Indian Machinery & Technology: India’s machinery makers embrace challenges
Also, download this story from the electronic issue here
The plastics industry is one of India’s major engines of growth that looks ahead to a year of increasing growth rate and expanding markets, adapting well to the flux as opportunities for varied applications for plastics continue to rise, all this against the background of a slowing GDP, the demonetising policies introduced last year and the impending implementation of GST this year.
For many economies worldwide, the previous year, emblematic of events that challenge established beliefs and standardised political frameworks, has epitomised the axiom that the only permanent thing (on earth) is change.
The new year brings a mixed bag of opportunities. On the one hand it has traces of the spillover impact of 2016, yet at the same time there are cues for a more optimistic outcome. Fortunately for the Asia-Pacific region, likewise vulnerable to global risks, it is able to maintain its momentum amid soft growth prospects.
In the region and the world, India has become a benchmark for growth. But again, what has been “set in stone” for many years in the past has been challenged after the Indian government demonetised high value currencies (in a bid to crack down on corruption and terrorism) last year. Though the move, critics say, may keel over India’s “world’s fastest economic growth” claim, especially since the International Monetary Fund (IMF) has downgraded the country’s growth projection, yet there are more positive than negative outcomes from this strategy. Economists at the Moody’s Investors Service and India-based affiliate ICRA Ltd project that the disruption is only short-term; and by mid-year, India’s economy will start to pick up.
As for the country’s plastics industry, consultancy firm Lucintel forecasts the plastic pipe market to grow at a CAGR of 10.4% from 2016 to 2021, owing to the growth of the building/ construction and infrastructure sectors.
Engineering plastics have a potential CAGR of over 13% from 2015-2020 report, finds TechSci Research. It attributes this growth to demand from diverse industries including automotive, electrical & electronics, construction, and others.
As well, the country has a lucrative demand for highperformance plastics, notwithstanding its burgeoning requirement for plastic packaging, forecast to reach US$73 billion by 2020, according to the Federation of Indian Chambers of Commerce and Industry (FICCI) and Tata Strategic Management Group (TSMG).
Metamorphosis to a global leadership
Extrusion and thermoforming machinery maker Rajoo Engineers is an example of success that follows changes. The Gujaratbased manufacturer describes its more than three decades of providing technology solutions for the plastics industry as a “quick metamorphosis” from its modest beginnings in 1986 in the Gujarat town of Rajkot to its current global status with offices in India and overseas.
Technology-driven, Rajoo Engineers ushers in 2017 with new developments that will help sustain the growth of the plastics industry.
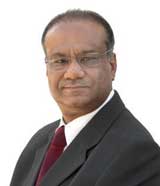
In an interview with PRA, Sunil Jain, President of Rajoo, when asked what Rajoo expects as well as aims for this year, replied, “At Rajoo, in 2017, our focus will be on highoutput barrier and nonbarrier films lines, in addition to high-output sheet extrusion lines. Thus, offering a complete barrier packaging solution to the industry, an application poised for exponential growth owing to the entry of organised retail in India. At the same time, our focus on exports will be further increased.”
While Rajoo has forged strategic partnerships with firms like Italian pipe machinery maker Bausano, German blown film machine maker Hosokawa Alpine and Meaf Machines of Netherlands, Sunil says the company is continuing to chalk up other plus points.
“Rajoo has several firsts to its credit, not now but since its inception. We have brought world-class affordable technologies to the industry in India, even in the past, and we continue to do so now. Offering import substitution to the industry has been our forte. Our sister company has successfully introduced machines for producing WPC (Wood Plastic Composite), which is a substitute for wood. Yet, another environment friendly technology offered by our company.”
As regards plasticulture, Sunil says the firm is
now executing a project for an Indian customer for
a seven- layer barrier, 4.2 m-wide blown film line to
produce agriculture
films. “This will
yet be another first
in the industry in
Asia from Rajoo.
The slated output to
produce barrier film
is 1,500 kg/hour and
is targeted for various
applications – FIBC
liners, canal lining
and agriculture films.”
Meanwhile, its other
latest technology,
Pentafoil five-layer
barrier film line,
introduced at the
K2016, is specifically targeted to produce all polyolefin films for
packaging, which are fully recyclable unlike films
with barrier polymers. “It also offers benefits of
down-gauging, thus reducing the overall usage of
plastics. Energy consumption is yet another ecofriendly
parameter and this line has been certified
by TUV at a never before 0.3001 kwH/kg of film,”
claimed Sunil.
As for industry 4.0 or IoT-ready technologies, Sunil remarked, “From the perspective of Rajoo Engineers, there are two focus domains: automation and data exchange in manufacturing technologies in making machines on one hand and our machines being automated and using cyber technology controls.”
He adds that the firm has taken steps in both directions. “Cloud-based ERP for creating a virtual factory is already under implementation. Further, our customers using high-output blown film lines already get internet-based remote support. Similar technologies are also being introduced in our complete range of machines. However, bandwidth and speed for internet access continues to be challenge.”
Dealing with skills shortages
While the availability of technology is aplenty, India’s plastics sector has a downside though as explained by Sunil. “The skills pool to support the plastics manufacturing industry in India is scarce and it has reached a critical stage and is a major issue. While the government of India and our association – Plastics Machinery Manufacturers Association of India (PMMAI) – of which we are one of the founder members, have taken effective steps in this direction, Rajoo on its own has launched a unique initiative, a first by an Asian plastics machinery manufacturer in the blown film and sheet extrusion segment.”
The company is in the midst of setting up the Rajoo Innovation Centre, based in Rajkot, to be up and running in the middle of 2017. “It will be equipped with a state-of-the-art seven-layer blown film line and a barrier sheet extrusion line and will impart training to develop a skills pool for the industry. In addition to contemporary testing facilities, it will also provide an impetus for development of barrier packaging materials,” revealed Sunil.
While there are challenges on the horizon, Sunil is optimistic of the future. “The demonetisation drive launched by the government of India may have been disruptive but it is a bold step forward. We foresee it affecting the whole economy in the short term including the growth of the plastics industry. The introduction of GST, yet another major economic reform to be introduced in 2017, will positively enhance the “ease of doing business”. Our targets for 2017 will factor the above major initiatives in the country,” he concluded.
Mamata “exports” US technology to India
Another Gujarat-based machinery maker,
Mamata Machinery, which makes converting and
extrusion machinery, is expanding in the North
American market, where it has already installed
200 servodriven-bag and pouch making machinery.
The company first entered the market with a 5,000
sq ft-sales and service centre for pouch making
machinery in Illinois in early 2000. Later, in 2010, it
set up a 12,500-sq ft facility in Florida.
“The US-based team of engineers designs and manufactures these packaging machines. We now offer horizontal form, fill and seal; high-speed pouch fillers; and multi-lane sachet packaging machinery in the US,” said Apurva Kane, Senior Vice-President.
Speaking to PRA at the K2016 show last year,
Kane, added, “The machines produced in the US are
not only of a high speed but are produced in a high
hygiene environment, making them suitable for
use in the packaging of foodstuff, like dry products
such as oatmeal and dry fruits and nuts.” Such
machines have been installed at one of the world’s largest pistachio packer Growers Express’s facility in
California, a co-packer for Green Giant, shared Kane.
This technology is now being brought back to India. “Some of the major advancements in the packaging sector are taking place in the US. Our strategy is to hire design talent in the US to develop the equipment that is up-to-date and offer it to the rest of the world by leveraging the cost efficiency of producing it in India,” explained Kane.
He also said that though the machines will be priced slightly higher than locally made-in-India machines, the company will offer greater valueadded technology to the market.
The Ahmedabad-headquartered company also claims a first in the industry: the fastest bag making machine for non-woven reusable bags. “This machine is three times faster than the machines produced in China. It has an output of 160 bags/ minute, compared to the usual 40-50 bags/minute,” claimed Kane, adding that the prototype will be commercialised in the market soon.
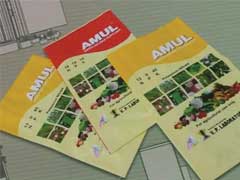
At the K show, it had another first: a high-speed bag maker for converting PP woven fabric into sacks and pouches for bulk packaging of commodities. The machine is completely automated; with sheet-onroll, it forms side gussets and undertakes back seam gluing as well cuts to required lengths; folds and stitches the bags. “It is able to convert bags from 5 kg up to 25 kg size that can be used for packing rice, pulses and garden manure. With an output of 60 bags/minute, it is the fastest in the world.”
As for future machinery launches, Kane said Mamata is researching into liquid packaging. “We are targeting the production of in-line machines for packaging with spouts, for normal liquid juices, edible oils and drinks,” he added.
(PRA)Copyright (c) 2017 www.plasticsandrubberasia.com. All rights reserved.