Arlanxeo opens technology centre in China; introduces sustainability to EPDM plant
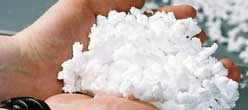
Synthetic rubber materials maker Arlanxeo says its Rubber Technology Centre (RTC) in Changzhou, China, not only boasts advanced analytical testing capabilities but is located within the premises of its EPDM plant, and is one of its global rubber testing centres.
In fact, the joint venture company says it now offers the most comprehensive rubber laboratory in China as it is capable of testing and mixing a great variety of rubber products.
“We believe that this move ties in with our focus of serving our customers better by improving our systems and processes in the APAC region. The new RTC will continue to strengthen Arlanxeo’s product portfolio to meet the region's growth potential,” said Jan Paul, CEO.
Together with the butyl rubber and Nd-BR plants in Singapore, the EPDM plant in China make up the three newest and most advanced plants of Arlanxeo – all in APAC. The new RTC also brings together the firm’s testing, mixing and production capabilities under one roof in China.
“The consolidation of our testing and mixing capabilities and the production strength of the EPDM plant in China has not only made Arlanxeo well-placed to meet the challenges currently presented by the market situation, but also underscores the importance of China and the APAC region,” continued Paul.
The new RTC at the EPDM plant is also part of its strategy to build closer ties with local partners and customers via cooperation and collaboration.
The development of the RTC began at the Lanxess Rubber Research Centre in Qingdao, where it started off as a chemistry and analysis laboratory in 2008. Since then, the centre has developed over the years, including merging with Arlanxeo’s APAC technical centre in Shanghai and adding more competencies and cutting edge equipment, before starting full operations as the all-new RTC at the EPDM site in Changzhou.
The RTC is made up of five different laboratories, to cater for mixing, rheological, physical testing, wet and analytical testing operations. The laboratories are currently led by two teams: the Rubber Mixing team and Rubber Testing team. These factors come together to make the RTC a holistic service and solutions provider, with the potential to act as a platform for technical exchanges.
The EPDM plant in Changzhou has a nameplate capacity of 160,000 tonnes/year and commenced operations in 2015. Meanwhile, the company says it is developing a more sustainable EPDM production technology. According to Niels van der Aar, Arlanxeo’s Head of Technical Service and Application Development for Keltan Elastomers, “Key examples include the use of Keltan ACE catalyst technology, and the recent introduction of Keltan Eco EPDM grades, the world’s first EPDM rubber based on bio-ethylene.”
Keltan ACE technology was introduced at its largest plant in Geleen (The Netherlands) and in Changzhou (China). As the Keltan ACE catalyst is extremely productive and polymerisation can take place at much higher temperatures than the conventional Ziegler Natta catalysts, the new post-metallocene technology is said to be energy efficient. Customers have evaluated, approved and implemented the Keltan ACE grades in the market since 2013, says the company.
Keltan Eco EPDM is a recent development, produced from bio-based ethylene, supplied from Brazilian materials supplier Braskem S.A., which originates from sugar cane. Depending on the ethylene content of the particular grade, the bio-based content of Keltan Eco EPDM rubber ranges between 50% and 70%. Detailed studies have shown that the polymer characteristics and the technical performance of Keltan Eco EPDM are identical to those of the corresponding conventional products. Independent Life Cycle Assessments of the eco-EPDM grades versus their equivalent Keltan EPDM product have shown that the CO2 emission is reduced by more than 50%, saving the emission of 4-6 barrels of oil used for production per mt EPDM. The new bio-based EPDM grades are commercially applied in applications, such as low-weight, micro-porous automotive solid seals, recyclable TPVs, flooring and window seals.
“Our commitment to sustainability goes beyond our products”, says Niels van der Aar. “Recently, Arlanxeo published extensive studies on increasing the sustainability of thermoset compounds by combining Keltan Eco with sustainable alternatives for plasticiser oils and fillers.”
Arlanxeo, with sales of around EUR2.8 billion in 2015, about 3,800 employees and a presence at 20 production sites in nine countries, was established in April 2016 as a joint venture of Lanxess and Saudi Aramco.
(PRA)Copyright (c) 2016 www.plasticsandrubberasia.com. All rights reserved.