Erema’s ReFresher for nicer smelling PCR material
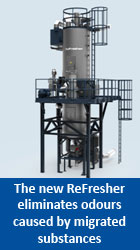
With the presentation of ReFresher at the K2016 trade fair last year, Austrian recycling equipment maker Erema says it achieved a breakthrough in the post-consumer sector with its odourless recyclate that opens up a multitude of new sales markets for recyclers and producers.
Erema now says its customers will have access to a mobile ReFresher for test purposes to enable them to carry out on-site trials and evaluate results. The investment is, thus. designed to meet the exact odour requirements of the desired end application.
Post-consumer material, especially household packaging waste, is considered to be plastic which is difficult to recycle due to impurities and the fluctuating degree of contamination. These contaminants often cause an unpleasant odour in the recyclates which severely limits the scope of use with the end products.
"We recognised the potential of continuously increasing packaging waste early on and worked intensively on finding a technical solution for the odour issue. With the ReFresher we offer recyclers and producers the edge in terms of quality to establish themselves in the marketplace with odourless recyclates from household waste," says a confident Manfred Hackl, Erema CEO.
The ReFresher eliminates odours caused by migrated substances, i.e. residues left on the plastic materials. These include, for example, food contamination, cleaner/detergent residues and cosmetics.
The ReFresher is downstream of the extrusion process and keeps the recyclates at the required temperature at which volatile materials can be discharged. The equipment is available in various expansion stages depending on the end application.
It is based on the proven TVEplus technology
and now offers filtrated, degassed and odourless recyclates for the first time in post-consumer recycling – even in the case of severely contaminated packaging waste.
The Intarema TVEplus prevents unpleasant odours from developing in the course of the extrusion process. In conventional processes these develop, for example, through cellulose contamination such as wood or paper which burn during extrusion and transfer the smell to the plastic. The interplay of preconditioning unit, Airflush technology, low melt temperature, efficient filtration and several degassing steps ensures that the cellulose particles are separated from the plastic.
"At the end of the extrusion process what we have in our hands is high-quality recyclate which is already suitable for many applications. And here I am referring to extrusion products such as pipes or film in the waste management or construction industry. The odour caused by migrated substances, however, is more stubborn. End products such as plastic parts in cars or in the home call for an additional recycling step to neutralise the odour. And this is exactly what we developed the ReFresher for," explains Clemens Kitzberger, Post Consumer Business Development Manager at Erema.
TVEplus technology has a market share of around 85% in the post-consumer sector in Europe alone. "I am sure that the ReFresher will be another boost for the use of recyclates from post-consumer material. Whether it is in supermarkets or homes – I assume that we will come into contact with this type of odour-treated recyclate more and more in the future," says Clemens Kitzberger.
(PRA)Copyright (c) 2017 www.plasticsandrubberasia.com. All rights reserved.