Extrusion Machinery
Virtual displays from W&H and Bandera
The Covid-19 pandemic has changed the way businesses have to operate, given the tighter restrictions.
German machine manufacturer Windmöller & Hölscher (W&H), which had initially planned to exhibit at the Interpack and Drupa exhibitions that have been postponed until 2021, held its first Virtual Expo to present technologies and products. Held over two days from 24-25 June, over 2,000 visitors from 120 countries tuned in for live flexographic and gravure press demonstrations, technical sessions and virtual meetings.
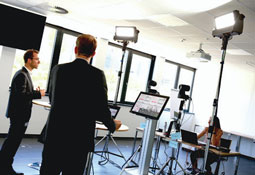
“The past months have been a challenge everywhere. Yet the flexible packaging industry is as busy as ever. That’s why it was so important for us to hold a Virtual Expo and show our customers new technologies and applications that are available now and can help them run their production more efficiently,” said Peter Steinbeck, Managing Partner at W&H.
To accommodate different time zones of visitors, the Virtual EXPO was held live three times a day. Filmed in the 120,000 ft2 W&H Technology Centre in Lengerich, Germany, and the W&H Academy, two live machine demonstrations and eight technical sessions were broadcast live.
The live machine demonstrations included the Novoflex II flexographic press highlighting the new RUBY IoT system for analysing production data to optimizse processes and the newly redesigned Heliostar II gravure printing press.
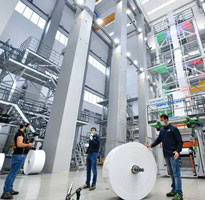
The live technical sessions were targeted to package printers, industrial sack producers, paper bag manufacturers and film extruders. A session showcasing an All-PE film structure as an alternative to PET for stand-up pouch applications was said to have generated significant interest.
Other technical sessions covered flexible packaging topics, including sleeve handling solutions for flexographic presses, printing solutions for industrial sacks, heavy duty films for FFS sacks, remote service and paper sack production on machinery from W&H subsidiary, Garant Maschinen.
Meanwhile, Italian extrusion machinery maker Bandera also organised Open House sessions in live streaming where it presented its new HDBFlex five-layer co-extrusion technology.
The Open House started in May with a first private session dedicated to the final purchaser of the line, allowing the firm to preview the running line, verifying its production parameters and the structure of the event live. Three live streaming sessions were transmitted in two days, respecting the different time zones of the customers.
Over 500 customers, potential customers and suppliers attended the live streaming presentation of the HDBFlex line – Heavy Duty Bag Flex. Its partners included materials firms Borouge/Borealis, Frilvam (masterbatches manufacturer from Varese) and Industria Creativa, an agency specialising in digital communication.
Reifenhäuser conver ts line for protective garments; Nordson steps up flat dies
The Covid-19 crisis has seen a high demand for global production capacity for hygiene products. In March this year, machinery maker Reifenhäuser has temporarily produced metlblown to produce roughly 1 million face masks/day at its Technology Centre. The company has now converted another pilot line for production. The first batch will produce 110 tonnes of protective film for a global manufacturer for medical coveralls for use in hospitals. The increased demand is currently very high for coveralls worn to treat highly infectious coronavirus patients. This volume is sufficient for about 1.2 million overalls.

Reifenhäuser, the manufacturer of plastics extrusion lines, normally uses the Technology Centre to research and develop new applications in collaboration with its customers. The film protects against infections but allows air exchange, which is vital for hospital workers who must wear overalls for long periods of time. Breathability comes from the pore structure in the material which is produced by a special calcium carbonate addition followed by a stretching process (Reifenhäuser EVO Ultra Stretch).
The same line type is capable of producing hygienic film for use in diapers, besides certified medical protective film. Ultra Stretch technology can also be used in other advanced applications, such as recyclable All-PE film (PET replacement). The production unit can therefore be used flexibly to respond to a wide variety of market demands outside of an emergency or crisis.
Meanwhile, the surging demand for devices that protect against Covid-19 includes sheet and coated fabrics whose manufacture calls for flat die systems that in pre-pandemic days often had quite different uses, reports Nordson Corporation
“Our company’s EDI Ultraflex sheet extrusion dies have been put into service for producing PVC, acrylic, and polycarbonate shields, face guards, sneeze guards, and barriers and our Premier fixed-lip slot dies are now used for coating fabrics and filter membranes specifically intended to protect against Covid-19,” said Patrick Meinen, Global Product Line Manager.
(PRA)
Subscribe to Get the Latest Updates from PRA Please click here
©2020 Plastics and Rubber Asia. All rights reserved.

©2020 Plastics and Rubber Asia. All rights reserved.
Home Terms & Conditions Privacy Policy Webmail Site Map About Us