols, which are contained in DOPA. While most adhesives interact with water instead of sticking to surfaces, the catechol groups may have a special talent for “drilling down” through surface waters in order to bind onto surfaces.
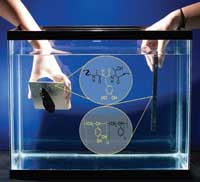
The new adhesive is about 17 times stronger than the natural adhesive produced by mussels, and this discrepancy is not unusual in biomimetics, when mimicking natural materials and compounds, with future research to include work to test the adhesive under real-world conditions.
Bioplastics from crustaceans are also making ripples in the research facility of Egypt’s Nile University. The researchers, in collaboration with UK’s University of Nottingham, are looking at the viability of chitosan, a fibre found in a substance called chitin that develops in the hard outer shells of crustaceans.
Egypt imports around 3,500 tonnes of shrimp, which
produce 1,000 tonnes of shells as waste, making it a
lucrative feedstock for bioplastics. The shells are cleaned,
chemically treated, ground and the dried chitosan flakes
dissolved into a solution that can be turned into polymer
film by conventional processing techniques.
The technology has potential for large-scale industrial production, say the researchers, but having only produced small samples, the project is not yet ready to go into commercial production, since properties like thermal stability and durability need to be further improved.
Chitosan was chosen because it is a promising biodegradable polymer already used in pharmaceutical packaging due to its antimicrobial, antibacterial and biocompatible properties. The second phase of the project is to develop an active polymer film that absorbs oxygen.
If successful, the UK university plans to approach UK packaging manufacturers with the product. Additionally, the research aims to identify a production route by which the degradable biopolymer material for shopping bags and food packaging could be manufactured.
Diapers/packaging made from cornstarch
Disposable diapers are among the top waste proliferators and in the US alone, an estimated 20 billion disposable diapers or 3.5 million tonnes/year of waste go to landfills, according to the US Environmental Protection Agency (EPA). The diapers, especially the lining made of plastic, take 500 years to degrade, releasing methane and other toxic gasses as they break down.
In view of this, US-based start-up Tethis has developed a
biodegradable material made from corn starch for the diaper
industry, as well as for other applications like feminine hygiene, wipes, for personal care products, and others.
Tethex is a super absorbent polymer (SAP), based on a
patent-pending technology platform, that boasts superior
performance in highly ionic fluids such as seawater, hard
water, divalents, oil, and blood, says the firm.
Tethis, which began in 2013 as a spinout of novel technology discovered at NC State University aimed at the water treatment market, is able to produce about 700 tonnes/ year of the biorenewable polymer at its facility in North Carolina. It expects to increase production to 10,000 tonnes by 2018.
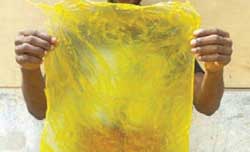
Meanwhile, in a similar effort, the Department of Energy and Environmental Engineering of the Ghana-based University of Energy and Natural Resources (UENR), has also developed biodegradable plastics from corn starch that come in a variety of soft, semi-soft and hard textures. The polymer degrades within one month, is edible, and may be used for packaging. Further research to improve the innovation for utilisation in industry-scale is being undertaken by the university.
Sweet prospects for bioplastics from sugar
India-based cutlery maker Pappco is “greening” India with its take on biodegradable disposable plates, cups and glasses manufactured using bagasse from sugarcane, bamboo and wheat straw as well as corn and potato starch. Set up in 2011, the company says while costing slightly higher, the products are also comparatively firmer and more durable than plastic counterparts.
Another “sugary” innovation has been developed by the VTT Technical Research Centre of Finland, producing furan dicarbonic acid (FDCA) from plant sugars for the production of drinking bottles, paints and industrial resins. VTT has patented the method for producing FDCA, a monomer for PEF polymers, from sugar or sugar waste. Thanks to the solid acid catalyst and biobased solvent with short reaction time, the method provides a considerable reduction of toxic waste compared to traditional methods, VTT said.
The project, which is funded partly by Tekes, the Finnish funding agency for technology and innovation of the Ministry of Employment and the Economy, is aimed to provide a renewable option for making bottles, which to-date is still dominated by oil-based PET. The method can be scaled-up to industrial purposes without substantial investments, and it has already raised a lot of interest in industry, according to VTT.
Following the trend for biobased, albeit non-food, PET bottles are bottled water companies Danone and Nestlé Waters, who have teamed up with California-based startup Origin Materials, to launch the NaturALL Bottle Alliance. The R&D partnership will be developing and launching at commercial scale a PET bottle made from 100% renewable, biobased material, such as used cardboard, sawdust and wood chips, so it does not divert resources or land from food production.
Danone and Nestlé Waters are providing expertise and teams, as well as financial support, to enable Origin Materials to make this technology available to the market.
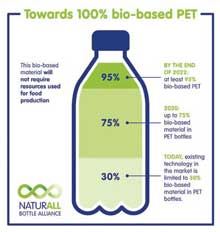
There are already 30% bioPET bottles in the market and Origin Materials has already produced samples of 80% biobased PET in its California pilot plant. Construction of a pioneer plant is commencing this year, with production of the first samples of 60+% biobased PET to start in 2018.
The Alliance plans to have an initial volume of 5,000 tonnes of bioPET. By 2020, it aims to develop the process for producing at least 75% biobased PET bottles at commercial scale, scaling up to 95% in 2022. The partners also said they will continue to conduct research to increase the level of biobased content, with the objective of reaching 100%.
Films take the cake
European experts are taking a crack at discarded bread crust, sponge cake and stale bread to obtain a 100% biodegradable PLA film from bakery waste, as opposed to PLA from cornstarch.
The research consortium is coordinated by Spain’s Research Association of Plastics and Related Materials (AIMPLAS), with the Technological Centre of Cereals (Spain), the Institute of Agriculture (Germany), and the Biocomposites Centre of the University of Bangor (UK).
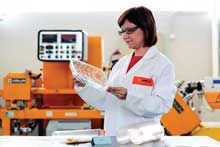
The study called Bread4PLA is looking at a new way of treating bakery waste to allow for new packaging for bakery products and to close the life cycle loop. The PLA material can be made into bags/trays for the packaging of different bakery products. The production of PLA is via a low-energy process that uses water-based enzymes on a large pilot-plant scale.
Magic mushroom as biopolymers
US-based Ecovative has developed a biodegradable plastic called Mushroom Materials, made from agricultural by-products and mushroom mycelium, which is the vegetative part of a mushroom fungus and a natural glue. The material binds with crop waste like seed husks and corn stalks to form the fully biodegradable bioplastic.
Its product range includes MycoFoam to replace plastic foams like Styrofoam. In its range is Mushroom Packaging — a protective packaging product used by companies like Dell and Stanhope Seta; as well as Mushroom Insulation, acoustics, core materials, and aquatic products.
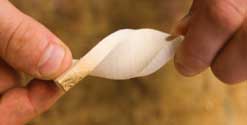
It’s most recent development is MycoFlex, made entirely of mycelium. The firm says it is developing it through grant funding as a replacement for all cushioning like shoe soles, seat cushions, yoga mats, lightweight core materials, and a variety of other uses.
As it can be seen there are a chockfull of renewable food (as well as non-food) feedstocks currently being explored by the industry that is relentless to serve up eco-friendly solutions to consumers with an insatiable appetite for sustainable innovations.
(PRA)Copyright (c) 2017 www.plasticsandrubberasia.com. All rights reserved.