PRA Chinese
Rubber Journal Asia Injection Moulding Asia Energy, Oil & Gas Asia
VISIT OUR OTHER SITES:
PRA Chinese
Rubber Journal Asia
Injection Moulding Asia
Energy, Oil & Gas Asia
Plants: BASF inaugurates the second phase of antioxidants plant in Shanghai; Sasol ups ethane cracker output after catalyst replacement
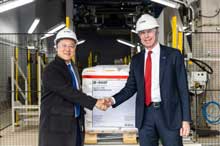
German chemical firm BASF has inaugurated the second phase of its new, world-scale antioxidants manufacturing plant at its Caojing site in Shanghai, China. The second phase comprises a synthesis plant to produce the antioxidants Irgafos 168 and Irganox 1076. With the completion of the second phase, the plant will have an annual capacity of 42,000 tonnes, mainly serving customers in China.
The units for liquid antioxidants, formgiving, and powder blending were inaugurated in January 2019 as part of the plant’s first phase. It was the first time BASF used a modular concept to build a plant. This enabled the completion of the project in just ten months – half the time of an onsite build. Ten plant modules with a weight of up to 440 tonnes/module were pre-fabricated off-site in just 230 days. They were then assembled at the site in only five days after undertaking a 24-hours journey on the Yangtze River and the East China Sea.
The process technology of the new plant also has a lower energy intensity and less waste is generated per ton of products manufactured. For example, the plant will reuse much of its process water for production and a different drying technology is used to reduce solid waste.
Thanks to these features, the plant has recently been awarded a grant of RMB50 million (approximately EUR6.5 million) by the Shanghai government..
Antioxidants help prevent thermal oxidation reactions when plastics are processed at high temperatures. Oxidation can cause the loss of impact strength, elongation, surface cracks, and discoloration of the materials. Almost all polymer materials undergo oxidative degradation reactions at one or all of the manufacturing, processing and end-use stages.
BASF runs a global production network and is the only supplier of antioxidants with production sites in Asia, Europe, North America and the Middle East.
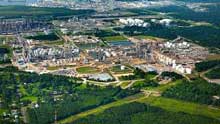
Meanwhile, in other news, chemical firm Sasol says its Lake Charles ethane cracker in the US is increasing production rates following the successful replacement of the acetylene reactor catalyst. The ethane cracker achieved beneficial operation in August 2019 but has run approximately 50-60% of nameplate capacity due to underperformance of the plant's acetylene removal system. This issue has now been resolved, says Sasol.
The outage to replace the catalyst was successfully completed on schedule and within budget. Following the outage, the unit was started up smoothly and ethylene production rates are approximately 85-90% of nameplate capacity and are increasing. Ethylene quality meets US Gulf Coast ethylene pipeline specifications.
Sasol says it also looks forward to the completion of the Lake Charles low Density polyethylene (LDPE) unit, which is being commissioned with beneficial operation expected later in December 2019.
The remaining three downstream units under construction to complete the integrated Lake Charles site, ziegler alcohols and alumina, alcohol ethoxylates, and Guerbet alcohols, remain on cost and schedule as per our previous guidance.
(PRA)
Subscribe to Get the Latest Updates from PRA Please click here
©2019 Plastics and Rubber Asia. All rights reserved.

©2019 Plastics and Rubber Asia. All rights reserved.
Home Terms & Conditions Privacy Policy Webmail Site Map About Us