Machinery: Kautex expands German facility; Boston Matthews adds on resources/technology
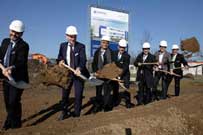
German extrusion blow moulding machine maker Kautex Maschinenbau is continuing to drive forward with its growth plans. In order to meet rising demand for its recently developed, all-electric packaging machines and compact suction blow moulding machines, the company is expanding and modernising its Bonn production location. From Q3 2017, the new 5,000 sq m assembly hall will mostly be dedicated to assembling and testing KBB-series packaging machines and KSB-series suction blow moulding machines. Along with this, around 80 office workplaces are also being built.
Kautex CEO Dr. Olaf Weiland hopes that the plant expansion will make production even more efficient and further reduce lead times for customers: “As well as improving the long-term performance and efficiency of our machines, we want to make the same improvements to our production.”
Meanwhile, Kautex says it finished fiscal 2016 on a high with record sales of EUR122 million. Weiland sees the sector heading in a positive direction, hence the focus on the company’s Bonn HQ. “Bonn is located in the heart of one of the world’s most important centers for plastics manufacturing. The high density of universities and the presence of specialist research institutes offer excellent development opportunities for our innovation-driven sector,” comments Weiland on the city where the company was founded over 80 years ago. Kautex Maschinenbau has its own technical centre in Bonn, which is itself one of the world’s largest research and development institutes for plastics machinery.
In other news, UK-based extrusion machinery manufacturer Boston Matthews has expanded its engineering department,
with the addition of resources and investment in technology hardware. The company says this is to meet growing demand worldwide, across a wide range of industries.
Mechanical and electrical design engineers will work on both the Boston Matthews extrusion machinery and Munchy Recycling machinery, utilising the latest 3D CAD technology within the company’s design centre. Additions have also been made to the electrical design team, which develops and designs the electrical schematics for individual machines and complete turnkey installations. An investment has also been made into new electrical design software packages for this area of the business. An experienced control systems engineer has been assigned to the design department to develop and write PLC and motion software for the company.
"The decision to take on more design engineers is a big investment and, therefore, was carefully considered," said Managing Director Simon Brookes. “Technological innovation and the constant drive for product improvement is at the heart of Boston Matthews and (maker of recycling equipment) Munchy, and it is imperative we have the experience and skills to accomplish this. We are experiencing a high level of demand for our products because of our ability to work with customers and take them to the next level, which is fantastic, but it does place particular demands on engineering. The new additions to our team have been very carefully selected to add to our already highly experienced and skilled design team.”
Investments in technology include high-precision machine component manufacturing equipment and precision digital measurement equipment, to enhance the design and manufacture of complex die heads, tooling and other precision component parts. “We try to keep as much manufacturing in-house as possible to enable us to incorporate any design improvement as quickly as possible. It also greatly improves our R&D capabilities,” said Brookes.
The 50-year old company invented the caterpillar haul-off machine and says there are more than 10,000 machines in use worldwide. It was also the first to manufacture a 150 mm extruder for processing polyurethane. It operates facilities in the US, UK and China. It acquired recycling machinery maker Munchy in 2002. Munchy invented the dual-diameter screw, which enables the recycling of plastics into pellets.
(PRA)Copyright (c) 2017 www.plasticsandrubberasia.com. All rights reserved.